Supply chain logic between sustainability and innovation
Marking and traceability, packaging quality and aesthetics, handling that looks at product integrity: from ACMA a series of answers that make attention to detail and dialogue between supply chain players the key to its path of sustainability and digitalization.
Luciana Guidotti
ACMA, a Coesia Group company, is a company that has “made history” in packaging and today is ready for the new challenges - sustainability and innovative materials first and foremost - that the sector must face.
A global leader in the design and manufacture of packaging machines, exports about 95% of its solutions, has more than 250 employees and R&D investment of 5% of sales, with a particular focus on the confectionery, soaps and detergents, tea and coffee markets.
Roberto Lattarulo, ACMA marketing manager, spoke to Italiaimballaggio of the new features finally live at the fair and the vision of a complex market such as the 2020-2022 two-year period.
Novelties that respect traceability and aesthetics
«ACMA brought three solutions dedicated to confectionery», Lattarulo tells. «Two machines already in the portfolio for chocolate wrapping and the Material Gate unit, a system developed by our R&D department, which allows tests to be carried out on materials of any kind to prove their performance on a twist wrapping, for example, the double twist wrap.
We start with the CW 800 for spherical or egg-shaped chocolate wrapping, which makes double twist fold wrapping or the rolled type on an aluminum base. In its new version, it is equipped with a laser marker, which inconspicuously but legibly prints whatever alphanumeric string you want on each individual fold wrapping. In this way the client is able to indicate batches and expiration dates not only on the secondary packaging but also on the primary packaging without affecting the aesthetics».

«Moving on to the CW 600 - Lattarulo continues - this is a machine for flat-based products that, at a speed of up to 600 pieces per minute, wraps chocolates with different fashions (up to 6 types). At Ipack-Ima we decided to show the latest style developed for this machine, portfolio with banderol. The novelty is twofold: the particularly sought-after wrapping type and OptiMate, the smart HMI panel developed together with Coesia, installed on Coesia Group’s proprietary hardware».
In a market where difficulties in sourcing semiconductors and components are evident, the Coesia group can rely on its own supply chain, which now allows ACMA to extend the HMI solution to increasing numbers of machines, equipping them with ergonomic interfaces with great responsiveness and processing capabilities.
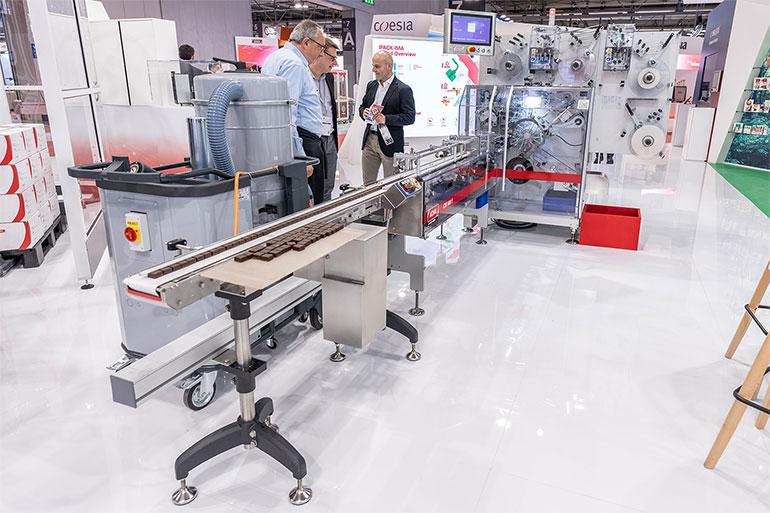
Innovative materials without secrets with Material Gate
«Part of Sustainability Lab, the third solution on display is Material Gate: an innovative test unit made ad hoc by ACMA engineers, to carry out tests on materials of any nature, proving their performance on a single twist fold wrapper» intervenes Roberto Lattarulo.
«In general terms, the confectionery market is moving toward the reduction of plastic-based or multilayer materials, which requires machine manufacturers to find effective solutions in terms of productivity and aesthetics in using alternative products».
