IMA: All-In-One supplier for pharma
Integration of know-how: at the recent edition of Achema, the Pharmaceutical Divisions of the IMA Group presented themselves as a technological “whole”, organizing an itinerary characterized by innovation.
Maria Costanza Candi
A surface area of 1,400 square metres was the setting for the IMA’s presence at Achema 2024, housing a broad overview dedicated to the pharma solutions of the Bolognese multinational. The offer ranged from pharmaceutical technology, to cosmetics, from experimentation on new materials, to digitalisation paths, with interesting spin-offs in markets like battery packaging.
The protagonist was IMA Pharma, the all-in-one supplier specialised in the design and production of machines and complete lines for pharmaceutical and nutraceutical packaging and processing, the assembly of medical devices, and the development of digitalisation projects characterised by sustainability and customer care.
The IMA Active division for solid dose solutions, the IMA Life division for the aseptic process and freeze drying, the IMA Safe division specialized in packaging solutions, the BFB division focused on end-of-line and the IMA AUTOMATION division for advanced assembly solutions of medical devices, all form part of IMA Pharma.

Innovation step by step
A visit to the IMA stand was, therefore, a veritable journey through innovation that extends beyond the pharmaceutical world, the focus of Achema, reaching very different markets, via sustainability and R&D on new materials, epitomising an approach oriented towards constant research into cutting-edge technology for the markets in which IMA operates.
Focus on solid dose Luca Cavazzini, Sales & Marketing Director, tells us about IMA, presenting, in particular, AQUARIA, the solution for the automatic washing of components and mechanical parts:
«The washing cabin is a component-washer that houses a rack on which to position the pieces of other machines, avoiding any type of cross-contamination. The double door permits the introduction of components through the wall, dividing the dirty area form the clean area. Great attention has been paid to sustainability for a monobloc design that guarantees the optimisation of detergent consumption, washing and drying cycles, in line with the latest trends that see multinational customers searching for increasingly sustainable solutions».
We must inevitably refer to the futuristic and all-digital set-up dedicated to IMA Active’s Competence Centre,
«a services hub - Cavazzini continues - that offers a test laboratory and the optimization of processes and new product development. Achema is an opportunity for the launch of the hub’s centralised services, which soon will offer customers a new test laboratory in which to carry out tests on the entire IMA Active range: granulators, filling machines, pressing machines, systems for tablet coating, washing booths and the continuous line».

Focus on the processing of liquids and powders in an aseptic environment
Continuing the visit, it’s difficult not to notice the design of the IMA Life proposal, with regards to which Marcello Ghelfi, IMA Life Sales Director for EMEA, talks about the integrated line composed of NEBULA, the high-speed decontamination tunnel and INJECTA 36, the advanced robotics solution for the filling and closing of Ready-To-Use (RTU) syringes and, more generally, isolated aseptic filling and closing lines that guarantee 100% sterility.
«The tunnel - Ghelfi begins - guarantees the 6-log decontamination of the Ready-To-Use package (that is, the tub/tray containing the RTU components) through a highly concentrated vapor stream of hydrogen peroxide (VPHP - Vapour Phase Hydrogen Peroxide) before entering the filling machine. There are three tunnel chambers, characterised by different colours that indicate the different processes: the yellow heating chamber; the red decontamination chamber using VPHP, and the third blue purging chamber relating to the cooling and removal of any H2O2 residues. At the end of the cycle the package is ready to be filled and closed. This is where INJECTA 36, the highly robotised solution for the high-speed filling-capping of syringes, carpules or RTU bottles, comes in. An innovative solution for 100% weight control, the machine ensures flexible and high-level production performance with up to 36,000 syringes/hour».

Focus on automation and customized assembly
The visit continues with IMA AUTOMATION.
«The division was created in 2016 after series of acquisitions» points out the Vice Chairman Lorenzo Maldarelli. «The aim is to deal with everything that is not packaging, acting on complementary business areas. Automation, for us, “means” machines for assembling plastic and metal components. The core of the system is a standardised platform that is offered with specific customisations according to the needs of the customer and of the product. At Achema, we chose to exhibit a platform for the assembly of insulin pens, but the modularity of the solution makes it possible to adapt it to any product. The Division also deals with the preliminary part of production. A good example are contact lenses, that is, the assembly of the two components that make up the lens, up to the packaging; there are also, however, lines for the assembly of numerous other solutions, of which I can mention electric batteries, with particular involvement in the construction part of the cell. It’s a growing sector for IMA, although medical is still a prevalent business, given the increase in solutions for self-medication and associated devices. Our division has 9 factories throughout the world with over 1,000 workers to respond to any request of an industrial nature».
Focus on digitalisation and AI
The themes present in the show inevitably include sustainability, digitalisation and solutions for customer service, areas about which we talked with Marco Cesari, Corporate Communications Team Leader in IMA Digital, who affirms:
«Innovative solutions linked to the monitoring of systems and advanced analytics stand out among our offer, deriving from the activity of the machines connected with IMA Sentinel. Among the priorities of our R&D there’s the collection of data, processing on cloud and display supported by AI and machine learning. Machine data is, therefore, made available to our customers in processed form with advantages on operating performance but also regarding IMA’s knowledge of its own solutions. Sandbox and Algomarket foster collaborative environments for the development of customised AI algorithms, which are made available to customers within an authentic market place. Our data scientists also work on projects specifically customised according to customer needs».

