Virtual event, real innovation

During B&R Industrial Automation’s Innovations Day 2021 we were catapulted into an artfully created virtual world, with spaces designed to encourage interaction between people and present many highly concrete technological innovations, starting from the ACOPOS 6D system, up to mechatronic solutions, robotics, to motion controls, advanced software functions...
Maurizio Cacciamani
Nicoletta Ghironi, B&R’s Marketing & Communication head Southern Europe, talks at length about the advanced machine and factory automation solutions presented during the online digital event Innovations Day on April 8th, focusing on the most recent and, in many ways, groundbreaking product: the ACOPOS 6D handling system.
«Nowadays the manufacturing industry is called to produce small batches, with frequent design and size changes from one product to another» Ghironi starts out, who points out that the rigid traditional handling systems, designed for large sequential productions no longer suit the case. «That’s why B&R, in order to solve these problems, has in its catalog the track family, flexible and fast conveyor systems that until yesterday included ACOPOStrak and SuperTrak, and that today has been expanded with ACOPOS 6D».
ACOPOS 6D: from line to space
But how does this new handling system differ from other B&R products? «Rather than differences - explains the manager - we should talk about two systems that can be used in different situations. The main difference lies in the movement: ACOPOStrak and SuperTrak move on a line, albeit an articulated one, while ACOPOS 6D moves in space. Both are magnetically propelled, but in ACOPOS 6D the shuttles remain completely suspended above the segments that make up the electromagnetic motor. The system is very flexible, as the combination of the various active segments (240 x 240 mm) enable the creation of “ad hoc” tracks in space thanks to the six degrees of freedom (hence the acronym 6D), which are fully controlled.
The range of shuttles, which can be combined, includes 10 models with dimensions varying from 120x120x10 mm to 450x450x16 with a load capacity from 0.6 to 14 kg; the maximum speed is 2 m/s. The shuttles are intelligent and each one is globally assigned a unique ID for position management at all times».
Flexibility and simplicity aboveall. The system’s strongpoint, Ghironi explains, «is its flexibility in terms of programming, routes, processing sequences and the level of protection of the structure (stainless steel or plastic material). The system, which is easy to wire and configure, simultaneously controls four shuttles on the same motorized segment. Each shuttle can also carry out weighing operations with high precision, thus totally eliminating the weighing stations, for which significant space savings can be achieved, making machines more compact».
Maintenance operations are also reduced to a minimum, as the shuttles float freely without contact or friction, thus eliminating problems related to wear and tear.
«The high degree of protection - up to IP69K - also makes them ideal for use in areas where hygiene is essential, such as food & beverage. I would like to underline - points out engineer Ghironi - that the integration of ACOPOS 6D in the B&R ecosystem makes it possible to synchronize, with microsecond precision, the shuttles with servo-axes, robots, track systems and vision systems. A dedicated controller, connected to the machine network via POWERLINK, plans the optimal path, avoiding collisions and minimizing energy consumption. For systems with more than 200 segments or 50 shuttles, multiple controllers can be synchronized with each other. At startup, the controller immediately locates each shuttle on the engine segments, and production can begin without further operator intervention».
IT - OT integration, even with the PLC
The digital event Innovations Day 2021 made it possible to reiterate the criteria that guide B&R in designing and proposing industrial automation systems that look to the future and simplify users’ operations.
Here Ghironi is assertive: «In B&R’s vision we need - and we are already working in this direction - to take a further step towards integration between the IT and OT worlds, making it possible to use any code created on the Linux operating system, written with any programming language, such as Eclipse or Visual Studio or C++, Python, JavaScript in B&R control systems… So, for example, you can run a Linux Tensorflow ML (Machine Learning) model on an Automation PC, receiving machine data from an X20 series PLC via an API, exploiting existing codes to optimize maintenance».
«In the live demo performed by our engineers during the event - Ghironi continues - we show how easy and fast it is to load a Linux code written in Python and integrate it into the automation system. The most important advantage offered by this solution is that, regardless of the language that the engineers use to develop new applications in the future, for example deep learning or block chain applications, you can simply use the algorithms that will be available in the future in the B&R systems».
Advanced and native functionality
Reality dictates that automation systems are not and can no longer be single, isolated entities, but must be connected starting from the sensor to the cloud, so that information is made available where it is needed, without barriers and/or interruptions.
«B&R’s goal is to enable fast, secure and easy-to-configure communication, based on standard protocols such as OPC UA and OPC UA on TSN and the use of advanced and secure features implemented natively within our devices. The choice of using standard protocols offers the manufacturer the great advantage of being independent from the supplier».
Motors with integrated drives. B&R has introduced new, sophisticated models of mechatronic units with powers up to 0.35 kW that are very compact and characterized by a high power density and a remarkable cycle time (50 microseconds) onto the market. «It should be emphasized - Ghironi reiterates - that while occupying a very small space (the base is the size of a business card) we can count on the most sophisticated B&R motion control on board, which allows us to implement the advanced integrated safety functions.
The use of hybrid cable simplifies wiring as well as the addition of additional motors along the machine, with daisy chaining, drastically reducing the meters of cable to be carried along the machine. Wiring is also made easier by the presence of the swivel connector (up to 300°) so that cables, less prone to flexing or twisting, will last longer and are much more accessible to maintenance personnel. Finally, let’s not forget the reduced size of the control panel, since the drive is integrated in the motor».
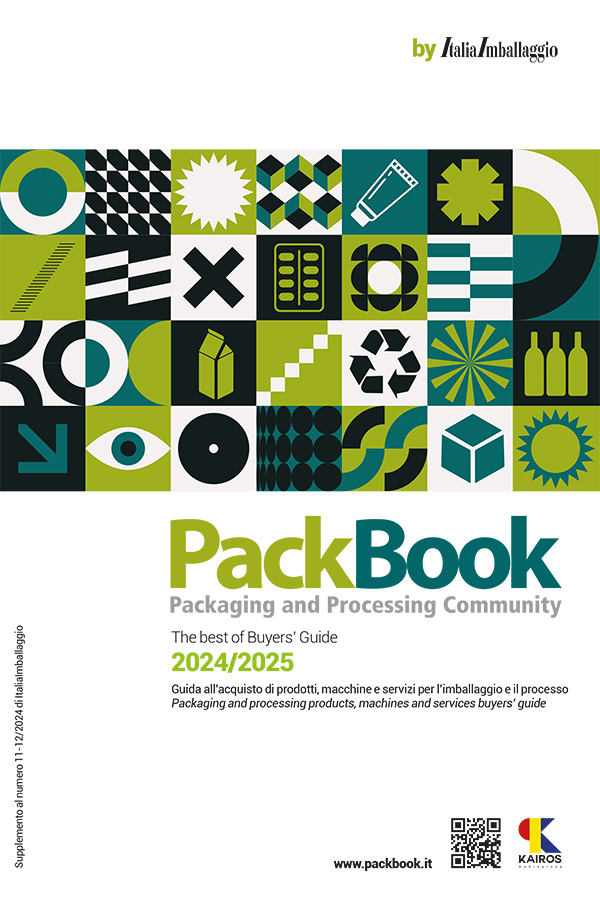