Augmented reality underpins the new normal
For Cama, the secondary packaging specialist with highly technological automated packaging systems for the food and non-food sectors, AR is today a standard solution that guarantees efficiency.
Augmented Reality (AR) is an increasingly widespread engineering solution that CAMA Group utilizes in numerous applications ranging from training and testing to the execution of FAT and SAT and the remote management of changeover.

«As a leading secondary packaging machine supplier to all of the major global vertical markets,” Massimo Monguzzi, R&D Manager at Cama Group explains, “it is a pre-requisite that we must exploit and deliver the very latest features that technology can provide. From our perspective, having a digitally capable platform already in place - in the form of our BTG range of machines - has made the transition for us and our customers a lot simpler. Like many companies, we have the in-depth CAD data that forms the foundation for our AR offering, but unlike some others, our exploitation of fully interconnected digitally capable hardware and software means that our AR solutions can be used for full simulation».
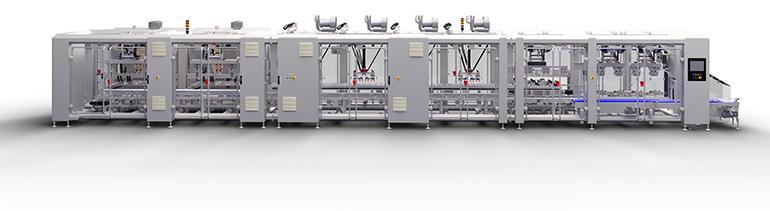
Training (and know-how) by remote.
«A case in point would be for a recent application we developed for a well-known household brand. We were able to deliver a virtual version of the customer’s precise machine thanks to highly detailed CAD data. Using this platform there were no surprises when the machine was delivered; the operators already knew it intimately from the AR/VR models.
From the outset, at the design and prototyping stage, customers can get a clearer appreciation of the machine and fully understand its capabilities. Operation can also be fine-tuned thanks to simulations based on accurate product models. At this stage, the machine can be virtually superimposed into its proposed location and then manipulated, so any utility and real-estate issues can be solved prior to install.
Faster changeover for a more efficient production.
«We are boxing up AR and other digitally enabled capabilities into what we call 4.0 Packages» Monguzzi adds. «Compared to the market average, we offer quicker changeovers than most, involving operators only for the strict necessary. Today we have managed to cut changeover in half - from 30 minutes to just 15. In coffee production, for example, where production speeds and outputs are so high, saving even 15 minutes per changeover is vital. If there are 10 production changes per day, which is not uncommon, this equates to 2.5 hours of additional up time. Payback for the additional technology is less than one month».
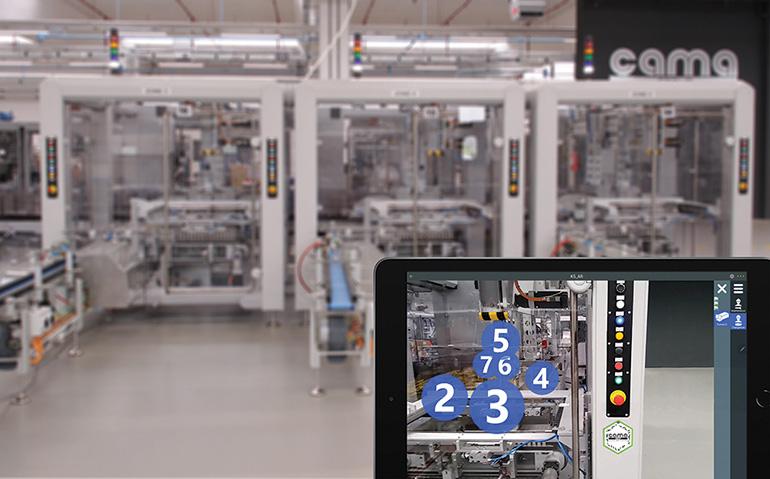
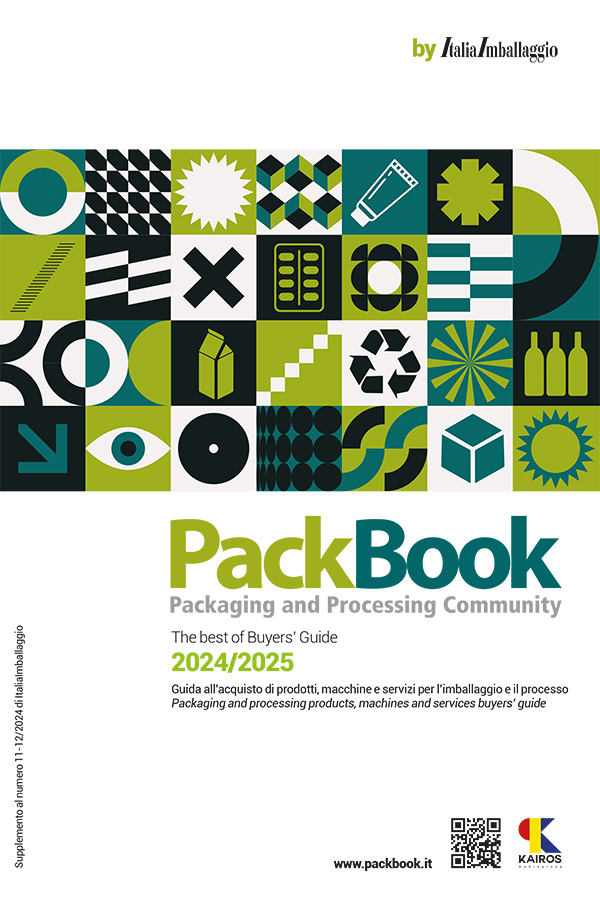