Experts in putting everything in the right place
Folding, feeding, transport, robotics: everything at D.C.M., a reference partner for industrial packaging, whose success is measured by customer satisfaction. And which responds with competence to the requests for sustainability expressed by the sector.
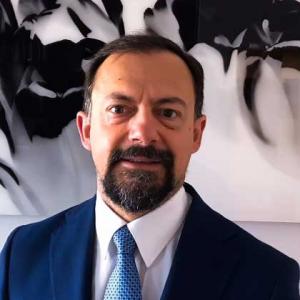
Quality, competence and innovation are just the words that best describe DCM, which has been operating for almost 50 years in the world of industrial packaging.
Founded in 1974, DCM’s core business is the distribution of folding machines for the pharmaceutical, paper converting and graphic arts sectors in general. However, the ability to evolve and the desire to bring innovation in-house have meant that, over time, its portfolio has been enriched with new packaging solutions: in order to meet the different needs of customers today it also proposes robotic feeding, conveying, handling and conveying systems.
And as its president Alessandro Casiraghi states: «Our mission is very clear: we want to help our customers increase the productivity of their lines».
A reminder that, in addition to the brand of excellence Guk, DCM also distributes Kraus and Autonox Robotics solutions exclusively in Italy, thus attesting itself as a benchmark supplier for machine manufacturers. In the following we enter into the merits of the technological proposals formulated by the company, which will have a showcase of excellence at Ipack-Ima.
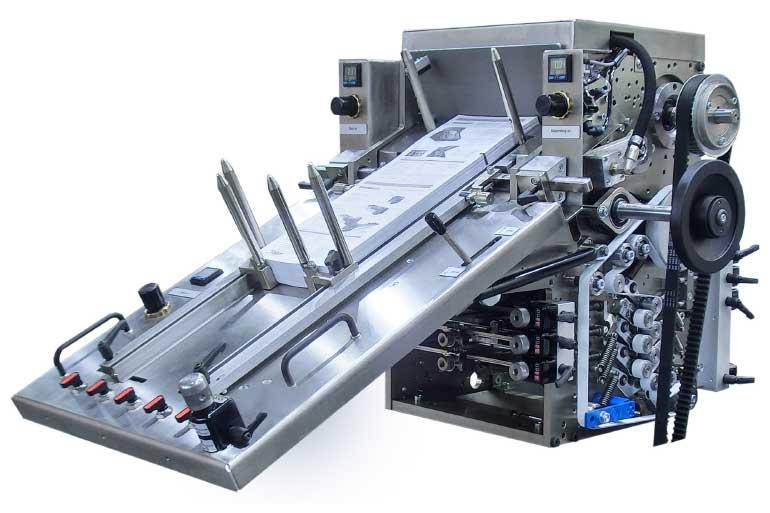
Unique expertise in paper folding
Over the years, DCM has acquired a unique experience in supplying and installing GUK products, famous all over the world for their practicality, sturdiness and reliability.
The formats produced by GUK machines are among the most varied, with folding lines reaching speeds of up to 600 pieces/min and guaranteeing higher quality of the finished product thanks to the consistency of the results and the use of unique and patented solutions.
Standard versions can be equipped with accessories and add-ons to further extend their capabilities, such as a vision system and automatic rejection to eliminate the risk of mix-ups.
«Thanks to Guk technology, millions of illustrative brochures are produced every day in Italy - explains President Casiraghi - and this has led us to develop an original method so that the productivity of the machines is never compromised; in particular, the preventive and scheduled maintenance plan for the folding lines has become fundamental for our customers».
For this reason, to enable a constant monitoring, for its folding lines DCM has created the Mercury system to give optimum performance of tasks allowing Industry 4.0 criteria machine interconnection.
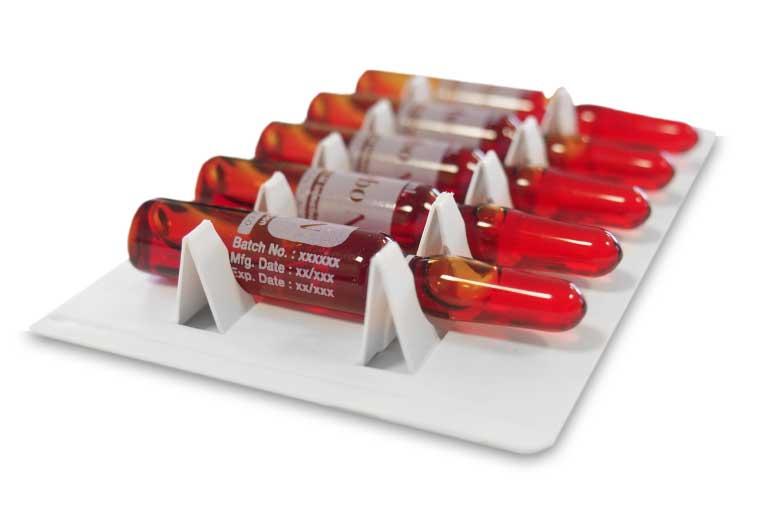
Feeding and transporting sustainable products
Kraus feeders are designed to work at industrial rates and are ideal for dispensing products at high speeds in various product sectors.
