Additive Manufacturing in Italy
In strong expansion thanks to incentives, A.M. has come under the lens of SPS Italia, which has published the Observatory Additive Manufacturing - Knowledge, use and developments of additive technologies” in collaboration with the Milan Polytechnic/MADE, the Turin Polytechnic/+CIM 4.0, University of Pavia, Porsche Consulting. . Maurizio Cacciamani
Additive Manufacturing is a booming market in all industries, so much so that it is estimated it could exceed $27 billion in 2023. The real turning point will be when it becomes a widespread technology, replacing traditional techniques and generating new business models.
Memorandum: at the SPS fair in Parma there will be an area dedicated to Additive Manufacturing, which will animate the District 4.0 from 6 to 8 July 2021
A.M. is one of the Industry 4.0 technologies, to which Italian manufacturing industries are approaching, studying its advantages and problems.
One of the most interesting elements that emerged from the Observatory is that additive technologies are of interest not only to technicians, but also to entrepreneurs and top managers (25% of responses), managers (40%) who are concerned with strategy, sales and marketing, and risk management. A.M. is therefore not perceived only as a technological “upgrade”, but as an effective business opportunity.
Who answered the questionnaire? Mostly micro, small and medium enterprises (64%), while large or very large companies accounted for 36%. The most interested sector was that of Mechanics and Capital Goods, clearly thirsty for innovation also due to its strong international projection, followed at a great distance by Automotive, Pharmaceutical/Medical, Consumer Goods/Fashion, Packaging, Aeronautics/Space.
Technology and the market. « «The analysis of the results confirms the consolidated role of some technologies (extrusion and powder bed) and some classes of materials (polymers and metals) as the dominant ones at the moment, for prototyping and small series production,” so Bianca Maria Colosimo, Department of Mechanical Engineering Politecnico di Milano - MADE Competence Center I4.0,, who continues “The need to take advantage of additive technologies starting from a product re-design is also evident».
40% of respondents see material jetting (material droplet deposition) as the technology on which to focus future expectations because of its potential advantages (high resolution and productivity), but it currently has some limitations.
Where is A.M. used? In prototyping (39%), possibly combined with small series production and customized products (32%), areas in which additive technology is currently able to offer economically advantageous solutions. Extrusion (typically of polymers) and powder bed technologies (for polymers and metal materials) are used by 50% and 40% of respondents respectively.
Service bureaus (55 per cent) and universities/research centers (35 per cent) play an important role in the deployment of additive technologies as they enable end-users to assess their potential without large up-front investments.
Nearly 60 per cent of respondents see functional prototyping, pre-series and small batch production as the main benefits of additive technologies, with technology suppliers confirming this view. Powder bed (60 per cent) and extrusion (45 per cent) technologies are popular for printing polymer (75 per cent), metal (more than 60 per cent) and composite materials (45 per cent).
Approach to technologies
Giovanni Notarnicola, Associate Partner Porsche Consulting, highlighted how the Observatory shows a strong medium-term potential of this technology, sometimes held back by the lack of in-house skills (56%) and the high perceived investments for implementation (20%). Effective dissemination of knowledge and adequate use of European and government incentives could overcome these obstacles.
The drive for innovation and the desire to overcome production constraints have convinced those who have already successfully experimented with A.M. that, in 80% of cases, have met and exceeded expectations. The potential value of this technology impacts several phases of the value chain, from research and development to after-sales, passing through production.
Other interesting data: among the 60% of users who participated in the Observatory, 31% did so with internal staff; of the remaining 40% (who have not yet used them), most see a probable use in the medium term.
The desire to explore an emerging technology, the perceived impact on R&D times, together with the desire to overcome constraints in design and production, are the main reasons that have led companies to experiment with this technology, which offers high flexibility.
Skills
«One of the obstacles to the diffusion of A.M.», explains Luca Iuliano, Director of the Interdepartmental Center for Integrated Additive Manufacturing (IAM@PoliTo) at the Politecnico di Torino and President of the CIM 4.0,Competence Center «concerns the lack of skills and professionals with specific training on technologies, materials and processes».
The integration of A.M. technologies in production processes requires multidisciplinary skills, from advanced design solutions, to techniques of treatment and characterization of materials up to quality control solutions, monitoring and process simulation.
