F&B multinationals invest in Italy
Safety, ecology and quality of working environments come together in an evolved concept of sustainability, the subject of multi-million dollar investments in our country.
By M. Costanza Candi
They are global multinationals, firmly rooted in the local area and with great potential for innovation. They are called Ferrero, Unilever, Campari and they look at our country as a fertile economic and entrepreneurial world, where know-how and development potential deserve major investments. They interpret 'sustainability' from different points of view, but with a common element: ‘people at the centre'.
We are talking about three recent interventions by:
- Ferrero, which has opened an innovative production plant in Alba where the concept of sustainability embraces both the environment and the workers;
- Unilever, which is aiming at the south of Italy with a new zero-emission production site and where the training of young people is at the forefront;
- Campari, which has built a global path of safety for workers with their active involvement.
The ideal factory exists and overlooks the Langhe region
The new Ferrero technical innovation centre is located in Alba, the Group's headquarters, and represents a model of integration between industrial architecture, natural landscape, process sustainability and workers' well-being.

The project by Frigerio Design Group is designed to respond to the principles of manufacturing 4.0, where human-machine interaction is brought into relation with its ecosystem, on a productive and non-productive level. The resulting Technical Centre brings together the engineering activities dedicated to the design of new production systems and the workshop, where these systems are pre-assembled and tested.
The development project, covering 12,700 square metres and housing more than 200 employees, follows the philosophy of slow architecture, marked by a reduced ecological footprint, giving rise to a building constructed in the natural surroundings of the Langhe region, designed to guarantee safety and sensory comfort.
The building, which is bioclimatic and nZEB (nearly Zero Energy Building), is designed to minimise carbon dioxide emissions, while the compact volume, made of industrial materials, maximises all passive inputs (light, air and sunlight), limiting management and maintenance resources to a minimum. A photovoltaic system on the roof guarantees a peak energy production of 300 kW. Thanks to the doors placed opposite each other, the rooms can also be naturally ventilated, while the offices are air-conditioned with radiant ceiling systems that operate at 40° instead of the usual 70°, and also perform a sound-absorbing function for acoustic room control. The outdoor car parks also ensure the control of light pollution, thanks to a smart system that regulates the lighting only when there is traffic.
Zero-emission ice cream is made in the South
Unilever's Caivano site, the multinational company's ice cream hub, is the main player in a major 60 million euro investment, which will finance the new plant and logistics hub. A zero-emission factory, digitised and designed to accommodate younger workers, towards which an integrated training strategy is planned between Unilever, the local ITS (Technical Institutes) and the Federico II University. The proposal, which is included in the ‘Piano Italia' of the global F&B giant, envisages an investment of 40 million in the factory and 20 million in the logistics centre and the warehouse, both united by a common goal to be achieved by 2026: reducing the factory's CO2 emissions to zero, applying a circular economy strategy to reduce waste, implementing a digitalisation process and regaining competitiveness. The idea of sustainability introduced by Unilever, however, does not only concern the environment, but also involves the workforce, with a number of employees that remains stable over time, but with a greater number of engineers on the technical side and, in general, an overall lowering of the average age, with about one hundred young people entering the company within five years, who have been trained in the local Technical High Schools and academic structures.

Safety at work is a global issue
Campari Group has recently revised its safety programmes with the support of Omron Safety Services. With the aim of improving machinery and process safety management to global governance, the multinational spirit market company has pushed for a radical overhaul of health and safety aspects in the workplace, going beyond procedural aspects to consolidate a new cultural paradigm throughout the Group's companies. The approach taken by Campari, as interpreted by Omron, is pragmatic, and actively involves operators who have helped define the standards necessary for efficient, safe but agile work.
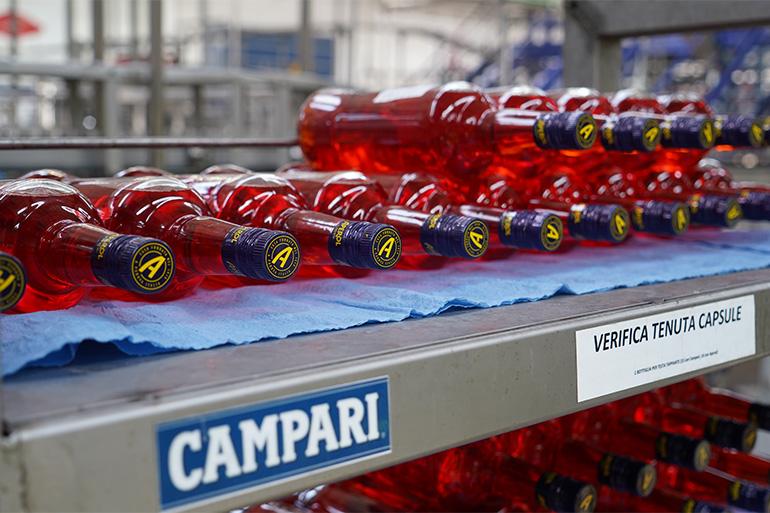
Omron has applied the expertise of Safety Services in combining technical and skills development, ensuring the uniform distribution of the new instances to all of the company's plants on three continents. In fact, the cultural revolution, as Campari calls it, is a global one that was first implemented in the Novi Ligure plant and then borrowed by the other sites, drawing up and following a real Campari Group Handbook, which represents the synthesis of all aspects of the common and shared safety model. Plants and workers now operate according to the same safety criteria, not only with regard to compliance with local regulations but also in terms of a common way of working in production, wherever they are. As a technology provider, Omron's programme focused on the most common classes of activity within the Group (palletising, depalletising, filling, labelling) with a particular emphasis on engineering, analysing the status quo regardless of the type of technology installed on board the machine or plant.
In addition to automation, evaluations focused on the right balance between efficiency and safety in order to avoid overly complex procedures. This result was obtained with the active involvement of the operators, with whom a shared approach was built to maintain the required safety standards but without burdening production.
The story can be found online at: https://youtu.be/AOr8PIBzH-k