Cold form blisters in mono-material aluminium
An innovative and technological solution for medicinal blister packaging from Laminazione Sottile’s R&D team. A clear example of circular economy, the new packaging not only responds to all the hygiene and safety criteria required by the pharmaceutical market, but is totally recyclable and therefore destined to set new sustainability standards.
Ciro Sinagra, Anthony W. Ipock - Laminazione Sottile Group
In this article we describe the design process followed by Laminazione Sottile in order to arrive at the production of an alveolar blister for the pharma sector, involving tests on the most suitable material and its subsequent optimisation.
From the study of materials to research… and back again
The pharmaceutical market has been using plastic alveolar systems for years to package medicines in the form of tablets, capsules, dragees and the like. If the medicine is sensitive to humidity, oxygen or light, a complex multi-material that glues together polyamide/aluminium/sealing PVC is used to create the cells.
The alveolar structure is closed with aluminium laminates, of 20 to 25-micron thickness, fully coated with vinyl heat-sealable lacquers, which seal the blister. These structures are defined as “cold form” because the cells are cold-formed with a simple mechanical deformation operation. Although this is an excellent tried-and-tested packaging solution, multi-material blisters, however, have a problem: at end-of-life, they are “practically” non-disposable, given that it is very difficult to separate the plastic materials which are inextricably glued to the metal.
This situation gave Laminazione Sottile’s research group an idea: to research an aluminium alloy, subsequently coated with a few g/m2 of polymers, which alone allows for the cold mechanical deformation of the cells, as well as perfect sealing through heat sealing with traditional closing aluminium foil. The advantages of such a solution are numerous, starting from the perfect barrier against oxygen, water vapour (that is, zero WVTR and OTR) and light. In addition, in contrast with what happens today, the process would make it possible to externally coat the alveolar structure with any colour (which is today exclusively the colour of aluminium).
In this regard, depending on the type of medicine, the pharmacopoeia could, for example, indicate a characteristic colour which would help patients (perhaps obliged to consume different medicines every day to treat different pathologies) take the right medicine. The blister developed by Laminazione Sottile could also be perfect for packaging contact lenses: coatings sterilised in steam at 121 °C for 30’ or also by gamma rays could be used to allow for sterilisation of the cells containing lenses and a saline solution with pH normally between 7.2 and 7.6.
The design idea
The alveolar structure produced to contain medicines in the form of tablets, capsules and similar forms, which have to guarantee a barrier against light, water vapour and oxygen, has a structure as shown in figure 1 (standard stratigraphy). The production cycle of the multi-material is also somewhat complex.
To guarantee effective adhesion between the materials, it is necessary, in fact, to:
- obtain the lamination of OPA and PVC film with normally polyurethane adhesives, using technology known with the name of “solvent dry”;
- carry out a thermal treatment process of the coils after lamination in a climatic chamber with controlled humidity for a minimum of 3 days. The adhesive finishes its polymerisation many hours after gluing;
- cut into strips in the width requested by the customer.
The design idea was, therefore, to create an aluminium laminate with a thickness below 135 microns (total thickness of the coupled OPA/Adhesive/Al/Adhesive/PVC laminate), developing a mono-material system which, at end-of-life, can be disposed with aluminium like a normal can, to be then recovered and recycled in a few months. It is worth noting that in Italy in 2022 73.6% of aluminium packaging and 91.6% of cans were recovered and sent to recycling (official CIAL data)..

* From Simone Hermann, Amcor Product Development Manager Pharma, in Amcor, Innovative Hochbarrierefolien - Herstellung, Design und neueste Anwendungen, 17 May 2017.
Optimising the laminates production cycle
The main problem was creating a laminate in an alloy able to resist the mechanical stresses in the cold forming of the cells. The experimentation carried out made it possible to obtain a particularly fine metallographic structure to maximise the elongation at break of the laminate developed at a thickness between 70 and 100 microns. The thickness, in fact, can be established according to the geometry of the cells to be made. The isotropy of the materials was carefully studied, to ensure that the mechanical characteristics, measured with tensile tests with specimens carried out parallel to the rolling direction and at 90° and 45° with respect to the rolling direction, minimised differences in terms of breakage load, yield strength and elongation.
A laboratory prototype “pilot” mould was used to verify the feasibility of the cells (figure 2).

