End-of-line and logistics optimised from A to Z
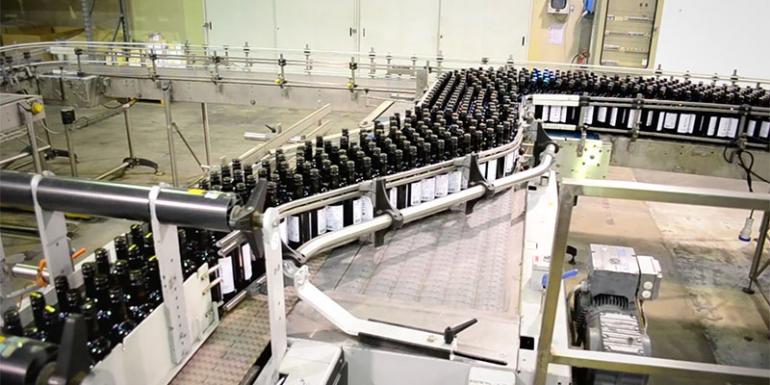
The wine producer CAVIRO once again chooses OCME and Robopac (Aetna Group) branded systems for the logistic and end-of-line efficiency of its Forlì plant, from palletising to the preparation of shipping bays.
With over 50 years of history in the wine sector, the Caviro Group, based in Faenza (RA), is strongly rooted in the territory and, at the same time, oriented towards the international market, with exports to over 70 countries worldwide.
In recent years, the Romagna-based manufacturer has consolidated its choice of Aetna Group as a reference partner for the supply of solutions capable of optimising end-of-line processes. The fruitful collaboration between the two companies is strengthened not only by their proximity to each other, but also by the sharing of an avant-garde entrepreneurial vision, which pursues responsible and sustainable growth based on the valorisation of resources, support for workers, technological innovation and the optimisation of industrial processes..
A state-of-the-art handling system
For the Forlì plant, which produces around 50 million bottles and over 24 million cartons a year, Caviro’s request was for a complete handling system for the finished product - from palletising to preparing the shipping bays - that would guarantee perfect compatibility with the company’s automated warehouse.
Aetna Group has therefore supplied a system of 11 OCME branded Auriga LGV shuttles, available in 3 different types of vehicles according to the spaces available in the plant and the tasks to be carried out.
In detail, 3 Auriga 25 Z vehicles were supplied, a series of stabilised LGVs capable of moving two pallets at a time for each cycle, also ideal for handling consumables (label reels, film reels for wrapping machines, empty pallets); 5 Auriga 15 PS LGVs, automatic laser-guided vehicles with covering forks, optimal for working in restricted spaces, used to move 1200x800 euro-pallets from the automatic warehouse (A) to the truck loading bays. The supply ended with 3 vehicles of the Auriga 15 CT series, counterbalanced forklifts, dedicated to handling the finished product on 1200x1000 - 1100x900 - 1200x800 - 1219x1016 pallets (Europallet - Japan - America) from the warehouse (B) to the truck loading bays.
The possibility of the LGVs to interface with the 2 automatic warehouses and with the customer’s management system made it possible to customise the product flow according to the plant’s needs.
Wrapping and palletising
But Aetna Group is not new to Caviro. In the Romagna-based manufacturer’s plant, the wrapping and palletising processes have been optimised thanks to Robopac branded solutions, including: the Helix HS 30 rotary arm wrapper, as a line for wrapping pallets coming from the bag-in-box production line for the foreign market; Genesis HS50 and Genesis Futura 40, automatic rotary ring wrapping machines.
It is also significant that Caviro was one of the first companies to install in its plant the rotary ring Genesis Thunder, top of the range of the series, dedicated to the demi-pallet wrapping line and rewrapping on mother pallet.
This supply has defined Robopac as Caviro’s exclusive supplier of pallet wrapping solutions, thanks to which, with the support of the Robopac TechLab, the wine cooperative has registered considerable advantages, starting from the better and more effective pallet stabilization to the reduction of costs deriving from the use of consumables (film, layers).
Overall, therefore, Robopac and OCME technologies have enabled Caviro to achieve its objectives - greater logistical efficiency and end-of-line productivity with state-of-the-art automated solutions - consolidating a long-term partnership.