Italian Excellence for the German Beverage Industry
A latest-generation palletising system, designed for the beverage industry, is supplied to a German customer: Gampack Group’s expertise overcomes barriers and guarantees success.

In the era of advanced industrial production, customized palletising systems represent the cutting edge of technological innovation, optimizing the efficiency and precision of production lines.
Whether relating to increasing production capacity, improving logistics management or ensuring rigorous quality standards, these systems are the key to obtaining a competitive advantage in the global market.
This is where the Gampack Group comes into play. With established experience in the development of palletising systems, it has made a significant leap in quality thanks to the combination of mechatronic and robotic technologies. This approach has allowed the company to develop ever more sophisticated and precise solutions to meet the diverse needs of customers.
An example of this innovation is the palletising cell designed for a German customer in the beverage industry, able to manage production lines of two different beverage cartons at the same time, thereby significantly increasing productivity.
How the palletising cell works. The first production line handles 500 ml items, packed in 12-piece transport cases at a rate of 13 cases per minute. The second line produces 1000 ml beverage cartons, packed in 6-unit cases with a nominal speed of 26 cases per minute. The 500 ml line pallets are composed of 6 layers, while those for the 1000 ml line have 5 layers.
The system is flexible and allows the customer to choose the number of layers for each pallet on a daily basis. The core of the system is a 4-axis anthropomorphic robot with a load capacity of up to 450 kg, which is able to manage the gripping of entire layers, interlayers and empty pallets with the same head, guaranteeing the precise and safe handling of the materials.
Each production line feeds an independent preparation layer top, maintaining a constant flow during the simultaneous production of the two lines.
The empty pallets are fed in stacks inside a pallet magazine, complete with the relevant pallet dispenser, to move on roller conveyors up to the quality control device. Every pallet is subject to rigorous conformity controls, thanks to as many as eight different types of dimensional and integrity checks (e.g., length, width, thickness and resistance). Non-compliant pallets are ejected and stacked in a dedicated system, while compliant ones are transferred to the picking position.
Once completed, the pallets are sent to a wrapping system with stretch film, equipped with a top-mounting device to avoid dust accumulation during prolonged storage. Finally, the pallets are labelled on three sides. A sophisticated communication system with the customer’s MES system sends production data for internal statistics and label printing. The ability to adapt rapidly to production variations and the rigorous quality controls ensure products meeting the high standards of this industry
This innovative palletising cell successfully reaffirms Gampack Group’s technological excellence and operating flexibility in a market as demanding as the German one.

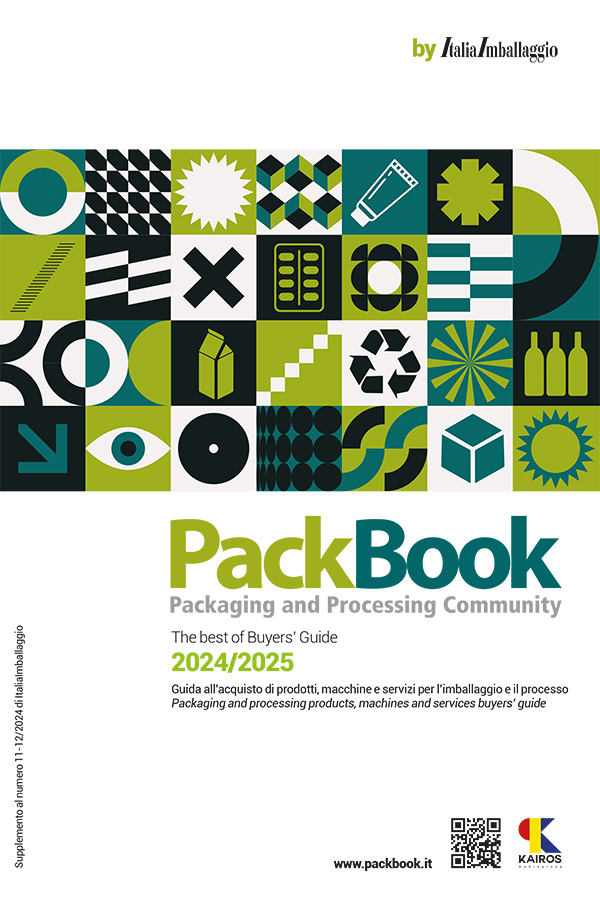