Enabling technologies for the smart factory
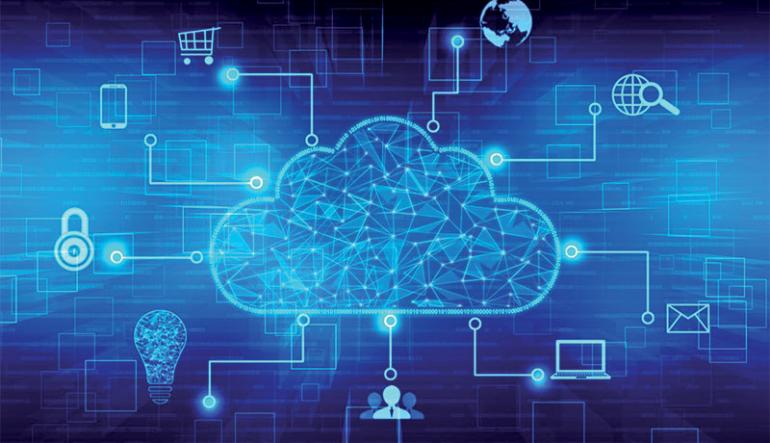
Many are the strengths of IOT technologies, but it is not easy to build the infrastructure that is able to allow the business to make a forward leap. The role of Competence Center, suppliers, OEM, system integrator and end user.
Maurizio Cacciamani
Many are the strengths of IOT technologies: bi-directional interaction with control systems, sophisticated dashboard development environment (mashups, i.e. the combination of elements, data and information of a heterogeneous nature, to obtain more useful results than the source data), integrability of business systems, unlimited connectivity, codeless Machine Learning model development environment, real-time detection of anomalies, availability of advanced statistical analysis tools, installation on cloud or on-premise (i.e. installed on the user’s computer or on a corporate server).
It is not easy to integrate enabling technologies and it is useless to hide it: OEMs encounter difficulties because if it is true that there are successful implementations (like the one illustrated by Emanuele Quarin, Digital Industrial Operations Director EU Electrolux), the opposite is also true. All the members of the supply chain, each in their own role, must enable the parts of the smart factory that must be easy to manage with multifunctional devices that can be easily adapted to different needs.
They are very important:
- connectivity, so that data can be available in real time using smart phones, tablets and smart watches;
- the involvement of people, so that they can, as in Elettrolux, bring added value by helping to solve their practical problems;
- training at all levels (from managers to operators), which should be further developed by the various government plans.
What does the SMACT Competence Center do? «Competence Centers are “a” solution, not “the” solution to the transfer of innovation to SMEs» says Matteo Faggin, General Manager SMACT Competence Center. The transfer takes place through guided tours to successful pilot lines and installations, training /refresher courses for managers and operators. The course catalog (also with online webinar) is under preparation, whose program will not overlap with what universities, masters and companies already do. Important services offered are the management of innovation processes, funding calls (in September the second of 900 thousand euros). In the future new processes and new solutions will be implemented.
Rapid product change. «It can be done successfully!» explains Carlo Cuppini, Head of Global Account Managers - Southern Europe B&R Automazione Industriale «with intelligent transport systems: the line must be modular, equipped with switches and parallel branches, but above all expandable: the trolley must be independent in route, speed and load».
In terms of integration, the robot controller must communicate with the machine or plant controller, sharing alarms, statuses, commands and the robot program. Further integration will see the disappearance of the robot controller into the machine/plant controller. B&R has developed its own vision system to optimize its integration into its systems to better manage traceability and even very small batches.
Nature solves complex problems with simple solutions. «Starting from this consideration - says Alessandro Ferioli, Industry Segment Manager Festo Italia - the company has launched a few years ago the Learning by Nature project that is the basis of research activities on materials, software, integration». Ferioli stressed that “pieces” of research are inserted in the products citing the example of the collaborative robot, where fluidics are combined with the latest innovations in the digital field. Ferioli pointed out how fundamental in these times is the training especially of managers, called to manage significant organizational changes in the company.
