PouchLab turns two: results and future goals
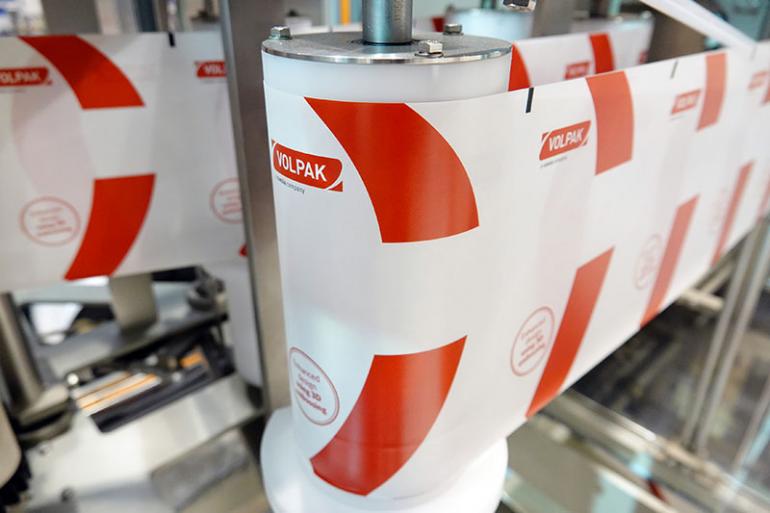
In the Center of Excellence born in June 2019, Volpak (a Coesia company) supports customers and partners in the development of new sustainable flexible packaging solutions.
Created thanks to the support of the Coesia Centre of Expertise Sustainability (which centralizes the collection and dissemination of data and projects aimed at supporting the green strategies of the various companies in the group), for the past two years Volpak’s PouchLab has been the place where its expertise on materials and automation is concentrated, but it is above all a space made available to customers and suppliers to develop recyclable or low environmental impact pouches.
Machines and instruments of excellence are therefore at the service of brand owners who need to set standards for their packaging, aiming to optimize the package size, need to consider downgauging packaging or aim to explore new materials for their products. The Lab is also meant for those industry players who need to compare the behavior of different structures, test machinability, double check the performance of their film, develop new sustainable solutions or new re-closable features for flexible packaging. Two years after its foundation the structure is a strong asset not just for Volpak customers, but also for manufacturers of film converters, caps and zippers, technological centers and raw material suppliers.
A protected place for research
The laboratory is located in a special area within Volpak premises, which ensures maximum confidentiality and dedicated closed boxes for material storage. All takes place in a controlled environment, which also relies on Volpask’s technical expertise.
The pouch-forming equipment provided by PouchLab, namely a new generation HFFS machine, serves for both flat and stand up pouches. Customers can control and monitor seal temperature, seal pressure and seal time, while also supervising film tension and monitoring film elongation throughout the whole machine process.
About the characteristics of the materials tested in the Lab, films are becoming much better, showing a positive evolution of their physical properties and better functioning on the machines. This is due to a substantial improvement in the processes adopted by suppliers and converters already with full PE film that behave very well in terms of sealability, mechanical properties, and spout application. Today, beside Paper structures, the industry is heading towards Full-PE and Full-PP films. Future challenge will be to enhance their performance and barrier properties.
PouchLab also played a primary role in developing the sealing process for a full paper recyclable stand up pouch we can now find in the market place currently produced on Volpak equipment.
Other tools provided by this area include an electrostatic charge measure tool, which can measure any material with utmost accuracy and calculate its electrostatic charge, a stress test machine, to obtain clear, accurate and manageable information about pouch stress resistance, a high speed camera to investigate the root cause of any issue, and a powerful microscope to analyze seal quality. A 3d printer is also used for rapid prototyping the parts to be tested.
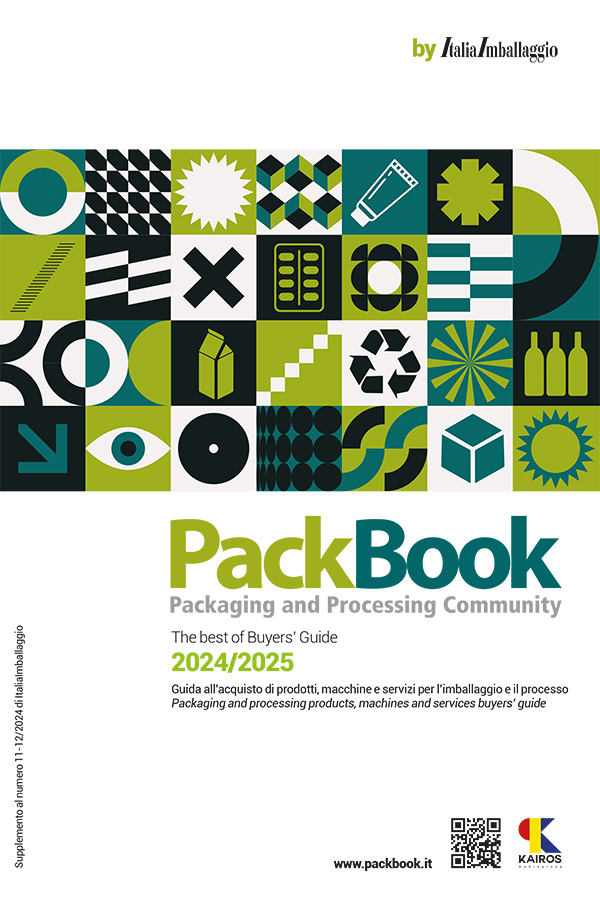