He continues: «Thanks to a servo-driven unit connected to a computer, our Material Gate makes it possible to use different laws of motion to test materials and measure their performance in a real production context».
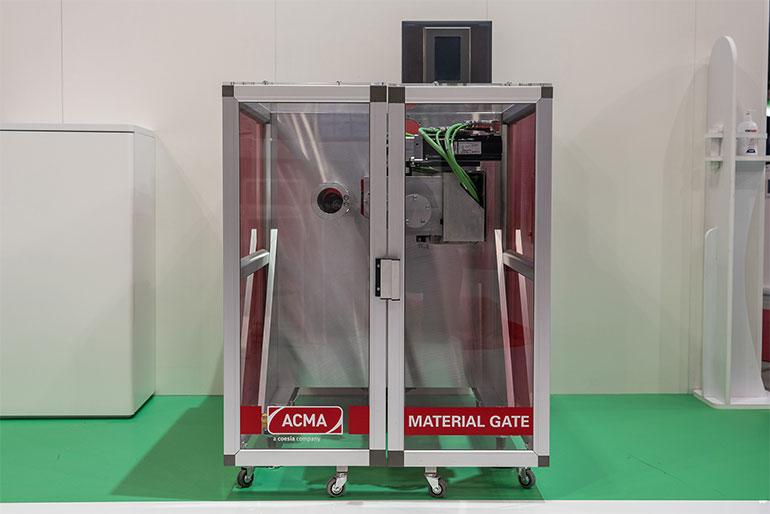
Increasingly green
Moreover, ACMA has long since started the Sustainability Lab, which has precisely the task of testing the behavior and machinability of new-generation materials, both for flowpack and wrapping, with a focus on those where twisting can create critical issues.
«At first, the laboratory performs the examination of new solutions proposed by customers or wrapping manufacturers, offering preliminary feedback: if positive, the material can be tested. This is followed by a first phase of in-depth investigations by the Coesia Engineering Centre, which studies the characteristics of the material according to the final application and compares it with the “best in class,” in accordance with our knowledge, thus defining an ad hoc Delta Report.
In a second phase, the material is directly tested on a dedicated flowpack or, for double twist wrapping machines using Material Gate, thus proceeding to fine-tune the material in the case of a producer, or the machine if it is a producer.
By following this process, one arrives in production with a material that is really adequate to the needs and without an onerous waste of products».
«A step-by-step process - Lattarulo goes on to clarify - that allows us to implement new products as well as to modify our offerings, even in terms of updating and retrofitting existing machines, thus reinforcing the scope of our sustainability choices. ACMA machines, even today, are partly based on mechanical movements that, at least by current technological standards, continue to guarantee high precision and speed. In short, we aim to support customers at this moment of momentous transition and to acquire know-how for the development of the machines of the future».
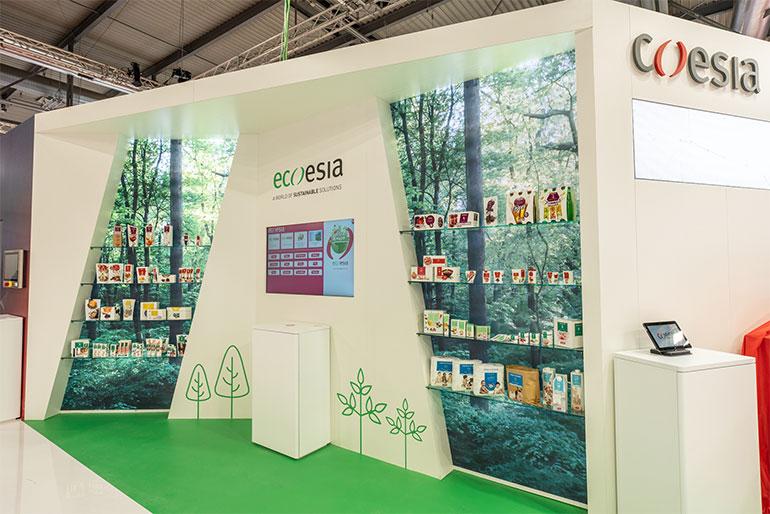
Quality, Industry 4.0 and cybersecurity
«The world is moving toward mass customization and flexibility. Everyone wants to be absolutely unique», Lattarulo concludes. «It is clear that machine productivity is closely linked to return on investment, understood as technical reliability, constant speed over time, and wrapping quality. ACMA is globally recognized precisely for these values: whether confectionery, soap or tea, it is in fact the care of the product, its handling, that makes the difference, especially in markets such as chocolate and soap, where this aspect is particularly critical».