Focus on the interaction between machines and new materials
A final comment on one of the most discussed topics of the moment, new materials and innovative solutions, at the centre of the OPENLab network’s activity, which the Manager of the Ozzano dell’Emilia laboratory, Emanuele Simonini, tells us about:
«OPENLab is a network of laboratories that investigates certain chemical-physical properties of materials, with a focus on thermo-mechanical ones, to associate their structure with machine performance. It’s an essential activity for understanding the properties that can be measured in a laboratory and correlated with performance. As a network we study materials that already exist or ones which are about to be introduced onto the market in partnership with producers that are interested in researching the best solutions and studying their machinability.
We also indirectly promote the development of new materials thanks to our collaboration with universities, the financing of doctorates and generally with actions through which we seek to foster university research, contributing experience and industrial means.
The machines tests effectively make it possible to put the customer in contact with a material not yet on the market. Looking at the future, new materials - both paper and plastic/polymer-based - will need to meet full recyclability requirements, also for applications with high barrier requirements (e.g., oxygen and steam), even though the general trend is to look towards reuse, evaluating all the advantages and disadvantages, for example, via LCA. We can refer to the prohibition of disposable plastic plates, so far made with a thin layer of material and today, instead, very thick and heavy, in order to be reusable. This, actually, hardly ever happens, leading to a greater consumption of material for a product that the consumer continues to perceive as disposable. What is missing, therefore, is a systematic analysis of the impact of the life-cycle of many reusable objects, including reuse numbers for any type of packaging. Given that the direction taken is to focus on recyclable material, the risk is for this packaging to end up in undifferentiated waste at the end of its life-cycle if it’s too contaminated».

Looking at future possibilities, Simonini continues:
«My impression is that it’s possible to arrive at a paper base with hermetic seals and a thin layer that guarantees a barrier effect. It should also be noted that the material needs to be welded with a polymer which, even if in minimal quantities and only where needed, remains important, despite the crusade against plastics. Paper, if not treated, has a series of inherent limits such as low puncture resistance or low cutting resistance and high friction coefficients. In this context, coating solutions are emerging that make the material tougher, albeit in the presence of fragilities. Possible solutions for obtaining a recyclable and barrier mono-material in the pharmaceutical sector could include the strategy of using a fine layer of barrier coating - based, for example, on silicon or aluminium oxide - inserted between two layers of materials, one sealing and one protective, with the same chemical nature and functionalised/processed ad hoc. We are talking about the pharmaceutical sector, a sector that has a series of unsolved issues with respect to the use of post-consumer recycled material for which it is not always possible to guarantee the consistency of properties between different batches. Today, in fact, reference is made to weight percentages calculated on the annual average of post-consumer recycled content purchased by companies, the mass balance, making it difficult to meet the tough requirements imposed by the sector, without forgetting that in many countries pharmaceutical packaging is not recyclable because it has been “contaminated” by the product. The solution - Simonini suggests - would lie in chemical recycling which, by returning the material to the monomer form, allows for its full purification, obtaining improved recycled plastics with clear percentages that would resolve the variability of the performance levels of mechanical recycled material, although investments in time and money are still necessary to improve efficiency»
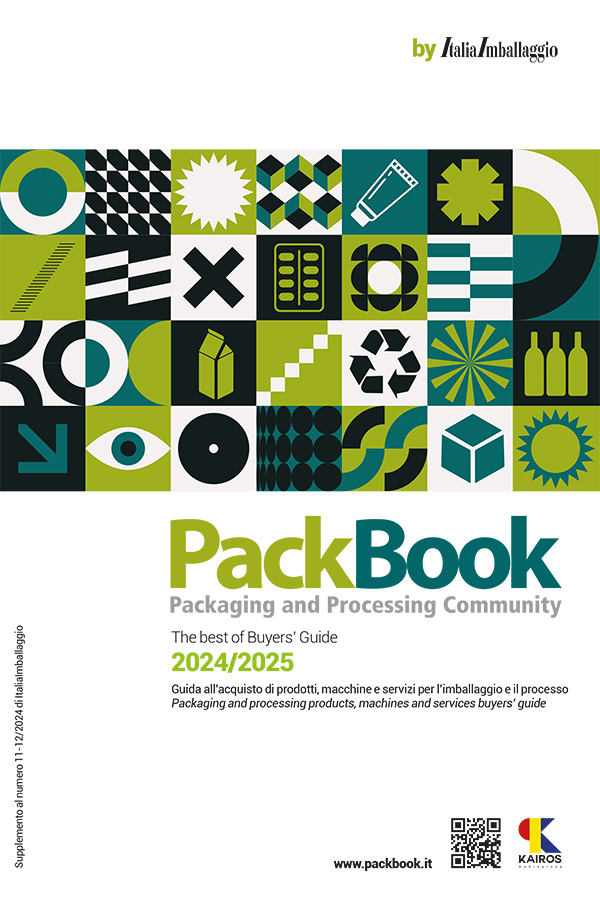