Hotmelt stitching: low-consumption gluing
With Volta by Robatech, lower adhesive consumption, reduced environmental impact and economic savings without compromising on the quality and durability of the application.
Robatech focuses on the hotmelt-stitching process, a low-consumption adhesive application method that allows for saving up to 50% on the product, reducing the impact linked to the increase in the prices of raw materials, since the system allows for operating costs to be kept constant or reduced.
Costs and benefits.
A saving of up to 50% in the application is an attractive option which must, however, take account of the costs for passing to hotmelt-stitching; costs and benefits vary according to the setup. It is, however, possible to precisely calculate the saving on adhesive obtained, taking account of multiple factors that can influence the process: the type of adhesive, the speed of production, the quality of the packaging material, the application system… To understand if hotmelt-stitching is worthwhile, it’s therefore necessary to compare the calculated potential savings with the cost of the investment, with reference to the single application. In all events, the quantities of adhesive are decidedly lower for the same bonding quality.
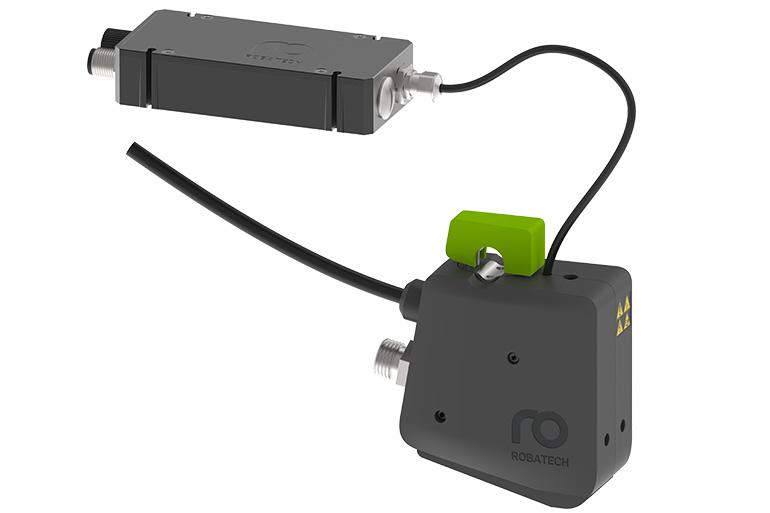
Volta application heads, designed for hotmelt-stitching.
Electric application heads are an ideal solution for hotmelt-stitching, and Volta stands out for reliability and precision. Designed for dot and bead applications with thermoplastic adhesives, it guarantees a constant and repeatable application, with low levels of wear, thereby minimizing maintenance interventions. A big advantage of Volta is energy saving: thanks to the fact that it works without compressed air, it’s possible to reduce energy consumption by up to 60%. With an operating frequency of 200 Hz, it’s therefore perfect for “dots” application, reducing adhesive consumption.
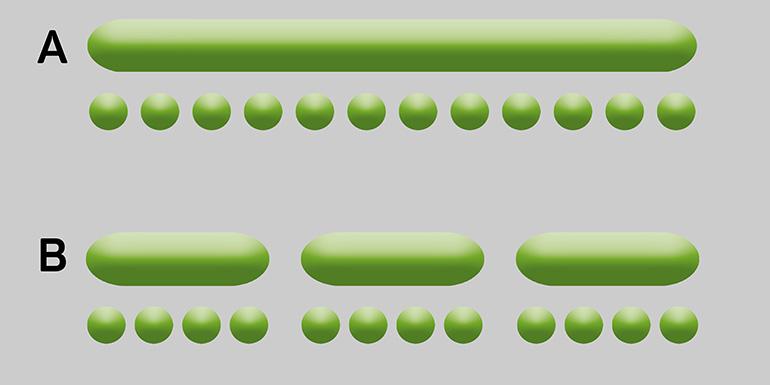
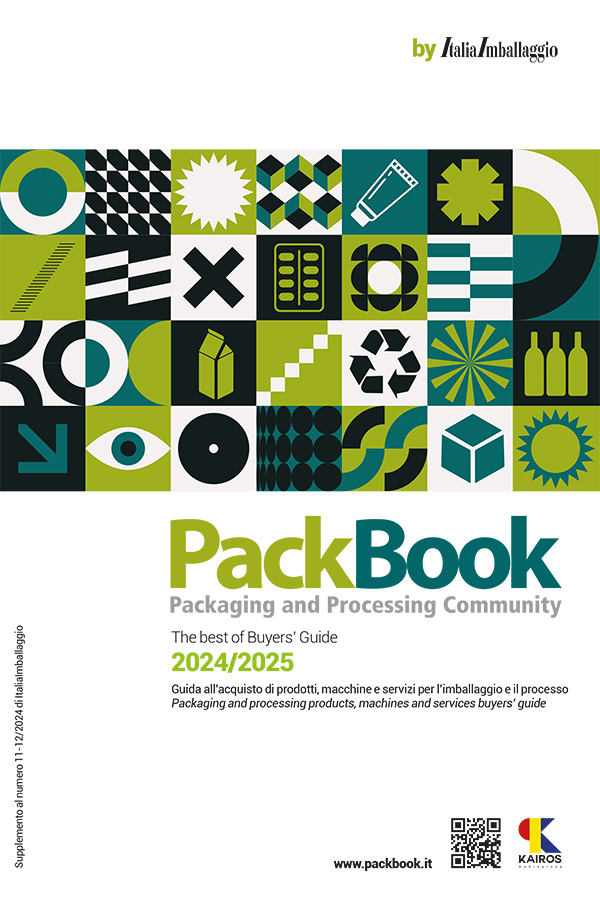