Unpredictable market? Adaptive production!
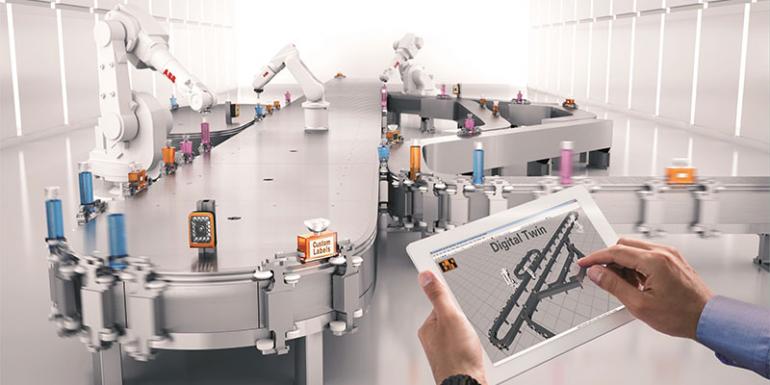
How e-commerce and marketing campaigns impact on production batches. The reflections of B&R, which promotes a paradigm shift based on the integration of industrial processes into a single software ecosystem. The advantages for goods producers and distributors, called to face a market that requires customized products in a very short time.
Driven by new purchasing models and new consumer behavior, classic production struggles to keep up with demand.
One thing: if the typical batches of a few years ago were composed of 300,000 pieces, today they are down to 10,000... meaning 30 times less!
In terms of productivity, considering a rate of 120 packets per minute, if before it was necessary to change format after more than 40 hours (5 shifts), now a batch does not last an hour and a half.
The format change has become strategic to keeping the batch profitable.
We face a market dominated by e-commerce, where the natural evolution leads us to have different packages, which can contain several different products.
How to ready oneself to produce a piece to be shipped in a day, instead of producing a lot to be placed in storage?
You can’t make operators go faster or buy new lines that satisfy all possible variations. Those who design automatic machines today live by following the customer’s specifications, “running” to design a machine only to find out when it is ready, after about 2 years, that the needs have changed.
There seems no way out, so it is time to look at new technologies to make a leap forward and find innovative solutions.
At this point we need adaptive machines and lines, so flexible as to solve the known present day challenges and future ones that have yet to appear.
The alternative solutions for the adaptive machine. There are 4 main technologies that enable adaptive production.
- The first involve tracks: intelligent factory conveyor systems, which replace the classic belt with independent magnetic trolleys. The tracks sort the individual products on individual routes, passing through specific processing stations to create unique objects. The track system is the backbone that makes adaptive production possible.
- The second is integrated vision: in addition to ensuring product quality, when integrated into the machine control it provides real-time information to understand and improve the process, also using Deep Learning - Machine Learning or Artificial Intelligence algorithms.
- Robots are the third enabling technology, a mechanical handling element, built without knowing what it will have to do. What can be more flexible than that ?
- Simulation and digital twins are finally the fourth technological pillar: allowing a complete virtual prototyping of the system, this helps to reduce machine design and factory production programming times and costs.
For this adaptive machine concept to work properly, the machine and line control architecture must be integrated. This condition is necessary in order to orchestrate all elements - control logic, motion, sensor data, operator interfaces, safety devices, diagnostics and maintenance, etc. - to be able to function properly in a single development and control environment. Operationally it means having a single application, a “brain” and a single network. Italian machine builders are known worldwide for their ability to innovate, to adapt, and they look to these technologies not to replace current machines, but to allow their manufacturing industry customers to enter new markets with enhanced capabilities and different business models.
Excellent concerns on the national scene, among the first to adopt enabling technologies for their machines, that surprise with uses and interpretations that even a vibrant technology supplier like B&R would never have imagined.
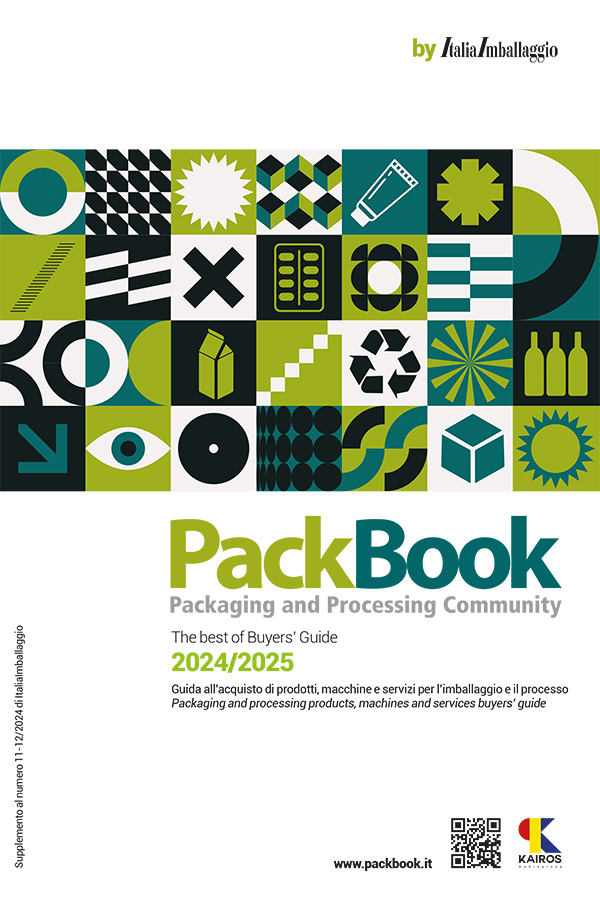