Ensuring flawless hygienic conditions
Thanks to their construction and processes of the stainless steel surfaces, Hygienic Design and Corrosion Resistant gear units from WITTENSTEIN ensure perfect hygiene in production facilities.
The special materials and geometries optimized to prevent the buildup of product residues in the Hygienic Design and Corrosion Resistant gear series from WITTENSTEIN guarantee the highest levels of hygiene on systems that frequently have to be cleaned with aggressive cleaning agents or corrosive disinfectants, such as in the packaging, pharmaceutical or chemical industries.
These automation components facilitate the reduction of bacteria and Covid-19 contamination and ensure the highest level of hygiene through electrochemical polishing of the stainless steel surface.
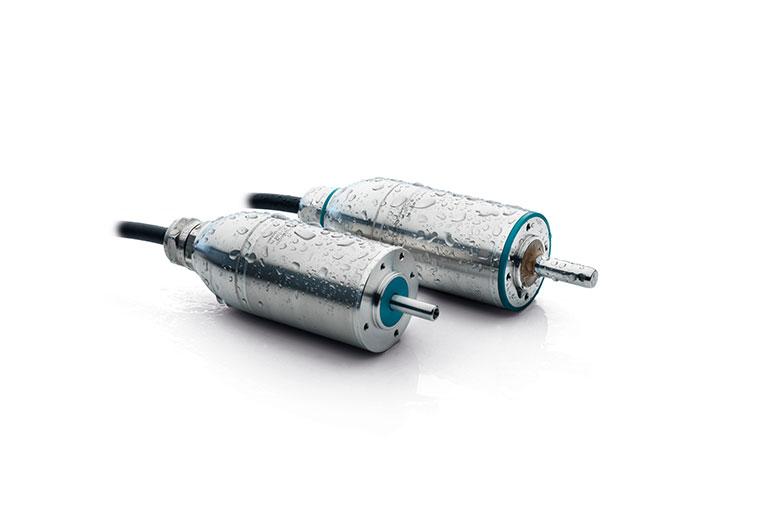
Hygienic Design
The gearboxes of the series offer maximum resistance to corrosion even in contact with those disinfectant fluids containing hypochlorites or alkaline foams, which could have heavy oxidizing effects on the components. The first in the world certified EHEDG (European Hygienic Engineering & Design Group), they have a shape with no dead spaces and smooth rolled surfaces, treated with electrochemical polishing to prevent the deposit of bacteria or polluting microorganisms, making their cleaning and that of the entire system faster and safer.
Motor and output seals are designed for food handling, preparation, processing and packaging plants, for the bottling, pharmaceutical and medical industries.
With this series it is not necessary to resort to the closure or carterization of entire drive units, with great economic and constructive advantages given the greater design freedom and optimized spaces.The output variants have either a shaft or flange (HDP) for compact, highly dynamic applications such as Delta robots, or an integrated motor for further space saving.
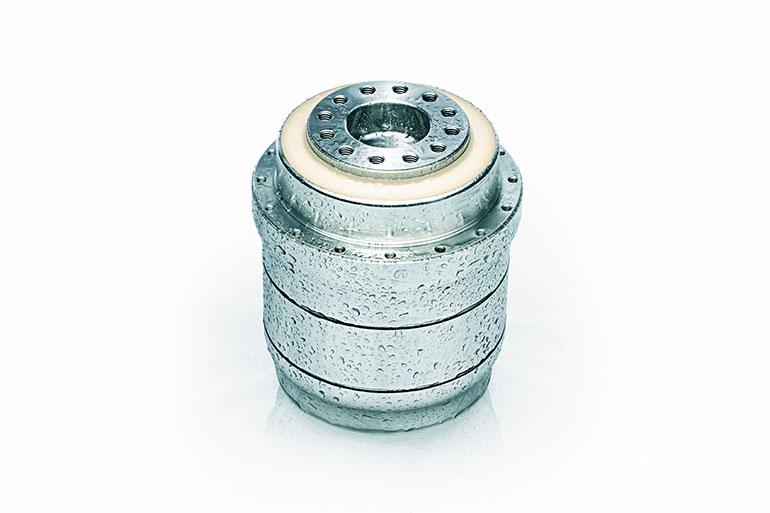
Corrosion Resistant
The coaxial and bevel-helical gearboxes Corrosion Resistant with shaft, flange or hollow shaft output offer total protection against rust and oxidation.
The input and output interfaces and various matching accessories, including couplings and shrink discs, are made of stainless steel, while the motor flange and housing are coated with a two-component paint, except for the centering, which is nickel-plated to maintain prescribed tolerances (g6). The series is lubricated with food grade grease, as prescribed by NSF regulations.
A complete offer. In relation to maintaining the hygienic conditions of the systems, WITTENSTEIN also offers the cyber® dynamic line brushless micromotors that can be integrated with simco® drives. The stainless steel version has an IP66/IP67 degree of protection, while the Hygienic Design version, made of stainless steel, offers a full shield (IP69K) against strong water jets, high-pressure steam apparatus or temporary immersion.
By virtue of their low rotor inertia, they are ideal for high acceleration, short travel and frequent speed changes, such as in pick & place applications.
Also available is a stainless steel version (IP65) with the screw fully integrated into the housing, ideal, for example, on high-precision bottling plants.
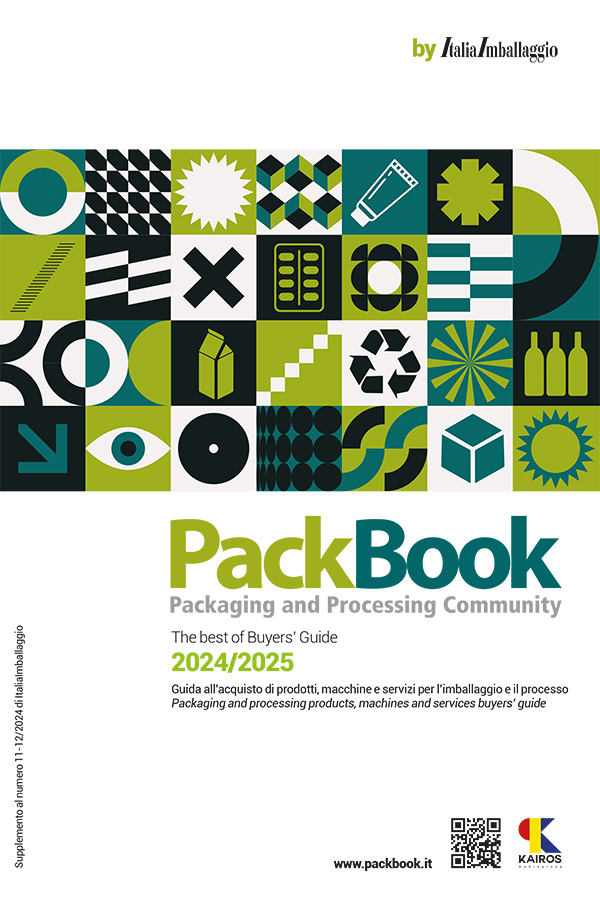