How (and why) to digitize food&beverage
Evolution of processes, the critical points to which companies must pay more attention, success stories... without forgetting cybersecurity, of course.
Maurizio Cacciamani
Coordinated by Matteo Faggin General Manager of Smact Competence Center Triveneto, which operates not only in the manufacturing sector but also in agrifood, the round table organized by SPS Italia in April offered a wide range of opinions on the opportunities offered to the agrifood industry by digital transformation, which we summarize below.
«Those who do not digitize are at risk and digitization is an essential element of business,» recalled Fabio Massimo Marchetti, Vice President ANIE Automazione - President WG Software Industriale, at the opening of the works, citing the advantages that the food sector can draw from it: better planning, greater flexibility of plants, improved efficiency thanks to the simplified evaluation of performance (waste and energy consumption). Marchetti concluded by underlining the importance of software as a key enabler for digitalization.
Supply chain control. Lorenzo Mastrangelo (R&D Manager ICAM - specialized in the design and implementation of automatic systems for the warehouse) underlined how digitalization allows «a complete control of the supply chain with improvement of flows, optimization of stocks and supplies, management of the perishability of products (fundamental for the food sector) and also of their conservation, thanks to the automatic control of temperature and humidity». In conclusion, digitalization makes it possible to get closer to the consumer by eliminating unnecessary steps.
Have clear objectives. For Daniele Ferrari, OT Manager Engineering Dept. at Parmalat, digitization is also essential, even though «its massive use can risk making a company lose sight of its objectives. Technology has grown exponentially and, unfortunately, so have the costs and skills needed to make the system work. We therefore need to be pragmatic: this is why, for example, at Parmalat, we have given up on projects relating to the digital twin, as they are not a priority at the moment. Instead, we are concentrating on the traceability and retraceability of milk with the company’s MES, reaching the shelves of the large-scale retail trade. We will have to integrate the upstream part of Parmalat, that is the stables of our suppliers».
New services for customers. «It is necessary to link technologies to customers’ needs, also offering them new services that guarantee food quality. The technologies are there to do this, but there are still no regulations similar to those of the pharmaceutical industry, from which to take inspiration to ensure greater transparency on product data». This is the opinion of Giancarlo Carlucci, EcoStruxure Plant Marketing Manager Schneider Electric, who believes that the many small and medium-sized companies in the sector should be helped to develop internal projects in order to successfully follow the path of digitalization.
The difficulties. Giorgio Santandrea, Head of Food & Beverage Vertical Market at Digital Industrie Siemens, described the situation of companies in the sector as varied: “Some are behind, others are very far ahead: however, they all need to produce a lot and well... an indispensable condition for staying on the market”. The biggest difficulties are related to data storage, networking structure, and the use of different software and networks.
More profits and more quality. Mark Olding emphasized that digitization is an accelerator for increasing profitability and product quality. «The problem is not the technology but the mindset of the people. Everyone in the company needs to start ‘playing’ with data to better compete in the marketplace».
The risks around the corner
The risks around the corner. Faggin introduced the thorny subject of the risks of (lack of) digitalization in the agro-food sector. As Olding said, “The risk is great and it’s failure”. And if Giancarlo Carlucci mentioned the difficulties of choosing the right partners in the digitalization process, Fabio Massimo Marchetti pointed out that one of the dangers is “confusing technology with strategy and not evaluating the digitalization phenomenon in its entirety”.
Giorgio Santandrea emphasized the search for funding, which is not grasped by the sector in its importance (this is also more serious due to the fact that the investment capacities of food companies are reduced). «Another obstacle is the very structure of the companies where you have to intervene: you almost always have to operate on existing plants, which must continue to produce».
As a user, Daniele Ferrari remarked that «it is necessary to proceed first where real advantages can be obtained: easy to say, much less to do. Skills play a fundamental role: Parmalat had great technological skills but few Data Analysis skills, which have gradually improved over time».
