TempCoat® 1002F: a coating optimizes productivity
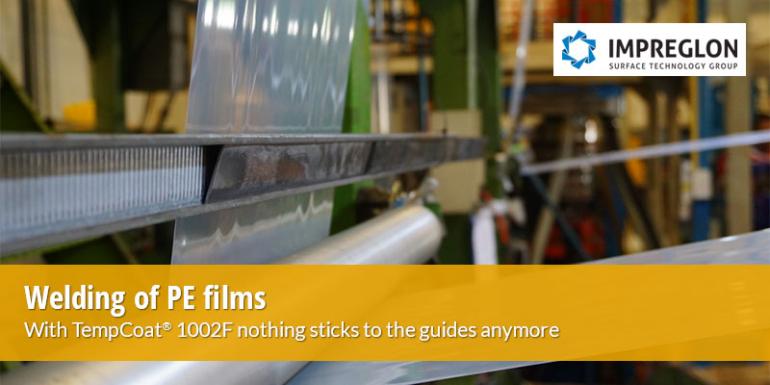
Having established the versatility of polyethylene and its diffusion in the packaging processes, Impreglon proposes the TempCoat® 1002F coating which gives solution to a contingent problem: prevent the PE film from sticking to the sealing bars.
In the packaging sector, PE tubular bags enable goods to be protected from humidity or simply from the air. The tubular or simple bag is filled and then closed with a film welder (in particular cases, the air contained inside can also be sucked out before closing). In this phase, however, there is often an accidental gluing of the film to the welding guides, which causes machine stoppages with consequent waste of time and money: the guide, in fact, must cool down in order to be cleaned before restarting production.
To avoid downtime, a manufacturer of film welding machines turned to Impreglon, who knew how to offer a simple and effective solution to the problem: TempCoat® 1002F, a coating that is applied to the surface of the carbon steel guides by means of a special painting process and a subsequent passage in a high temperature oven (about 400 °C) to allow polymerization.
The length of the sealing guides varies from 200 to 500 mm and currently from 100 to 200 guides are coated per month.
The solution guaranteed excellent results, but the customer also appreciated a second advantage: the coating, in fact, produces a more homogeneous distribution of the temperature, preventing the overheating of the guides, which in this way last longer.
Like all surface coatings Impreglon TempCoat® 1002F can be associated with a layer of PlasmaCoat® to further improve its hardness and wear resistance.
High wear resistance
Created with a view to offering increasingly high-performance surface treatments capable of satisfying non-stick, smoothness and good abrasion resistance needs, TempCoat® 1002F presents itself as the natural evolution of TempCoat® 1008F, distinguishing itself, in particular, for the increased resistance to wear and high operating temperature, the highest possible for a food fluoropolymer: 260° in operation up to a maximum of 280° as a peak.
Thanks to numerous studies and tests focused on giving maximum non-stick and abrasion resistance, TempCoat® 1002F is particularly suitable in situations where wear resistance is required in a continuous operating condition.
The most typical examples of application are in the field of plastic material welding (sealing bars, in fact), but also in the mechanical, packaging and food sector: in fact, it can be used to coat hoppers, sliding surfaces, cutting blades, molds and all types of kitchen plates (high-end pots or pans for crepes, wraps...).
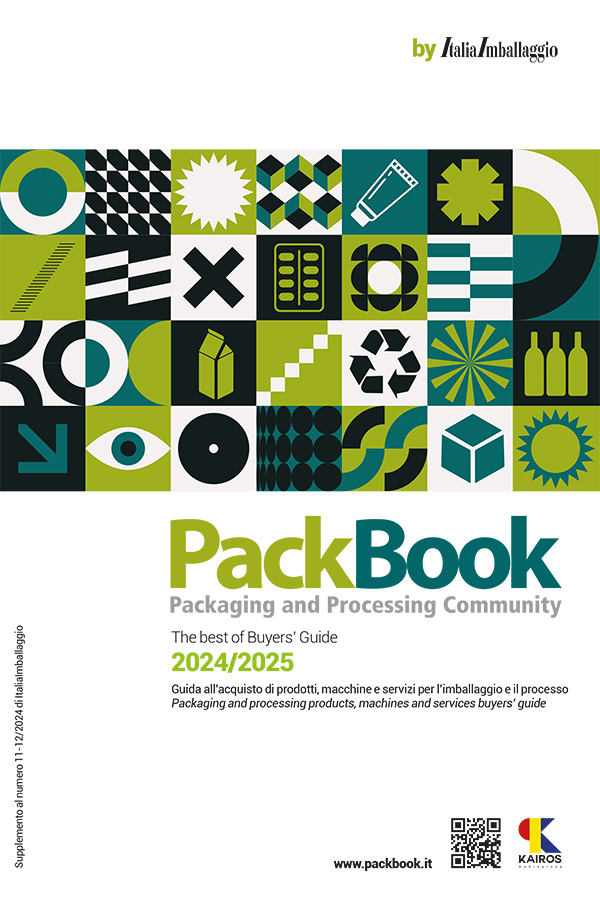