Flexibility serving efficiency
Tales of today
Ronchi Mario, leader in the sector of machines for packaging personal hygiene and liquid detergent products, presented at interpack a number of solutions intended to make, once more, a difference in the market.
Stefano Lavorini
Ronchi continues to work on product innovation. On the one hand, consolidating technologies already developed, such as, for example, the evolution of the robotic unscrambler and orienter of symmetrical and asymmetrical bottles without format change, the BETEL Δ 4-EVO, a modular machine with from 1 to 6 Delta robots, suitable for speeds up to 400 bpm. On the other hand, offering machines and solutions to reduce the time necessary to carry out format changes on the lines, in order to respond to the increasingly pressing needs of sales and distribution. Combining versatility and productivity in the best way possible is, in all events, the golden rule that guides research and development work, as the brothers Cesare and Gianmario Ronchi confirmed to me with brilliant sobriety during the trade show.
The emphasis is obviously on the two latest new developments: the robotic feeder of both caps and droppers, and the solution designed to integrate and complete the automatic format change system for filling and capping monoblocs.

Caps and droppers, for us they are of equal importance…
The new robotised feeder for caps and droppers is fitted with a single distributor and makes it possible to carry out format change completely automatically simply by downloading the files relating to the settings of the various caps or droppers in use: the time needed is around 2 minutes, against the 20 minutes for traditional format change. Other features include the very low noise level and no consumption of compressed air, which leads to obvious benefits in terms of energy consumption. The machine in the trade show, fitted with 2 anthropomorphic robots, was able to reach a speed of around 200 caps, or 150 droppers, per minute.
Not only short times, but also lower costs
The other new development relates to the devices that complete the automatic format change system on rotating filling and capping monoblocs. In practice, they replace the usual equipment linked to the format of the container to be used with flexible systems, such as the rotary feeder with grippers, which adjust automatically according to the size of the bottles, or the belt device that puts the bottles in step before entering the filler.
Automatic format change systems are valid not only because they allow you to drastically reduce the setting times and gain in productivity («in this sense the request that we receive from customers - Cesare Ronchi confirms – is to be able to carry out the format change of the entire line not in 6-7 hours as in the past, but in less than 10 minutes), but also because it makes it possible to eliminate costs of equipment and the times necessary for their manufacture, in the case of requests after delivery of the machine.
Increasingly close to customers
That this is a trend is also confirmed to me by Gianmario Ronchi: essentially, the users' request is for remotely controllable machines, which require a minimum of human intervention, as well as being very flexible, especially with regards to format change. This all, naturally, has to be achieved without affecting the levels of precision and quality of the production. For these reasons, Ronchi has reinterpreted the concept of personalisation in the last few years, offering the market the possibility of an increasingly direct contact and improving the quality of the partnership with its customers. It has implemented, in fact, in line with Industry 4.0 parameters, a digital system able to monitor and optimize the work of packaging machines.
The data collected are, moreover, the basis for predictive maintenance at line or factory level, which can be managed directly by the customer, as in the case of large multinationals, or offered by Ronchi as an additional service to an intermediate customer segment. Gianmario points out, furthermore, that the entire after-sales service has recently been digitalised with regards to the purchase of spare parts, with an online manual to identify, and request a quote for, the various components. In addition, a platform has been set up making it possible to carry out training and updating activities remotely, dedicated both to employees abroad and to users’ technicians, with tutorials, courses and live presentations of the machine in operation in the plant in Gessate.
Continuity in change
The strong vocation for innovation in Ronchi goes hand-in-hand with credibility acquired in the field in over a century of activity. It’s a result achieved by people who – I like to think – have always considered falsehood, imitation and sloppiness as “personal enemies”. The Cesare and Gianmario I know will never tire of waging battle against everything that is not simple, against everything that is not genuine. It’s an approach, a style that is now also the heritage of the third generation of the Ronchi family in the company: of Francesco, son of Cesare, and Alessandro and Fabio, sons of Gianmario.
What is more, the Ronchi family have been preparing the generational transition for more than 10 years with the assistance of external consultants. For now, the young members of the family are learning, first of all, to work together in harmony. It’s a good start.
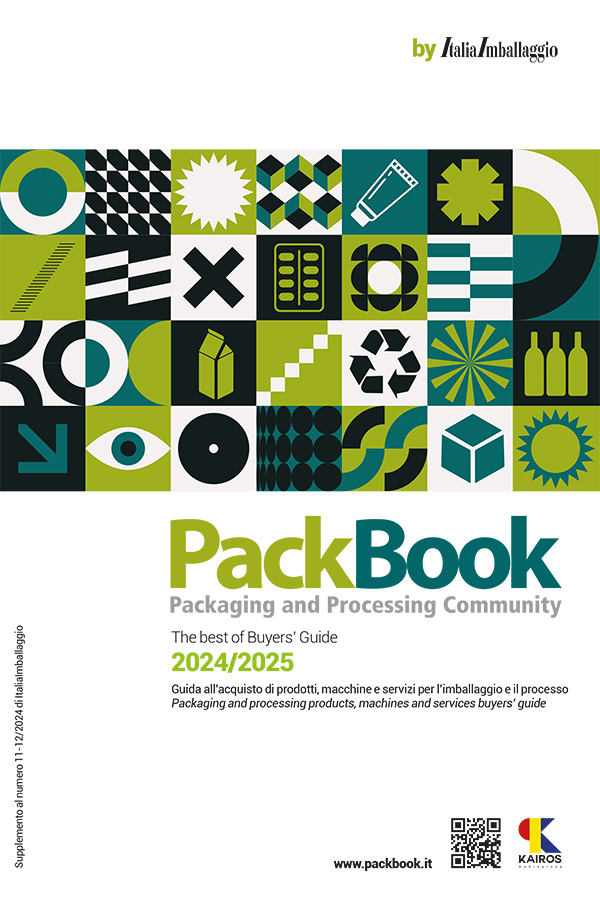