Flexible packaging and secondary packaging options for the food industry
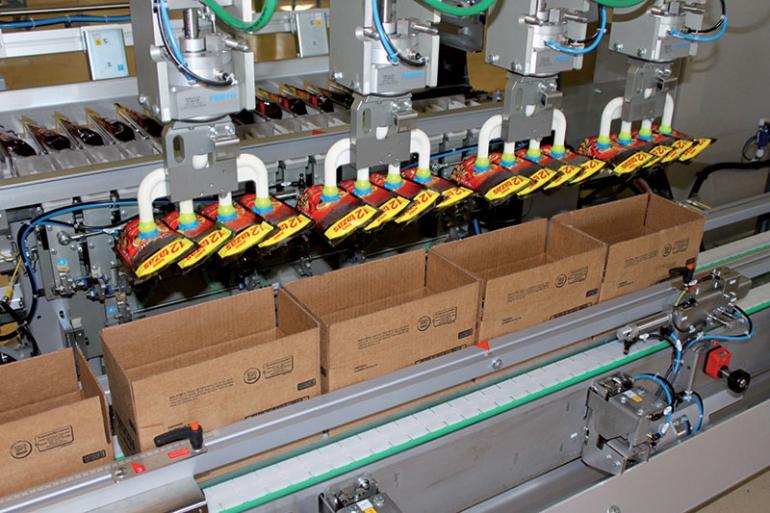
Advantageous in terms of marketing, profitability and logistics, flexible packaging poses non-trivial problems in automated end-of-line management. Sidel tackles them with technological solutions designed for the food sector, which draw on the experience acquired with this type of packaging and consolidated know-how in terms of robotics.
As well as being a global leader in the beverage industry, Sidel has also been a reference partner for over 50 years for companies in the detergent and food sectors. For the latter, in particular, Sidel offers customised solutions and services for food and secondary packaging, focusing on the handling of products packaged in flexible packaging.
In this field, Sidel’s offer is mainly focused on carton packaging systems, palletising and line integration, all characterised by extreme flexibility, ease of maintenance and efficiency.
This is discussed extensively by Etienne Henry (Sidel’s Packaging Business Development Director).
Why is secondary packaging such an important factor to master projects for the automation of flexible packaging?
Because it provides essential protection and stability to compensate for the unstable geometry and obvious lack of resistance or rigidity of flexible packaging.
Depending on varying producers’ wishes and logistical constraints, such as “easy opening” boxes, products standing up or lying flat in the case, the level of protection needed or the optimisation of the case filling in terms of surface area and cost, Sidel offers several configurations and solutions. Via our portfolio, we enable our customers to handle many different alternatives, such as RSC cases, Wrap-Around blanks and Shelf-Ready Packaging. It is key to keep in mind that there is no “one-size-fits all” solution. You will make a real difference when handling flexible packaging, thus improving product integrity, packaging quality and line performance, if you choose the right solution among the wide range of product infeed and packing systems. All of this, while considering the factory’s configuration and challenges. This is where Sidel can step in, helping customers obtain the best match between primary and secondary packaging solutions, together with the most suitable mechanisation technology.
What value are you as an equipment supplier bringing to this market?
The mechanisation process of flexible packaging can easily present issues when it comes to product handling and packing. This is due to the lightness and deformability of this kind of primary packaging. Its so-called unstable geometry has five major consequences: no accumulation possible, no counter-pressure to seal secondary packaging, no or little resistance to vertical compression of the secondary packaging on the pallet, limited protection of the product inside and risk of causing case crashes and, thus, pallet instability.
Sidel is able to provide several appropriate solutions for primary packaging, starting with traditional side-loading packers up to more sophisticated systems, enabled by our long-term expertise in robotics. Robotic packing represents the perfect alternative when the process requires a significant flexibility to handle high packing speeds and high number of SKU’s. For other needs, a simpler type of manipulator (for factories with lower speeds and more standard packing configuration) is more recommendable.
What key areas of expertise allow you to set up automatic packaging solutions for flexible packaging that ensure maximum efficiency and the best return on investment?
Firstly, we are familiar with the constraints inherent to primary packaging, in particular during conveying and handling. Secondly, our company has more than 50 years of experience in secondary packaging. Last but not least, we come with an important legacy in mechanisation and automation, which allows us to always design and deliver solutions which are tailored to the specific needs of our customers.
In a “white paper”, successful case histories
The different experiences gained in the context of the numerous Sidel projects are widely covered in a white paper we have recently compiled, addressing the current state-of-the-art options and solutions with regard to flexible packaging and secondary packaging options for the food industry:
- Cermex WB46, a twin lane infeed Wrap-Around packer with a robotic arm, installed for the Indonesian manufacturer Frisian Flag. The challenge was to find the right solution for folding the chain bags, placing them into flow packs and then positioning these flow packs in Wrap-Around cases. All of this while keeping the batches firmly grouped throughout the whole process. The fully automated solution provided by Sidel was able to eliminate all the operations that were previously performed manually, while ensuring a stable, optimal packing and secure case filling.
- A system for the packing of liquid refill pouches standing up into RSC cases.
- A solution to pack pouches in a creative way, with spout lying flat in the case, yet optimising the case filling and/or reducing its size.
- A system for the packing stand-up pouches of coffee in an upright position, leading to a shelf-ready packaging for the retailer.
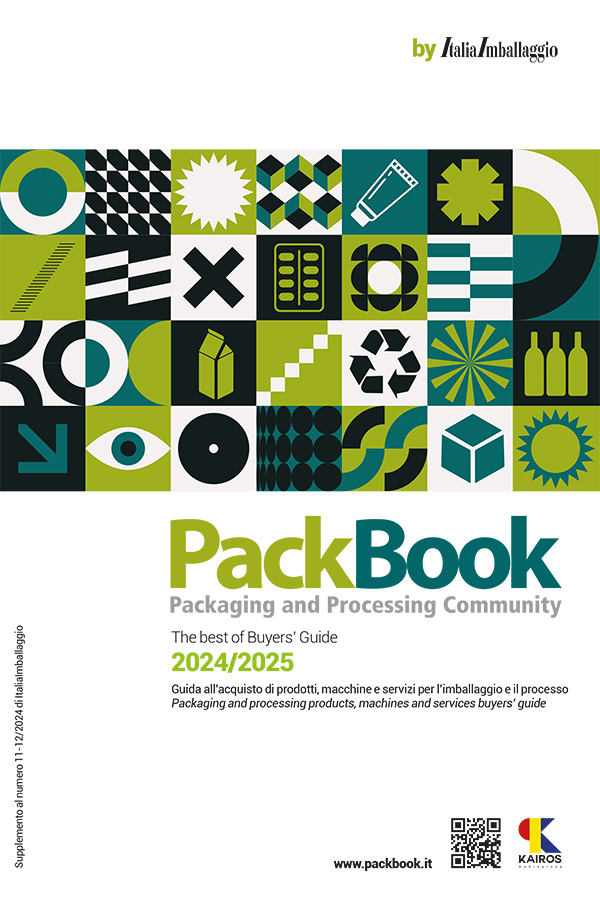