When heat matters

The difference is always in the details. In this case we are talking about cast-in aluminum heaters used in packaging machines, which guarantee superior durability, reliability, efficiency and safety. Interesting pluses for both machine manufacturers and end-users. This “alternative” solution, proposed by Amarc, can be evaluated at its best after a test “in the field”, or by asking the company for a free sample.
So, why not give it a try? by Stefano Lavorini
Cast aluminum or bronze heating elements are a component of the hot part of forming - filling - closing (HFFS and VFFS) and thermoforming machines. Produced by Amarc, according to the men of the company based in Montevecchia (LC), they represent an advantageous choice compared to the traditional electric heater, used on thermoforming and tray sealers, as well as sealing of plastic films.
Data in hand show that plates with embedded armoured heaters offer excellent electrical insulation - even in harsh conditions - and uniform temperature over the entire surface, with the added advantage of a single electrical connection, regardless of size.
They also allow a significant reduction in power consumption (-30%) and, thanks to the high mechanical properties and resistance to corrosion, ensure a longer life than other technologies, resulting in a drastic reduction of technical maintenance.
Among other things, in Amarc, they are so convinced of the validity of the product that they offer a 3-year warranty on the electrical part.
A valuable component
«Cast-in heaters produced by Amarc are the result of decades of experience in designing and manufacturing products and solutions for heating and transforming materials in industrial processes: in particular, hot chambers for heating drums and containers, as well as industrial ovens for multiple applications» Giorgio Ardesi, who with his cousin Andrea, runs the family business founded by their grandfather, tells me.
«All our products are characterized by high engineering and technology and are designed to ensure ease of use, high thermal efficiency, and maximum functional safety.
In the case of the cast-in heaters, in which the heating element is “submerged” in the material, the main feature is that there is no thermal exchange with the air, which ensures a longer lifespan, that is, a drastic reduction in machine downtime - whether thermoformers, tray seal or flowpack - as well as significant energy savings.
But that’s not all. A single heating element, which safely exchanges heat inside the aluminium casting, offers the advantage of having only one electrical connection, thus simplifying maintenance, as well as guaranteeing temperature uniformity over time even on large plates».
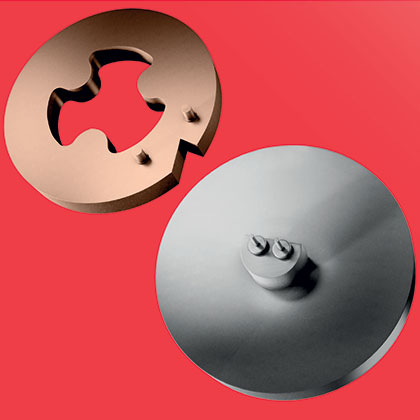
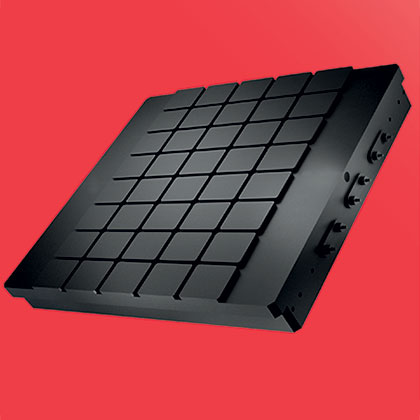
To each his own
Amarc manufactures cast heating plates according to customer specifications, shaping and machining them with CNC machines; these plates can reach temperatures of over 300 °C and can be prepared for electrical connections in housing with IP55 and IP65 protection.
In the case, for example, of HFFS (flow-pack) machines, cast-in heaters have been developed for cross sealing of the packaging film.
As the technical manager, Umberto Riboldi, points out «in this case, too, we use our ability and experience to define, in collaboration with the customer, the most suitable characteristics of the product. We intervene, for example, on the characteristics of the aluminum alloy, on the type of casting, on surface treatments to improve non-stick and smoothness or reduce abrasion.
For decades we have been partners with a leading global company, with thousands of installations worldwide, and we have not encountered any problems with weld sealing with any type of plastic material, including the new biodegradable polymers or those from renewable sources».
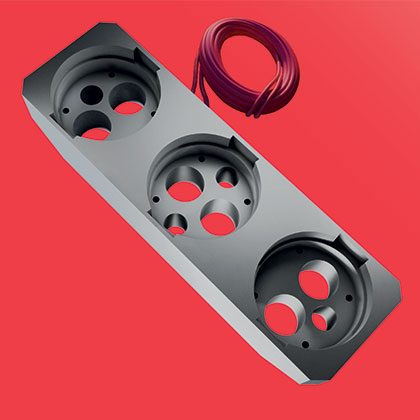
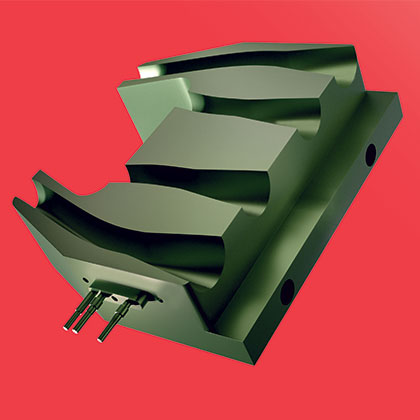
From words to facts
Therefore, sealing systems are an essential component: if they do not work properly, production is not possible.
For this reason, Amarc is a company that has always shown a keen eye to product and process improvement, with an ISO 9001:2008 certified quality system.
Andrea Ardesi is clear on the subject: «We are a customer-oriented company, which means, for example, that we do not have a catalogue but our technical office works alongside the customer to choose the most suitable solution for each individual application.
As far as heating plates are concerned - he continues - we well understand that machine manufacturers may be reluctant to experiment with new solutions, and therefore, precisely for this reason, we are committed to providing, to those who request it, a free sample to make a test and an initial assessment.
In addition, the passion and care we put into our work allows us to ensure extremely short delivery times of the electric casting plates, even only 3 working days, as well as a guarantee a three year warranty on the electrical parts».
Summing up, it seems that there are concrete reasons to learn more about and test out this alternative technology, which seems to be able to offer concrete advantages to machine manufacturers and users.
The choice is yours.