Indoor high tech transfer
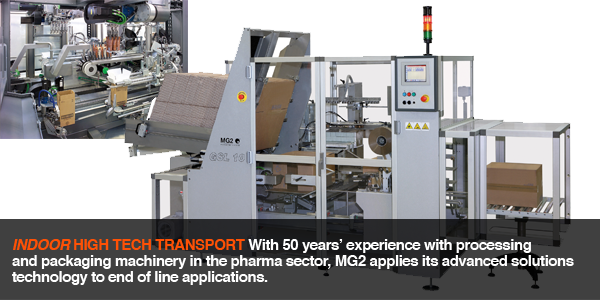
EXPERIENCE What do a capsuling machine and a palletisor have in common? The builder’s knowhow. With fifty years’ experience with processing and packaging machinery in the pharmaceutical sector, MG2 applies its advanced solutions technology to end of line applications. The latest developments below.
A wide and complete range that spans the most sophisticated capsuling machines and automatic syringe assembly machines, now extending to end of line for pharmaceuticals, chemicals, cosmetics and food. And that’s not all: thanks to a partnership with other builders, MG2 (Pianoro, BO) is able to supply complete primary and secondary packaging lines, for example for packaging syringes, capsules, coffee pads and more.
With this line-up, the Emilian enterprise has during the course of the last 16 years (the company is nearly 50) integrated its historic specialization in the construction of machinery for pharmaceuticals with new end of line solutions, developing horizontal and vertical casepackers, formers, fillers and closure systems for displays, boxes or trays, palletizers…
Family traits
What unites all these proposals is, first and foremost, the degree to which they lend themselves to integration and connectivity. MG2 solutions can be easily connected online with components upstream and down, as well as integrated with remote control systems, barcoding systems, RFID scanners, inkjet printers and complete units for track & trace. Furthermore, the concern’s own technology is based on designing servo-assisted systems, characterized by few mechanical components and capable of guaranteeing maximum performance, but also quick and easy maintenance and changeovers. But at the same time, these are always tailor-made systems: adapted to the needs of each user, for integration with existing layouts and executing different runs with maximum efficiency and economy. The concerns for end of line are no exception, and, what’s more, they benefit from the long experience of the concern’s designers. Below are some examples of this admirable approach and the results it has yielded.
GSL10 is a horizontal casepacker that forms, fills and closes American boxes (1). With an ergonomic design, this system securely and forcefully opens the box, guaranteeing the reliability of both the feed and positioning of the products and a quick and easy format changeover. Both adhesive tape and hot glue closure systems are available.
The GSL10 can process up to 10 boxes/min, depending on the container format and the position of the product within, and can be supplemented with optional components such as barcode scanners, inkjet printers, labelers or a scrapping station.
The palletisor/de-palletisor GRP features an anthropomorphic robot that guarantees high performance and great flexibility. Its modular structure enables the user to set it up as needed: with one or two palletisation areas, automatic empty pallet feed (with empty pallet storage and full pallet outfeed), warehouse and layer divider feed.
This solution enables switching between European and American pallets with the addition of just two dividers. Moreover, it makes it possible to rearrange the products with ease at any time, and the pallets can carry loads up to 2,200 mm in height.
Most suitable for vertical and horizontal MG2 casepackers, GRP can be interfaced with any other machine.
GTL30 is a vertical casepacker that is easy to use and clean of any cardboard trimmings, since it is made completely accessible by its cantilevered design (2). This solution offers the perfect balance of quality mechanics that enable opening and manipulating the box, advanced electronics that adopts brushless motors for the primary motions, and pneumatics used in secondary motion. Format changeover requires no replacement parts, but operates through handwheels that adapt the machine to the new box size.
Available in two versions (GTL30 and GTL30/L), for processing American boxes of two different format ranges with hot glue or adhesive tape closure, this solution offers different feed systems (the products can be positioned to the right or to the left of the box magazine).
GTF60 brushless motors guarantee optimal functioning and high performance with a wide range of formats (3): containers and their covers (minimum 90x40x40 mm, maximum 300x300x150 mm), from pressed or canetté cardboard. The closures can be clasping or glued, including on three sides, and the operating speed reaches up to 60 cycles/minute. The cantilever design guarantees total accessibility on all sides and optimizes conductivity. The system boasts many other distintive features, starting with the use of chainless systems to reduce cleaning requirements and the time they require, as well as control of all cycle phases, from forming to feed, from filling to closure.
GTF60 can adopt various automatic feed systems - conveyor belt, drawers, stacking and more - with the products being loaded onto the trays by pushing or MG2’s own pick&place system, or with a robot. The positioning of the feed, in line or perpendicular to the die-cutter, guarantees extreme layout flexibility. It is also possible to equip the machine with multiple loading stations and a variety of other functional components: for inserting instructional manuals; box contents control; marking; barcode scanning; scrapping station.