Control of the metallographic structure of the laminate. The laminate was characterized in terms of grain size, dispersion and size of intermetallic compounds with metallography techniques. The samples, after polishing, were attached with a fluoric solution and observed under a metallographic microscope with polarized light (figures 3 and 4).

4. 3D reconstruction of the metallographic structure.
Material anisotropy index control. Anisotropy measurements were calculated both with flat tensile tests of laminates at final thickness on specimens at 0°, 45° and 90° with respect to the rolling direction, carrying out also experimental measurements of Lankford coefficients, and on samples subjected to deep drawing.
To evaluate the deformation on the drawn parts, the strips were previously engraved with a precision laser (Yb:YAG Laser Marker - Manufacturer: IPG Photonics) and the incidence of the laser beam on the lacquered aluminium surface was analysed using a confocal microscope (figure 5).

Pilot mould tests. A small laboratory mould was constructed to carry out initial deep drawing tests on an impression considered sufficiently critical. Figure 6 shows a number of images of the prototype mould.

In conclusion
The mono-material solution studied - a coated aluminium alloy laminate, specific for the production of alveolar blisters for the pharma sector - could represent a revolution in pharmaceutical packaging. Laminazione Sottile Group’s R&D department is open to partnerships with automatic machine manufacturers, convinced that this innovative, hygienic hermetic packaging design, with a total light and gas barrier, perfectly and easily recyclable, could represent in the near future an excellent solution for pharmaceutical companies more sensitive to the concepts of the circular economy.
In this way, a product which today, at end-of-life, becomes an item of waste, could easily turn into a resource. It’s a concept which the aluminium world has already embraced for some time, overcoming the traditional “from cradle to grave” view, and designing today packaging solutions according to “from cradle to cradle”.
Ciro Sinagra, Anthony W. Ipock Laminazione Sottile Group (Caserta), Italy
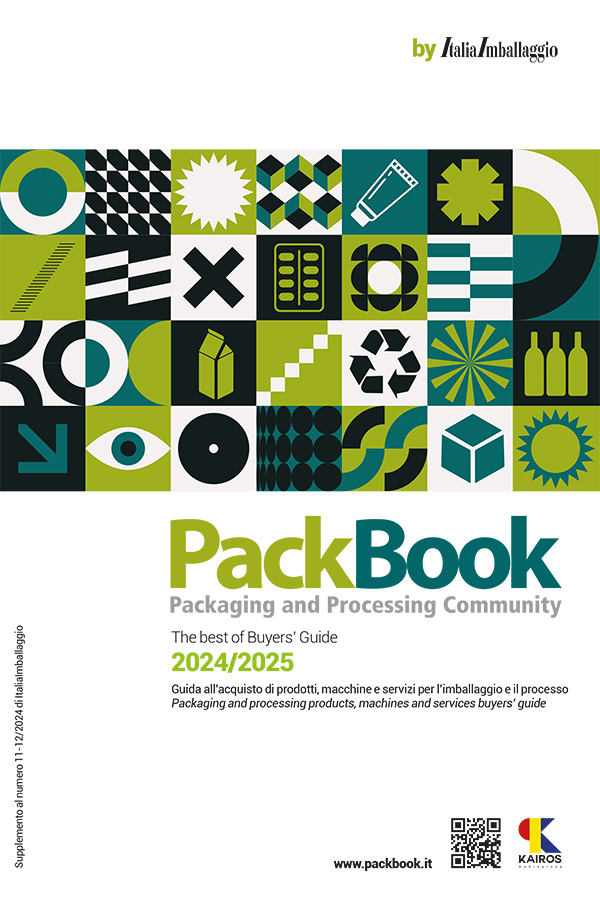