The lively focus on sustainability in recent years has led to the transformation of machines to accommodate the demand for environmentally friendly, ‘green’ packaging. The increasingly frequent use of recyclable materials in the production of disposable cutlery, cards, trays and tubs has also led to changes in the technological solutions adopted for their singularization and distribution, carried out fully automatically on the production lines.
The subject also closely touches the pharmaceutical sector, of which DCM boasts a very in-depth knowledge; and it is precisely through the know-how acquired in this area that DCM has created a new concept solution.
«Our desire was to follow up on the increasingly frequent demand to replace thermoformed plastic trays with an eco-sustainable support», explains the president. «From this desire and collaboration with our parent company, the Brava family was born; consisting of 3 different machines, it provides as a finished product a cardboard support that has 2 to 6 rows of cusps that, during packaging, go to accommodate products such as syringes, flacons and vials».
Since Kraus is not only synonymous with feeding and conveying but also with labeling, another recent development proposed by DCM is the Labeljack system, which is characterized by a high cycle speed, readiness for Industry 4.0 and the management of labels of different formats.
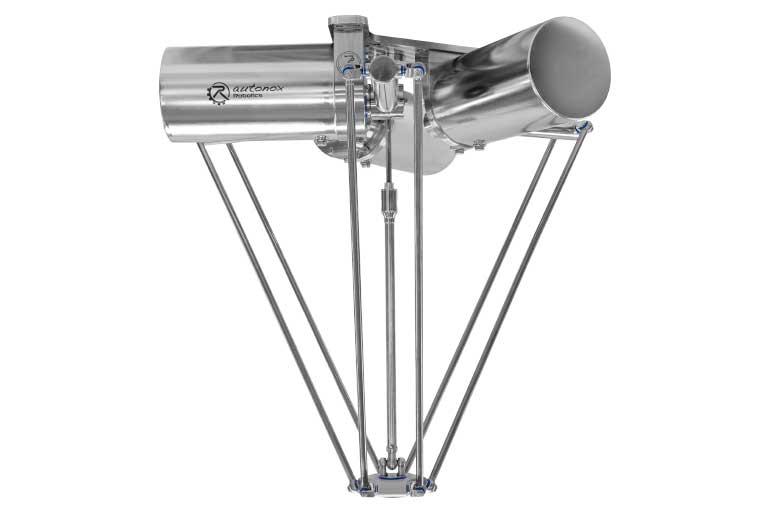
Industrial robotics and the digital twin
Technological innovation has led to a real revolution in the production sector, with the spread of industrial robots and their control software.
The evolution of information technology and electronics has made it possible to develop new advanced industrial robots such as those under the Autonox Robotics brand, capable of performing almost any type of packaging and handling activity on products of different weights and sizes.
The entire range is controller independent and is composed of duopods, Delta robots from 3 to 5 axes and anthropomorphic robots from three to six axes, able to work with sustained cycles and to meet the different requirements for payload and working areas: from 0.5 to 350 kg and from 200 mm up to 2257 mm.
The standard versions are completed by the renewed Hygienic Design versions, to work in primary packaging with IP69K grade protection and will be presented at Ipack-Ima 2022.
In recent years, as far as robotics are concerned, the need to simulate production processes and in particular to virtually test robots by means of a “digital twin” has grown increasingly.
«Always attentive to innovation and value creation, we have integrated into our offer the possibility of simulating the customer’s robotic application» President Casiraghi explains. «Through virtual commissioning software, we are able to propose the right robotic sizing and test the feasibility of a project; this is a great technological advantage that, in most cases, can replace the physical testing part of the machine».
