Valves (and a lot more) for 3D printed respiratory masks
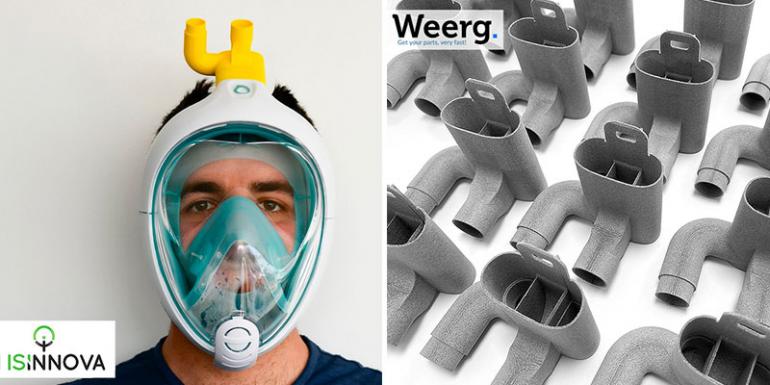
Matteo Rigamonti, founder of Weerg, tells how his e-commerce company decided to join the project launched by Isinnova and FabLab Brescia, to create emergency respiratory masks from snorkeling equipment.
This is a collaborative story. Between a former head physician of the Brescia hospital of Gardone Valtrompia (Renato Favero) who had the idea of readjusting a snorkeling mask model, Isinnova (a consultancy company operating in the industrial mechanical engineering sector), and Decathlon, manufacturer of the Easybreath mask. This had led to the design of the additional component to connect the mask and the respirator, the valve, called "Charlotte", has already been patented for free use so that all hospitals can avail themselves of it. With 3D printing, the first prototypes were made in record time, immediately tested in hospitals in the province of Brescia, direly affected by the emergency, where tests were carried out on patients in a state of great need.
Isinnova and FabLab (a digital manufacturing laboratory) have chosen to share the file free of charge with all the companies able to print the valves and, together with many other companies that have immediately taken action, including Weerg, specialized e-commerce in 3D printing which has a unique professional 3D printing department in Italy with the latest generation of industrial machines, that immediately responded the appeal.
«We made contact with Isinnova and in just one day, thanks to our HP Multi Jet Fusion 5210 printers, we were able to supply 500 valves made of PA12 Nylon, a material compatible with this sanitary application» explains Rigamonti. This first batch of valves will be assembled on the same number of masks and supplied to Brescia’s Civil Protection for distribution to hospitals.
A reminder that Weerg, thanks to its available technologies, has been able to produce parts of medical instruments that were necessary in these moments of emergency in record time, creating a single piece in 3D as well as a series of up to 5,000 pieces in thermoplastic materials (Nylon PA11 and Nylon PA12). Rigamonti's commitment is to put its production capacity at the service of hospitals and companies that operate on the front line. «We have 50 quintals of PA12 Nylon available which is why we are sending e-mails to healthcare companies to whom we will reserve symbolic prices, sufficient to cover our materials costs».