Spare parts warehouse: how to reduce the cost aspects
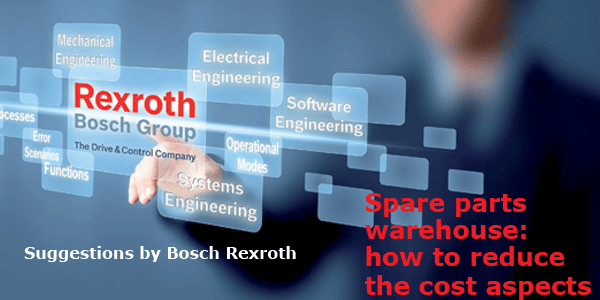
THE EXPERT REPLIES Processing automation, energy, timed cams, open and modular automation architecture, soft automation, service: in the column on ItaliaImballaggio called “The expert replies”, Luca Stanzani (Packaging and Processing Bosch Rexroth Italia) will provide answers for the specific problems that the readers will tell them about. Write to [email protected]
Question
Hello. Rather than a question, what I'd like to highlight is a particular need common to most end users. Our production lines are made up of systems and machines produced by different suppliers, often using different products and systems. To avoid machine down-time, we have to keep huge spare parts warehouses and this has a devastating effect on costs. Is there a solution? R.R.
Unfortunately, there's no single answer that can fully resolve this problem.
The point is to try and reduce warehouse codes and frozen capital, avoiding any obsolescence.
But how? Here are a few simple ideas:
• establish an active, open relationship with suppliers of both machines and components
• request a list of recommended spare parts from the manufacturers
• keep an updated product “phase out” list to avoid, foresee and manage any situations of obsolescence
• ask the system suppliers to standardise the components as much as possible; in fact with the minimum effort, it's often possible to reduce the number of codes by 30-40% (the most frequent examples are the size and options of motors, reducers, pneumatic actuators, linear actuators, etc.). On this subject, I'd like to give you a concrete example that recently came up. Bosch Rexroth managed to acquire an important new customer thanks to its range of linear guides that guarantee the same loads on all 4 sides, and the same tolerance class even with separately purchased components (therefore not bound to the guide/runner block supply); this means greater component standardisation and a 40% reduction in codes.
• use flexible products (for instance, the Rexroth IndraDrive range offers a single hardware that can work as both inverter and servo, with or without retro-activity)
• when possible, propose the use of international standards (customisation should be avoided) and interchangeability of components (e.g. guides, runner blocks, ISO pneumatic cylinders, I/O modules, asynchronous motors)
• request the use of products and systems that can be used with different systems and protocols
With regards the last point, please note the two important innovations introduced by Bosch Rexroth in its range of inverters and servo drives, that have the added aim of standardising hardware and firmware and thereby reducing the number of codes.
In particular, the introduction and use of: multi encoder inputs - a single encoder acquisition interface and therefore a single code, so the encoders (motor and/or external) can be managed with the most commonly used protocols (Hiperface®, EnDat 2.1, EnDat 2.2,1 Vpp, 5 V TTL, Resolver) and a multi-protocol communication interface - a single support (hardware and firmware) and therefore a single code for four different communication standards based on the Ethernet protocol (SERCOS III, PROFINET IO (RT), EtherNet/IP, EtherCAT).
Both these innovations fully respond to the need to reduce warehouse codes; in fact a single hardware, that can dialogue with 4 different communication protocols and read 6 different types of encoder, can potentially reduce the number of codes by 95% (passing from 24 codes to one single model!).
Finally, here are some hints for end users, based on our experience over the years in relation to consultancy and after-sales services applied in various production sites.
It's essential to know what products are installed in your systems. By simply mapping the installation components (an operation that only needs to be carried out once), you can obtain a complete, clear picture of the products and systems installed (or at least the most strategic and sensitive ones). Combining this information with the warehouse stock, you can immediately see if any fundamental spare parts are absent, or if there are any situations of obsolescence or over-stocking (situations that are far more common than you may think).
Last but not least, keep a record of breakages, repairs and replacements as this is an excellent way of monitoring (via log records and statistics too) any problematic issues requiring further attention.
For further information www.boschrexroth.it