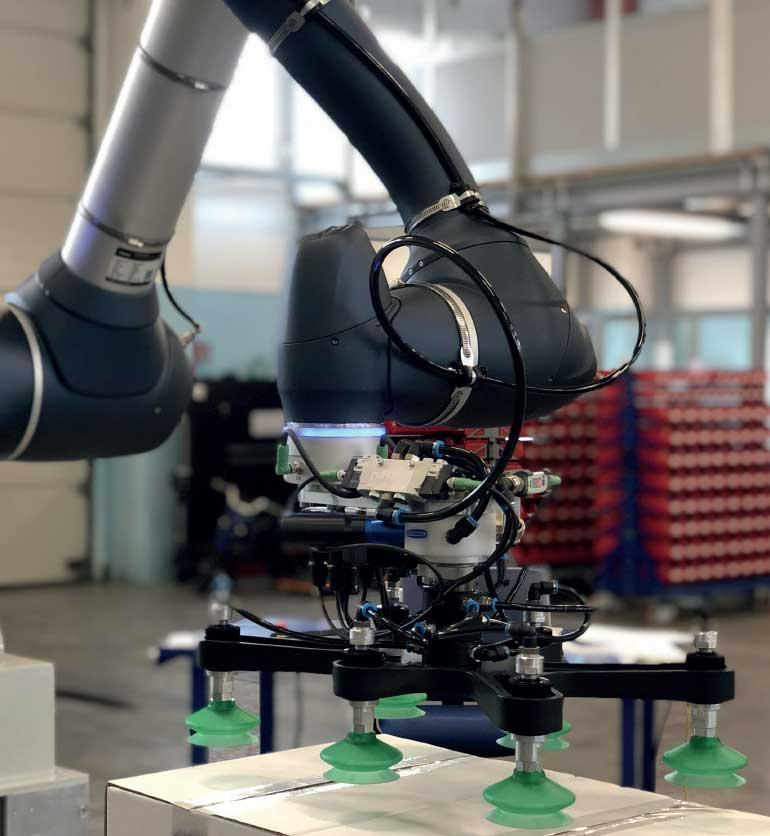
End-of-line expertise and innovation
Upstream of a production line, end-of-line equipment is tasked with handling and manipulating different types of products using efficient and precise machinery. The objective is to complete the production process, transporting the product and making the pallets that will then be shipped or stored in the warehouse.
Also, at the end of the line, DCM boasts an innovative and high-performance system; we are talking about “Squirrel”, an advanced intelligent automation solution for pallet assembly.
Totally barrier-free, it allows the operator to work in maximum safety thanks to the network of sensors that detect movements in the work area, drastically slowing down the speed of the palletizing arm. This allows the management of the completed pallet, while the island creates a new one in the opposite position.
In summary, here are the advantages of this collaborative palletizing island, which:
- improves working conditions by replacing manual palletizing;
- guarantees high safety standards;
- brings greater flexibility to one or more low-speed lines;
- allows palletizing up to 2,400 mm in height;
- allows the handling of boxes weighing up to 25 kg;
Through the integrated and easy-to-use software, Squirrel also allows you to create layer configurations by entering box dimensions, pallet size and box layout.
Pre- and post-sales support
«DCM doesn’t just mean solutions and products, but also first-rate consulting and assistance» explains President Casiraghi in conclusion. «In fact, over the years we decided to create a proprietary brand that would encapsulate all the support, consulting and training activities provided by the company and we called it “OPTIMAC”, which for us means maximum efficiency and professionalism in supporting our customers at all stages, from the preliminary design to spare parts and maintenance».
As promised, everything is now really in the right place.
On show at IPACK-IMA (Hall 2P - Stand B04 C03)
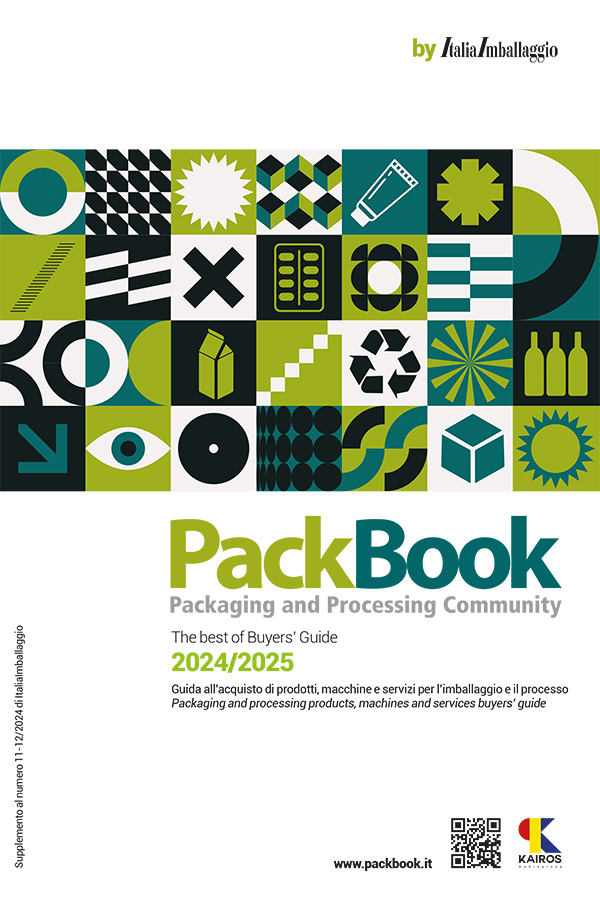