Quality unquestionably combined with flexibility, which makes it possible, for example, to guarantee rapid format changes on the same machine, strengthening the return on investment and reducing the space occupied in the factory».
Lattarulo adds, «Then again, today we aim for an increasingly “smart” machine: with OptiMate, the connected panel, we develop and accelerate operations such as format changeovers, machines troubleshooting, maintenance, technician training, the access to wizards and digital documentation directly on the machine. We aspire, then, to connect the machine park and production lines with PerforMate, the IioT platform developed with Coesia, which enables remote line control to identify issues, track performance, and have full control over factory operations.
Looking at the operator, more connectivity also means more ergonomics, in a much more intuitive and safe operating framework. The safety part is obviously basic: if a machine is not safe, it doesn’t leave the ACMA factory».


To stay on the industry 4.0 theme, with UltiMate, the predictive and preventive maintenance phase is also the subject of a specific offering.
«These are solutions that have been on the market for some time and demonstrate how the concepts of digitizing production are becoming more established. OptiMate, for example, is integrated by default on some machines such as the CW 800, HW 900, the JW700 and now on CW 600 as well.; PerforMate has already found several applications, while UltiMate is about to be supplied to one of ACMA’s many established customers».
These innovations impose the utmost attention to cybersecurity and, for this reason, the Bologna-based company is carrying out a series of assessments with external certifying bodies in order to ensure the security of the systems developed.
«With Coesia’s Remote Assistance, we close the circle», Lattarulo concludes. «Designed to do remote assistance to our customers, saving time and resources, and also to guide them in fine-tuning through the use of advanced audio and video sharing technologies. These same technologies were then used during the COVID-19 emergency and enabled us to provide support to our customers and ensure business continuity that would otherwise be impossible. One example above all: remote Factory Acceptance Test (FAT), which has now become a permanent fixture in our business processes».
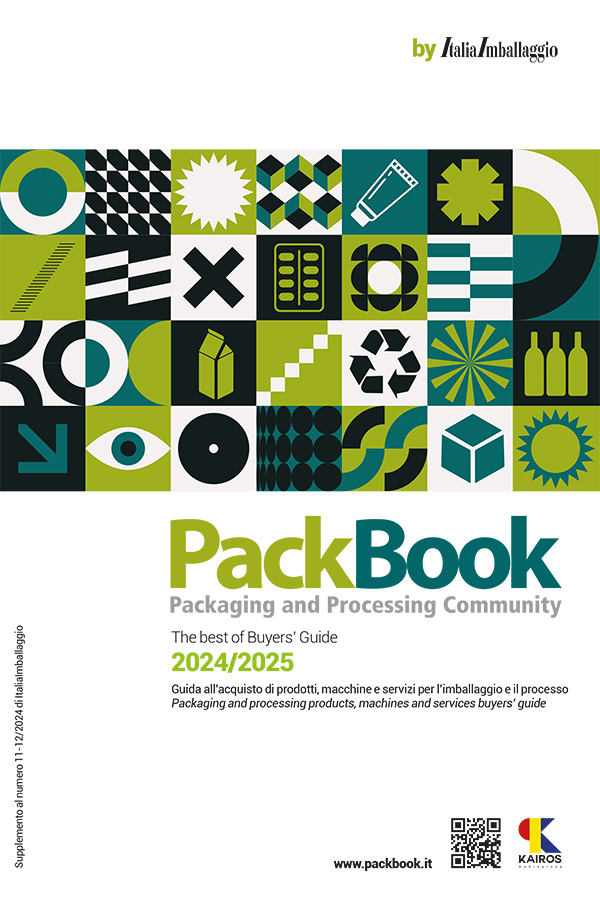