Important, therefore, is the need to invest in on-the-job training (41.1% of responses) to train personnel in dedicated laboratories, with the support and advice of the academic world and research. The main skills lacking in companies are, in order: in-depth knowledge of processes (74.4%), those on “design for A.M.” (73.3%) and on methodologies. (73.3%) and post-processing and finishing methodologies (47.8%). Talking about services aimed at encouraging the adoption of A.M. in companies, the one considered most strategic is on-the-job training for personnel in dedicated laboratories, followed by consultancy for the technology to be adopted and consultancy on design & engineering for A.M.
All the advantages of A.M.
The challenge for companies is to be able to look ahead by imagining the possible evolutionary scenarios of their sector, starting at the same time an experimental, modular and sustainable path. The winner will be the one who, thanks to a strategic approach, will transform Additive Manufacturing into a lever of competitive advantage.
A.M., a mature technology, is not a panacea for all ills, therefore it cannot solve all applications, however it offers several advantages:
- Industry 4.0 technology
- Reduced design time
- Design freedom
- Reduced development time and time to market
- Reduced material usage (use only what you need)
- Reduction of waste
- Simplify end-of-life activities (disposal)
- Extended product life (easier repairs)
- Reduction in the number of components thanks to the possibility of creating complex shapes with reduced assembly times
- Production of ad hoc spare parts (even unique pieces) with a consequent drastic reduction of the spare parts warehouse
- Distribution of the production on machines located geographically in different places with reduction of transport costs.
Return on investment and strategic prospects
According to Ferdinando Auricchio, Construction Science, Department of Civil Engineering and Architecture, University of Pavia, «A.M. is a technology that is sufficiently widespread and appreciated for its ability to provide an important added value: the reduction of design and production times (73.2%)».
However, there is a limited perception of the need to redesign and optimize in order to increase competitiveness by taking advantage of new design/production methods. A far from negligible percentage of users have a clear vision of the impact of costs (63.4%), but for an important slice of potential users it is still unclear what the costs are and the added value offered (36.6%).
A.M. is seen by 48.3% as a technology with a short-term return (<2 years) and has the potential to greatly influence the development of more innovative products and, therefore, with a long-term return.
To conclude, a forecast of where A.M. will be used in the next few years: in addition to the sectors of major use mentioned above, the percentages obtained by the pharmaceutical/medical 36.7%, packaging 8.9% and food 3.3% sectors should be underlined..
The Observatory pdf can be downloaded at this link
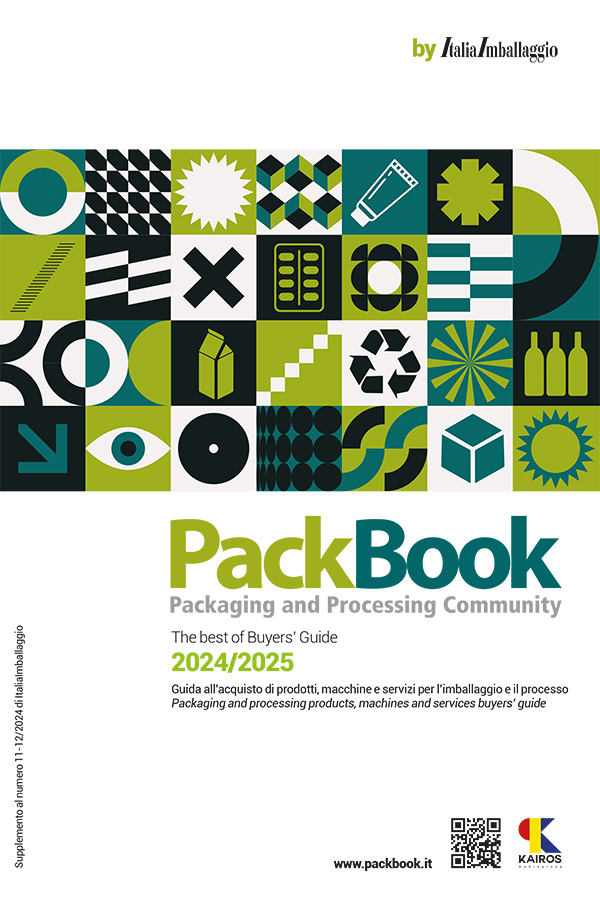