Lorenzo Mastrangelo also pointed his finger at the return on investment, but «it is not necessary to embark on the Industry 4.0 path because financing is available, but rather because there is a need within the company to optimize flows and costs. In addition to designing warehouses, for example, we offer a consulting service to the customer by providing clear numerical indicators on efficiency, handling times, stocks in order to analyze the return on investment».
Cybersecurity: we never talk about it enough
«Every day we try to make the market understand how important digitization is in order to remain competitive, but cybersecurity is just as important» says Andrea Scattina, Channel & Sales Manager Italy of Stormshield Italia, an Airbus Group company, who continues: «Every day we recommend the activities that need to be done to secure digitization. The questions to ask are: how do I collect the data? Where is the data stored? Does my data meet European standards? Is the data kept up to date? Who keeps the data up to date?»
Unfortunately, cyberecurity can’t be talked about enough, and it’s also evidenced by the fact that, in 2020, at least 30 well-known companies were hit hard by hackers. Not only cloud but also edge computing needs to be properly protected!
It should also be taken into account that, from July 2020 with the fall of the Privacy Shield, the data of European companies are no longer protected against US edge computing and cloud providers. Add to this the fact that the EU has published a list of states that are not “safe” because they do not comply with European privacy laws.
Here’s another question to ask: in which nation is my data stored? Is it a nation that is compliant with European regulations?
«From the point of view of Cybersecurity a food&beverage industry is not so different from an aeronautical industry». Scattina explains: «Obviously the dimensions change, but thanks to modularity, our solutions, which include hw&sw products and services, can be applied practically everywhere, not only in Airbus but also in the small company of 20 people. You have to protect the perimeters, the cloud(s), the plants by militarily separating OT from IT. Above all, we must be aware that there is no such thing as 100% security, so we must always keep up to date in order to fend off possible attacks that sooner or later will arrive».
Digital Transformation from Theory to Practice
The SPS round table dedicated ample space to the practical achievements already implemented by food & beverage operators. The problems solved and the advantages gained, sector by sector.
Milk... Parmalat has replaced 23 lines of traditional palletizers in the Collecchio warehouse with 7 lines of anthropomorphic robots that process 2 million liters of milk every day. In this regard, Daniele Ferrari gave some numbers: «Productivity has increased by 30% against an investment of euro 7,000,000, the expected return was 4 years, but in practice it has been about 3! The advantages obtained were not so much related to the production sector as to logistics».
Cheeses... Two cases were cited by Lorenzo Mastrangelo (ICAM): the first related to Tecnoblend (specialized producer of ingredients for ice-cream and pastry shops) which, with the introduction of the automatic warehouse, has improved the flow of raw materials. The second relates to the cheese producer La Deliziosa, which is experiencing vertiginous growth on foreign markets. «We have realized a spare parts warehouse relative to the production lines in order to give continuity to the production reducing drastically the machine stops».
Baked goods... A 12% increase in productivity, the possibility of managing two orders on the same line at the same time (one at the completion stage, the other at the beginning), predictive maintenance, almost total elimination of production errors: these are the results obtained by a cookie manufacturer thanks to the interconnection of machines, data management, digital modeling of the operation of the rather complex and very fast line. Fabio Massimo Marchetti (ANIE) brought the interesting example of a new plant for the production of bakery products, where the management of recipes, doughs, weighing and dosing, and quality control allows to make products according to requests. The implementation of artificial intelligence in data analysis allows to avoid future problems by avoiding waste.
Wine… Giancarlo Carlucci (Schneider Electric) talked about the application made in Fratelli Gancia, a wine house founded around 1850, «where tradition and innovation come together and where internal processes are very cadenced. We started in 2017 on the wave of energy saving, monitoring electricity consumption, then moving on to the interconnection of the lines, then we connected to the company’s information system: a digital transformation done step by step respecting budgets, with a well-planned ROI and doing progressive control tests».
