An EDGE + CLOUD solution for the analysis of production processes
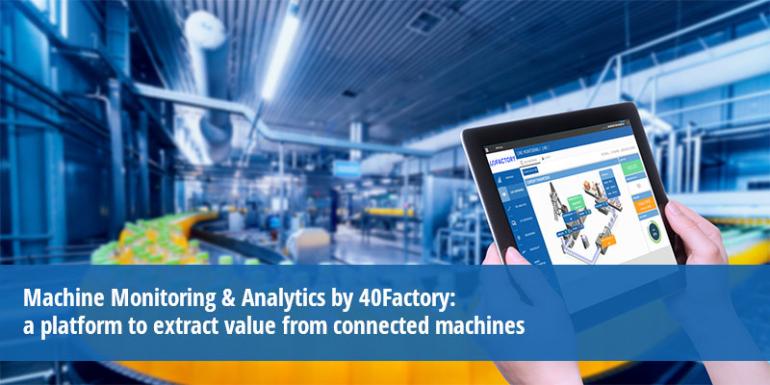
Efficiency analysis, monitoring and predictive maintenance of packaging, wrapping and filling lines are issues at the center of the digital transformation process of the main industrial sectors: from food and beverage to pharmaceuticals, going by way of cosmetics.
Machine Monitoring & Analytics of 40Factory - leading Italian company in the development of IIoT and Data Analytics solutions - is a platform for the analysis of production lines connected, based on three basic elements:
- Edge computing, for the extraction of data from the production machines and their preprocessing within the perimeter of the plant through intelligent industrial PCs installed on the line.
- Cloud computing, for archiving, analyzing big data and accessing information in ubiquity in compliance with the main security standards.
- Data analytics and AI, to transform raw data into added value.
Machine Monitoring & Analytics is made up of smart modules, which can be composed as desired and customized, based on customer needs and the specific production context: the end result is a streamlined solution that is immediately ready to generate value from the data extracted from the system, which relies on market cloud platforms, such as Siemens MindSphere, capable of meeting all the standards required by the industrial sector, such as data security and privacy.
Edge Plug & Play connection. The connection of the machines takes place in a plug-and-play way, through intelligent Industrial PC (IPC), able to acquire data from the main automation systems with standard protocols, such as OPC-UA and S7. Variable mapping can be custom or use a standard profile, such as OMAC PACKML. Multiple IPCs can be used in a modular way, to connect various production lines, without necessarily requiring modification of the automation software. Not only machines, through the EDGE level it is possible to acquire data from factory IT systems, such as MES, ERP or database.
Cloud Machine Supervision. Once the connection is complete, it is possible to access production data and the main KPIs in real-time such as, for example, recipe parameters, process variables, line speed, real-time OEE and others. The monitoring of the lines can take place from anywhere in the world, even from mobile devices, thanks to an adaptive and progressive HTML5 WEB interface.
Production Data Analytics. Machine Monitoring & Analytics modules include functions for the analysis of the OEE of the plant and of the individual machines, analysis of the causes of downtime with Pareto diagram, analysis of customized KPIs and their comparison by aggregation factor. You can answer questions such as: "What is the production format that has experienced the lowest quality rate in the past 90 days?" or again, "what is the shift of the day in which the most plant shutdowns occurred in the current month?" All this information is accessible in an intuitive way and through dashboards with a high graphic impact.
Traceability & energy consumption. Machine Monitoring & Analytics offers an advanced module for process traceability, necessary in sectors such as pharma and food & beverage. For example, it is possible to correlate trends of process variables, such as pressure levels and temperatures, to production events, such as machine stoppages, format changes, maintenance and others, in order to identify hidden patterns and possible correlations.
Furthermore, through the energy monitoring module it is possible to track energy consumption (electricity, air, nitrogen, etc.) and run them to production volumes. The system, through deep learning algorithms, is able to alert the user in case of abnormal consumption compared to the normal trend.
AI & predictive maintenance. Starting from the acquired data, it is possible to synthesize a digital model of the line or part of it: the data driven digital twin is the digital model of the physical line, created using artificial intelligence models, based on deep learning and machine learning.
This tool allows you to enable predictive maintenance logics on the connected line; it provides, in real-time, indications on the health of critical components, such as an end-of-line palletizer or a dosage unit, and is able to identify and classify any anomalous behavior.