Additive Manufacturing meets packaging
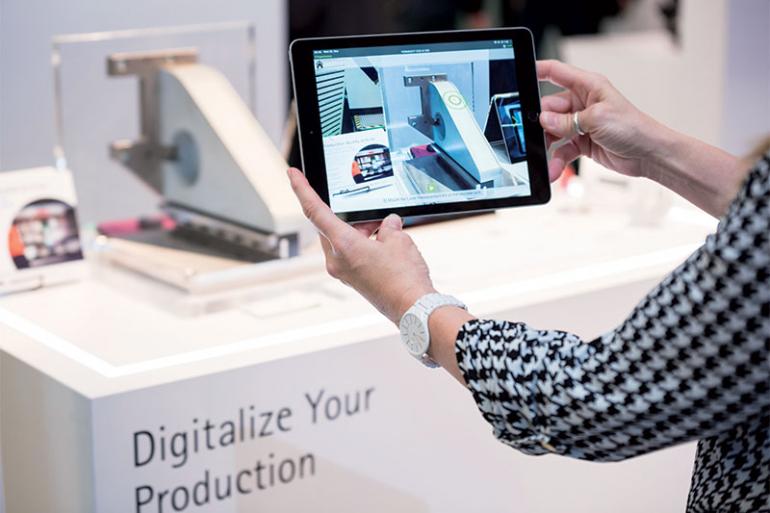
There is still much to “explore”, yet Additive Manufacturing is a topic of great interest given that, in the not too distant future, it could revolutionize the way of producing. The suggestions obtained from the round table promoted on the topic by SPS Italia.
Maurizio Cacciamani
“Smart Production: Additive Manufacturing as enabling technology for Industry 4.0”, the first of the four appointments running up to the 2020 edition of SPS Italy, was held at the end of January at the Milan Polytechnic (Bovisa centre), adjacent to the Milanese Competence Center MADE.
Moderated by Franco Canna (Innovation Post) and Bianca Maria Colosimo (Milan Polytechnic MADE), the day involved 24 speakers from all sectors involved in Additive Manufacturing: machine manufacturers, material suppliers, users, consultancy, universities, subcontractors.
Four moments marked the times of the round table: a general introduction to Additive Manufacturing (AM), with the presentation of the new dedicated area in SPS; a summary of the trends that emerged at Formnext (annual European reference fair for new technologies at the service of industrial production that Messe Frankfurt organizes in Frankfurt: 860 exhibitors at the last edition of November); the presentation of MADE (the Competence Center for Industry 4.0 headed by the Milan Polytechnic) which recently launched the first call for 1.5 million euros of 50% co-financing in favor of small and medium-sized companies ( as many as 71 the applications received for 51 million euros); applications in the medical field with the creation of customized prostheses.
The second and third phases were dedicated respectively to the automotive and aerospace sector, traditionally at the forefront of the AM sector, while in the fourth, packaging was discussed with the contributions of Filippo Rosa (Research & Innovation Engineer IMA), Riccardo Della Martera (Sales Engineer Manager EMEA Relayr), Giacomo Coppi (Head of Digital Supply Chain and Manufacturing SAP Italy), Marco Giuseppe Andreetta (Sisma Product Marketing Analyst), Giuseppe Cilia (Sales Manager Stratasys Italy), Ferdinando Auricchio (Full Professor at the University of Pavia).
AM in a nutshell: The fields of application
Additive Manufacturing (AM) is an ESG (Environment Social Government) technology, as it enables the production of lighter products: you save material, you have less processing waste and you consume less energy. Other related advantages are the reduction in the number of components (with, in practice, the relative decrease in references in the warehouse) and the possibility of creating products with complex shapes ... But, watch out: in the packaging, pharma and food sectors, complex shapes can create some problems, as they do not facilitate machine washing.
AM is however ideal for prototyping or for producing small series, for maintenance and updating on equipment and machines. It is therefore not a technology to be used for large series (even if the aviation industry, for reasons related to safety standards, uses AM for important productions).
It is also ideal for making inhouse plant and machine spare parts, thus allowing to drastically reduce downtime.
In general, 60% is used in prototyping and 40% in production. In the not too distant future, this ratio will be reversed.
The engineering design style
The use of Additive machines (which can use 25 different technologies) must be planned from an Industry 4.0 perspective, otherwise the potential offered is not grasped. The organizational aspect and the training of people are of fundamental importance for both production and design: the 3D project is in fact different from the CAD project and enables the solution of different problems.
Hence one needs to change the design style, keeping in mind however that you can’t produce everything, as the pieces produced with AM have limited mechanical characteristics, due to the materials avialiabe that do not always offer adequate fatigue resistance.
However, new plastic, thermoplastic and metallic materials (brass, bronze, copper) are being studied and heat treatments that improve mechanical characteristics are beginning to be used.
It should be noted that the University of Modena Reggio Emilia is carrying out research in the powder metallurgy sector. As far as the machines are concerned, there is a tendency to make bigger and bigger ones, while for the products hybrid production is taking hold, that is, a piece is made partly with traditional machines and then with AM.
Last in line, one of the most important phases of production in AM is post-processing, the purpose of which is to improve the finish of the piece produced, to color it or to reinforce its structure.
The how and why of starting
Many approach this new technology by adopting small machines in the company to produce prototypes or small lots (typically spare parts). In any case, the insertion of the new machine needs to be carefully planned, because if the planning is carried out correctly, you can obtain a return on investment in 6-9 months. Profitability - it has been underlined by many parties - depends on the correct application, for which the feasibility study is fundamental, which though is not easy to carry out since few operators have a specific culture in this regard. It should be remembered, however, that machine manufacturers, universities with competence centers such as MADE and research centers offer valuable support. And as for Industry 4.0, AM offers the opportunity to create new business models.
Training
Many companies have an internal “academy” for customer courses and offer a valuable consultancy service. In the field of training, universities are taking on a fundamental role, both for the technical part and for the management part. Universities with Competence Centers (specifically MADE) are establishing themselves as aggregation centers, where the skills of the many players involved converge: users, machine manufacturers, material suppliers, communication software and hardware suppliers, service companies.
The incentives
Additive machines are incentivized with tax credit, provided they are inserted in communication networks for the exchange of data but also to primarily allow remote monitoring as well as cloud data collection.
Relayr (a company active in the industrial Internet of Things) is studying, in particular for OEMs, the possibility of accessing pay-per-use contracts as an alternative to purchasing or leasing; but has already made avaialable assurance services of results guaranteed.
A valid alternative to the purchase of AM equipment remains the definition of a partnership with a subcontractor (this is the case of IMA, which avails itself of a partner with whom it has a partnership for the creation of prototypes).
But what can be actually done in packaging?
It must be said that the meeting promoted by Messe Frankfurt - SPS Italia was intended to “generally inform about the technology” and very few examples were cited. As for the packaging sector, Sisma has created an injection molding head characterized by a capillary network for cooling (impossible to create with traditional machines): thus an increase in productivity was obtained during molding since the heat is more easily dispersed.
Other examples concern the realization of granulators for the pharmaceutical and anti-counterfeiting systems.
In conclusion, for those who wish to learn more, we point out a very useful color publication in A5 format entitled “Formnext AM FIELD APPLICATION GUIDE” published by Mesago: over 60 pages in English on rapidly evolving technology that for the next few years will revolutionize the design and production of objects.