Vegetables, chocolate and beer... «In Orogel - intervenes Giorgio Santandrea (Siemens) - the digitalization has invested the automatic warehouse where now, with a simulation software we have optimized the flows thanks to the analysis of the data related to the previous years. Another significant application concerns ICAM, the well-known chocolate factory. The liquid chocolate with different density is stored in silos and from there, through 50 km (!) of pipes, is sent to the processing lines. Due to the different density of the product, the pumps were subject to many failures, but where sensors have been placed, it is possible to control the status of each unit, minimizing mechanical risks and optimizing maintenance». Finally, Santandrea points to quality control in food and beverage companies where the process is difficult to predict, for example in the case of pasta drying or beer fermentation. In these cases, environmental data are collected (temperature, humidity, characteristics of the raw material) and thanks to artificial intelligence algorithms, the quality of the finished product can be predicted, making the necessary changes so as not to ruin production.
35 types of fruit to control ... «Digitization was a must for Unitec», says Piero Pasini, HR Department Development of the company specialized in automatic plants for the selection of fruit and vegetables sold worldwide.
«Our plants are able to check 35 different types of fruit and select them according to type, size, internal and external defects, crunchiness, sugar content as well as ripeness. We have embraced digitization because we are obliged to respond to the needs of customers who want more performance. So the use of vision systems made it possible to check cherries and blueberries in the round, compare the images with those in the database, and decide which class to sort the fruit into.
With the entry of artificial intelligence we now have algorithms such that the machine tunes itself according to the situation. Another advantage is predictive maintenance: from our locations we can monitor our customers’ plants wherever they are to ensure no downtime. This is important since, for example, the cherry season lasts only 40 days and the plants for their selection work 24 hours a day, seven days a week».
Not only food... Mark Olding (Exor International) wanted to remind us how digitalization concerns not only the realization of products but also the planning of production: «I like to remember that before digitalization, the scheduling of weekly production required our plant manager to work almost always on Sunday.
Thanks to the cloud where we have uploaded the MES ERP, production capacity data, sales data up to 9 months and human resources data, my colleague can plan production much faster and easier. From 3-4 months the system then, thanks to AI, is able to predict any problems and suggest solutions. Now our plant manager can devote his Sunday completely to his family!».
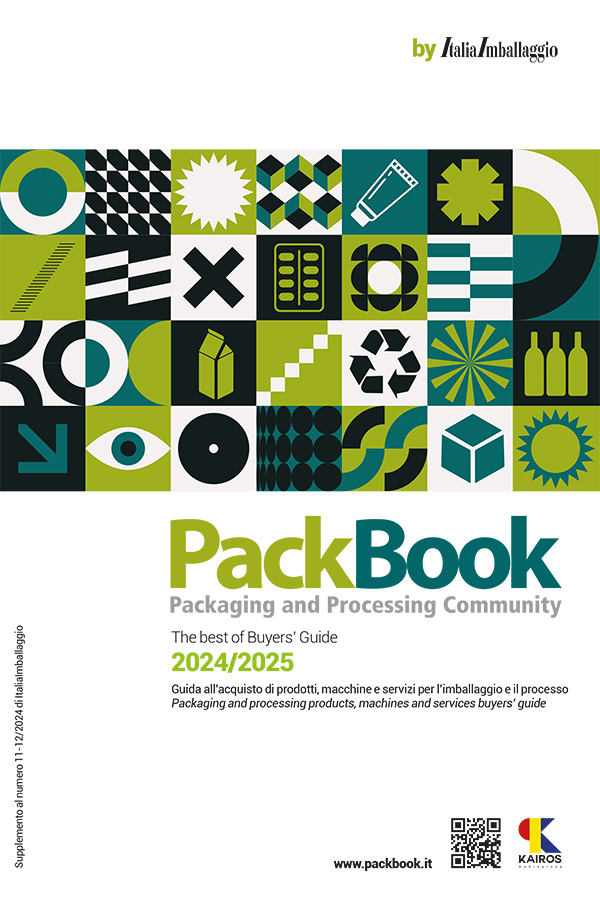