The FoodTech line
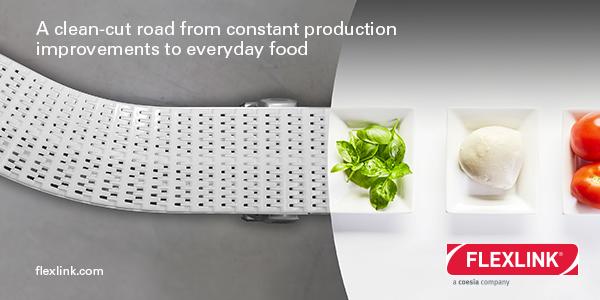
Systems for line automation and conveyor belts by Flexlink: compact design and low maintenance requirements enabling simple changes to line layouts, delicate handling.
For nearly forty years FlexLink (a Coesia Group Company) has been working to improve the efficiency of its customers' production lines, assisting them in layout design and set-up and supplying cutting-edge solutions for the transport and handling of products.
FlexLink boasts particularly valuable know-how in the food industry, for which it has created “FoodTech”: a specific range of solutions.
Fast, clean and precise production flow
FoodTech is a family of systems and services for advanced technology transport conceived specifical ly for the Food and Dairy industry.
The FoodTech systems development team has in-depth knowledge of the criteria that producers in the industry must factor in to guarantee the safety and efficiency of the line, along with the challenges that they have to face on a daily basis to ensure the highest possible product quality. This has led to the development of bespoke solutions designed to increase production efficiency, putting operator safety to the fore.
The systems in the FoodTech family stand out for their extremely compact design and low maintenance requirements, greatly simplifying any changes to line layouts. They also simultaneously ensure precise and delicate product handling, designed to minimise the risk of contamination. All of which translates int o reduced production times and costs. The use of highly automated lines also significantly reduces the margin for human error, ensuring high quality standards that remain constant over time. In practical terms FlexLink aims to guarantee an increase in Over all Equipment Effectiveness (OEE) of 1%, simultaneously delivering a more rapid return on investment.
Hygiene and efficiency: a combination of value
A clean production environment that complies with high standards of hygiene is particularly important in the context of non-packaged food, both in humid and dry conditions. Non-compliance with these standards can result in product recalls or, even worse, health problems for the final consumer, with dire consequences for the image of the brand.
In contrast, a line with a simplified design and conveyor belts that meet hygiene standards makes cleaning operations easier, reducing downtimes and overall operating costs with a positive impact on the whole supply chain.
The design of FoodTech systems guarantees maximum product hygiene while reducing conveyor belt cleaning times by approximately 25%, with the additional option of installing CIP (clean-in-place) modules or similar.
In designing its systems the company has followed the guidelines of the European EHEDG consortium (Europea n Hygienic Engineering and Design Group), but has also gone further by developing a modular belt in stainless steel, called the WLX, which is the only system on the market able to comply with the strict “3A” sanitary standards.
Optimisation of time and space
Every second that a product spends moving from one machine to the next is lost for production purposes. Careful planning is therefore required to set the correct flow, balancing the transport speed with the need to guarantee the appropriate handling perfor mance. Not only is time optimised, but so is space. FlexLink, through carefully reasoned line planning and the use of compact systems, manages to reduce the overall space required by between 20% and 40% compared to competitors, freeing up more room for increased production capacity.
Operators also benefit from a more open working area from the viewpoint of both safety and accessibility. The compact design of the elements also has a positive impact on the simplicity of line relocation or modification. And again from the viewpoint of design, the FlexLink range is based on modular components that greatly support flexibility. The standardisation of components simplifies the line planning and assembly phases. At the same time their innovative design makes both pre-assembly and installation quick and easy. Finally, the company keeps a large stock of parts at its warehouses in locations spread throughout the world, thus ensuring rapid response times in the case of both new orders and spare parts for pre-existing lines.
FLEXLINK: FACTS AND FIGURES
Based in Gothenburg (Sweden), FlexLink has operations in over 30 countries and is represented in over 60 countries. In 2017, FlexLink staff had over 1100 units, which have been growing steadily since 1980. Today the company can offer its customers a portfolio of solutions that cover the various phases of line handling and control.
FlexLink is part of Coesia, a group of industrial and packaging solutions companies, based on innovation and operating globally. The Coesia Group companies are leaders in the following segments: automatic machines and packaging materials, industrial process solutions and precision gears.