Better handling of smaller products
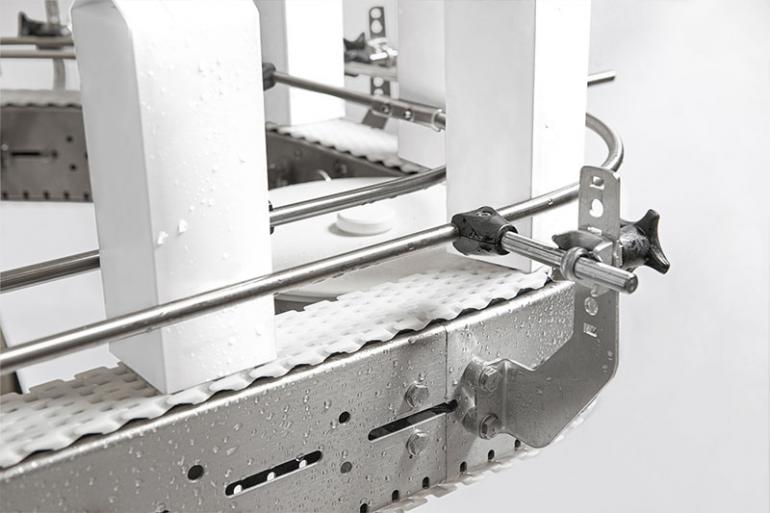
FlexLink expands its range of stainless conveyor widths and product handling functions designed for dairy, food, personal care, and pharmaceutical production.
Following 40 years' experience in automation, FlexLink introduces further capabilities for smoother product handling. In addition to the 85 mm, 180 mm, and 300 mm stainless steel sizes available, FlexLink now offers a new 70 mm option. This new size will replace the present XLX option.
Designed to handle smaller food containers and packets that are more sensitive to being unstable during production, this additional offer gives manufacturers greater possibilities to optimize their production control during manufacturing.
A toolbox for clean and safe production. FlexLink's comprehensive toolbox of solutions efficiently handles more product sizes and types than before. Standard handling functions available include cleaning solutions, clamp stops, and transfer bridges.
Operator safety is key. The importance of operator safety continues to be a driving force for product development at FlexLink. In line with the additional 70 mm conveyor option, FlexLink has also introduced a new chain design, available for the stainless steel, as well as the aluminum product range.
The innovative chain design has a high focus on product and operator safety, decreasing the opportunity for operator injury during production. The new design is approved by and compliant with both the latest European and American regulations.
Thanks to a reduction of pinch points, manufacturers are less likely to experience production losses caused by unstable products. The possibility for products such as juice cartons and baby food pouches to be damaged is also lessened, as a result of fewer pinch points.
A focus on simplicity. When considering line design, the simplicity of a lean interior reduces the time needed to clean the line and minimizes the risk of cross-contamination. Without crevices for contaminants such as crumbs to fall into, and with easy operator access for cleaning, the line starts with high levels of cleanliness that are easier to maintain.
Transporting products from primary packaging through to the end of the line, FlexLink provides a clean, simple line layout, following HACCP guidelines. With the combination of a more comprehensive portfolio of stainless steel conveyors and improved safety features, FlexLink continues to give value and control to manufacturers.
FLEXLINK AB (GÖTEBORG, Svezia) is a leading factory automation expert and provider of conveyor systems, material handling functions and delivers turnkey solutions including controls and standardized robotics: innovative, solutions to produce goods smarter and safer at a lower operating cost. Its main customer industries are the automotive, electronics, healthcare and fast-moving consumer goods industries.
Its aim is clear: adding value to every step of the process, whether it concerns design, installation of new lines or optimization of existing ones.
FlexLink is part of Coesia Group, a group of innovation-based industrial and packaging solutions companies operating globally, headquartered in Bologna (Italy), fully owned by Isabella Seràgnoli. The 21 Coesia companies are leaders in the sectors of advanced automated machinery and packaging materials, industrial process solutions and precision gears.