The evolution of safety. The availability of distributed controls allows with a single software the programming of devices located in different places even far away from the controller.
«Safety and security are two sides of the same coin» explains Giovanni Sangiorgio, Divisional Manager Systems Pilz Italia. «It is necessary to design from the beginning the new machines taking into account these two sides so that you don’t have to place expensive “patches” afterwards». Pilz has internally developed a collaborative robot to understand the safety and security issues involved and to develop ad hoc solutions.
Safety & productivity. According to Paolo Zanetta, Product Marketing Manager Automation products Datalogic, today safety is no longer at odds with production efficiency. To avoid the neutralization of safety sensors there are models that are difficult to neutralize or intelligent sensors that prevent tampering. The evolution has led to sensors that are insensitive to environmental disturbances that could cause line stoppage and to optoelectronic models that can monitor safety simultaneously on several different zones that vary dynamically. Laser scanners are now able to detect the measurements of the objects that gravitate around the mobile robot, once sent to the controller this calculates the location and the path of the vehicle.
How to secure a control room. «You only need to install on Windows PCs, which make up the vast majority of the control room hardware, only and exclusively the software strictly necessary for the operation of the line» states Andrea Scattina, Channel & Sales Manager Italy Stormshield, a company of the Airbus group that operates in the cybersecurity sector offering scalable solutions able to meet all needs, even those of SMEs, who are the most numerous customers. To combine performance with security the company has created blocks that are able to prevent the line from going wrong because of an intrusion.
How the PLC evolves. For Alessandro Favero Product Manager Control Systems & IO Phoenix Contact the PLC is evolving towards the edge: thus it is programmable with high level languages, it sends data to the cloud, it is able to remotely monitor with email notification of problems, it can install Apps available from stores, it manages security through controlled access or VPN access. These features can already be found on the PLCNext of the German company.
Servicing. The machine manufacturer can sell to the final user a series of services, which allow both to get a lot of added value. Rockwell’s Connected Machine Web Platform is the convergence point on the cloud for users and service providers such as: predictive maintenance supported by augmented reality, sales and parts management, continuous and central monitoring of installed machines. «Having a winning IOT strategy - explains Simone Cerizza, Team Leader & Solution Consultant Smart Manufacturing and Area Project Manager MADE Rockwell - means having a very clear ecosystem model in mind that includes not only hedge computing and the cloud but also block chains and artificial intelligence».
How to avoid human error in security. «In teleassistance/remote control, security plays a fundamental role, which many think they can solve by using non-industrial products in the factory» states Simone Dal Toso, Product Manager Networking Telestar. The security of the connection often sees the IT and OT departments on two different fronts, which have great knowledge in their respective fields but are not always open to the needs of the other department. Since security problems always derive from human error, it is necessary to use simple products, always set accesses with 2 factors (e.g. password + biometric data): as a 100% secure system does not exist, it is essential to provide procedures that make intrusion very difficult.
Why is a datum produced? Why is a datum consumed? «The answer to these questions - says Michele Frare, General Manager Factory Automation Panasonic Industry Italia - allows you to understand, thanks to the OEE (Overall Equipment Effectiveness) verification, if processes are improving (production, maintenance, quality control, etc.). All the improvements must be made according to the business and can be realized with the use of new enabling devices». The data processed by Artificial Intelligence and Machine Learning allow you to keep an eye on the overall state of the equipment in real time thanks to the hidden choice of dashboards and KPIs. The OEM is now required to make a quantum leap: it must become, supported in this by suppliers, a specialist in advanced connectivity from a technical, application, business and training point of view for its end users.
More EtherNet less fieldbus. To create an infrastructure correctly, industrial devices (cables+connectors) must be used so that the connected devices can transmit data efficiently without slowing down the system. «The danger - says Marco Artoli, Product Manager Lapp Italia - is to use methods that are good for IT but not ideal for OT, such as cables or linear topologies». Artioli also recommends creating infrastructures that are broader than current needs and easily expandable to support ever-increasing data traffic, reminding that Lapp brings EtherNet up to the sensor.