Stable, safe and... plasticless palletizing
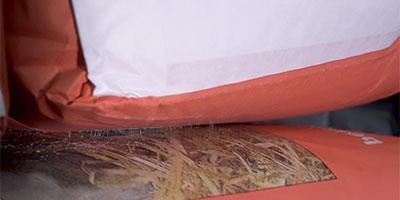
By applying non-contact hot melt glue, Robatech’s AntiSlip Gluing allows the palletized bags to be stabilized in a practical and reliable way, making the use of plastic film superfluous. UFA AG, a convinced user of the system since 2008, has also adopted it in the new bagging plant purchased in 2018.
Even at the end of the line, manufacturers are looking for alternative solutions to the use of plastic. But how can we reduce the use of shrink film without compromising the efficiency and safety transport packaging processes?
A successful example is offered by the collaboration between Robatech and UFA AG, the Swiss manufacturer of compound feed, mineral salts and milk powder, which, in 2008, opted for the innovative and and cost-effective solution for pallet stabilization using AntiSlip Gluing hot glue.
After 10 years, the company has reconfirmed the choice of the Robatech system, deemed sustainable and advantageous, adopting it in the new bagging plant purchased in the special feed factory at Sursee.
Recognized benefits
As explained by Urs Steiner, UFA Sursee production manager, compared to traditional systems with heat shrinking, the choice of palletizing with hot glue has several advantages: less waste of resources, narrower workspaces and competitive material costs. «Not to mention the benefit for our customers who, in addition to the feed bags, are no longer forced to dispose of the plastic film as well: calculating an average consumption of 25,000 pallets, it means over 2 tons / year “.
UFA AG is also satisfied with the degree of automation achieved with the Robatech system: «In general, our philosophy is not to look for the cheapest solution, but the most reliable and advantageous one» said Steiner, who specifies: «Given the large number of our systems, which must operate with the least possible number of interruptions, thanks to Robatech we have been able to eliminate unscheduled downtime. And the rare times in which a problem has arisen, however never serious, the technical assistance has been efficient and timely».
The project specifications
Eco-friendly stabilization. 500 bags of feed per hour are filled, sewn and labeled in the new UFA AG bagging facility. For the subsequent palletizing, two AX-Diamond contactless spray guns apply four hot melt spirals on the surface of each bag that passes on the belt. After that, a robot stacks layers of three sacks each on the pallet. Once two layers are stacked, a lift moves the pallet upwards and briefly presses the sacks against a press plate. This increases the adhesion between the layers, and the finished palletized stack can then be transported safely. Each layer is pressed, with the product counter of the Robatech application system ensuring that the last three sacks remain without adhesive application.
The palletised stack can therefore be transported safely. The quality of the bonding also ensures that the bags reach the customer without damage or tearing, facilitating the depalletization operations... a fundamental requirement for UFA AG customers.
A modular solution for easy retrofit
«The new bagging system has allowed us to increase the layers from eight to ten, achieving significant logistical advantages. However, to this end, we had to not only modify our gravity shelving, but also rethink the adhesive application process. In fact, having increased the load of each pallet to ten layers, it was necessary to ensure greater stability, but thanks to the modular structure of the Robatech products, retrofitting did not pose any problems» says Steiner.
«To this must be added that, with the CoolTouch insulation with which the spray guns of the Diamond series are equipped, the danger of burns has been eliminated and the energy efficiency is much improved, since the insulated applicator guns maintain a constant temperature. In short, AntiSlip Gluing has guaranteed advantages for everyone: to us, to our customers and to the environment».