Mechatronic systems: the trump card
When very high levels of productivity, quality and flexibility are required, mechatronic conveyor systems come into play. Focus on SuperTrak, ACOPOStrak and ACOPOS 6D from B&R.
Smart Factory motion control offers some key advantages: maximum availability, high-speed conveying and positioning, rapid reconfiguration, and remarkable fault-tolerant quality.
High productivity is key and you can combine high speed, flexibility and scalability to improve machine payback (ROI) by increasing equipment effectiveness (high OEE) for all production batches, even the smallest.In parallel, thanks to the tools and know-how of the B&R experts, time-to-market is also significantly reduced.
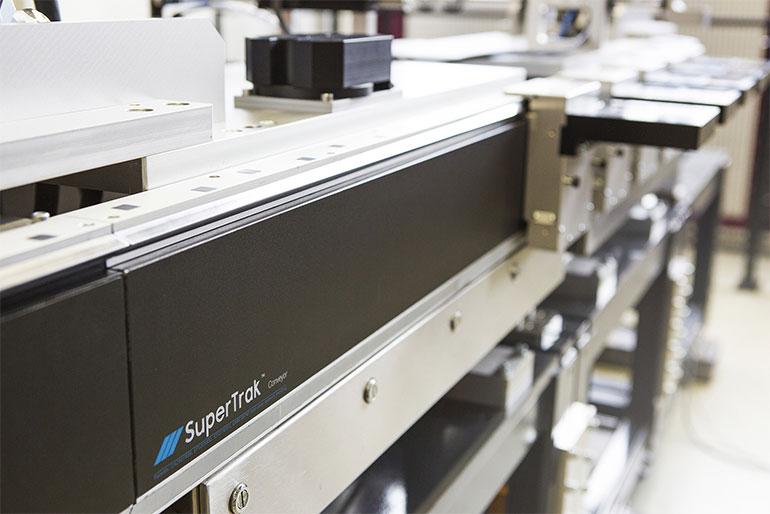
The tools at your disposal
SuperTrak was the first system to exploit electromagnetic field technology as a conveyor system in the automation market (the first application dates back 20 years).
It is composed of segments and trolleys, the latter controlled independently, which allows for flexibility and efficiency in production and energy.
Following the same technological thread as SuperTrak, ACOPOStrak is larger, scalable and flexible and is also designed for lines. It also features a high degree of protection and a wash-down variant is coming soon for more critical applications.
The trolleys can also be hot-swapped and, thanks to the identification of each trolley and process-oriented programming, it is possible to extend the economies of scale deriving from mass production to unit batches.
ACOPOS 6D, on the other hand, is based on the principle of magnetic levitation, adding further degrees of freedom compared to segment-based transport systems.
The shuttles incorporate permanent magnets that keep them suspended above the continuous surface created by the segments of an engine.
These systems allow products to be moved more efficiently, while maintaining a very high level of quality, and allow even the smallest batches to be produced with the speed and economy of mass production.
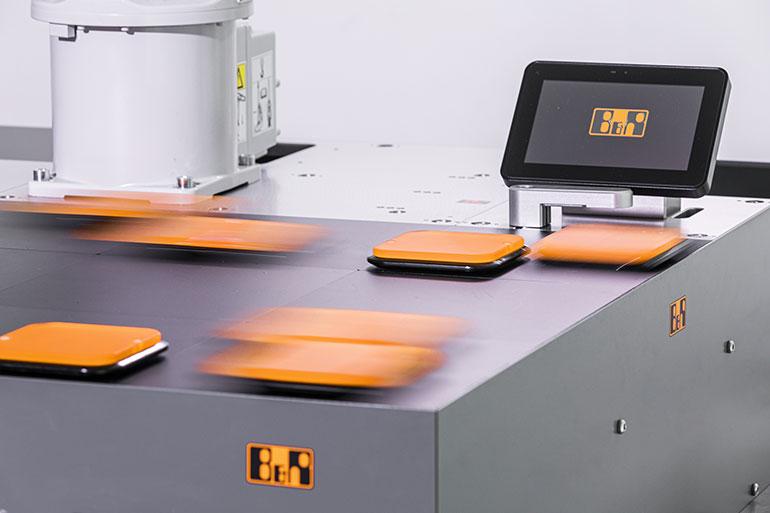
Virtual simulation of a real line
What happens when customers ask to optimize an existing production line or design one from scratch with these systems?
With dedicated tools, you can create a virtual twin of the system and watch it work; analyzing critical issues, you can reshape it to achieve the desired performance. The virtual simulation gives you a complete view of the final solution, allowing you to speed up the transition between virtual prototype and real machine.
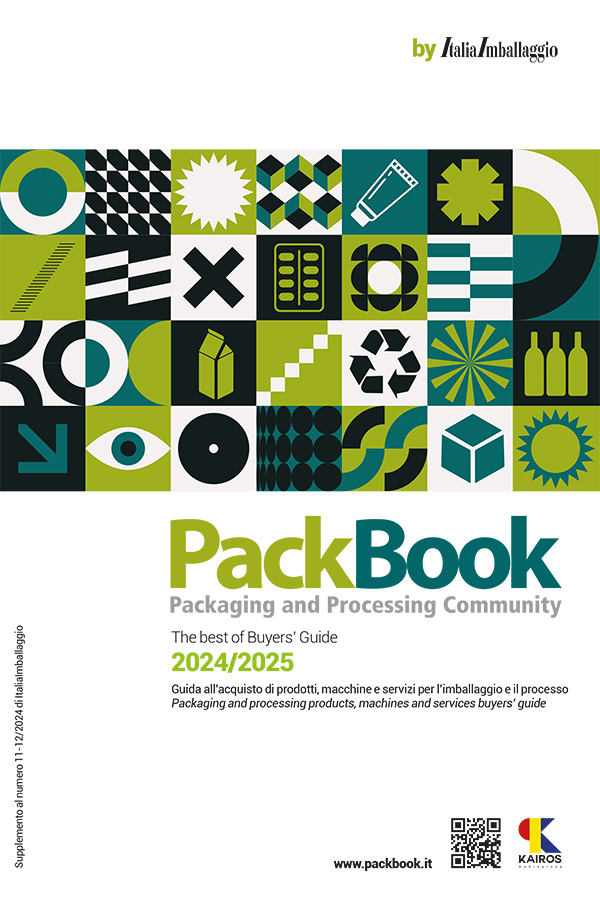