Machines for innovative packaging
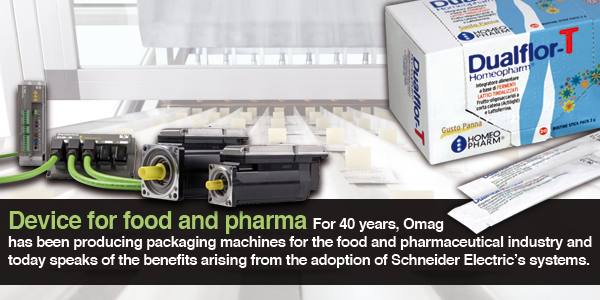
Kraft, Nestlè, Ferrero, Unilever, Bayer, Novartis are just some of the customers, that in over 100 countries around the world, every day use Omag packaging machines. Since 1975, the company, based at Gabice Mare (PU), has been designing and producing sachet filling machines, dispensers and screw conveyors for the food-, pharmaceutical-, cosmetic and nutritional industries. And today speaks of the benefits arising from the adoption of Schneider Electric’s systems.
«Our output includes a wide range of vertical and horizontal, continuous motion and intermittent packaging machines» Omag Sales Director Ingegner Giovanni Nocita states. «Among these, the C3 series for packaging products in sachets heatsealed on all 4 sides, the CO series for packaging products in doy-pack style or stand-up sachets heatsealed on 3 and/or 4 sides, the CS and Diva series for packaging products in stickpacks, and also machines for strips and single pieces. The range is completed by the "queens" of Omag’s range, Pharmasachet and Pharmastick, customised for the pharmaceutical industry».
We immediately reveal one of Omag’s secrets: the absence of a true and proper catalogue of standard products. Omag’s Automation & System Manager Roberto Filippucci explains why. «Even though our machines are designed starting from a common base, recognizable in their principle of functioning, each machine is always made taking into account the specific needs of each customer. According to the demands of the same, we hence develop an ad hoc solution that is ends up being one of a kind. In our technical department, a team of design engineers works full time to respond to these customization needs».
Primary packaging
In around 40 years Omag has faced every kind of problem regarding primary packaging. «We have come into contact with all types of product, aboveall in powder form, that needs to be packed and closed» Omag Technical Manager Davide Santi explains. «After our initial experiences in the food field, we slowly gravitated to the nutritional parapharmaceutical sector, where our added value has made the difference, especially in recent years, that is when the pharmaceutical market began demanding evermore customized machines also capable of packaging more than one type of product. Bolstered by the experience we built up in the food industry, characterized by highly variable demands, we hence entered the pharmaceutical industry without hesitation, because the capacity to respond to specific needs had become our daily fare».
Omag approached the pharmaceutical sector with innovative solutions, to the point of filing for an important patent regarding metering systems. This patent enables the metering of both powdery and free-flowing products, including mixtures. The success enjoyed in the pharmaceutical market has even allowed Omag to attain positive results in the years of crisis and to "rediscover" the Italian market. «If at first we didn’t pay much attention to the domestic market – Santi continues - in recent years we have changed our tack somewhat, attaining great results. And we have found that, on a technical level, the Italian market is very challenging: it’s a matter of dealing with competent people who speak the same language we do and who demand high standards». For the Italian market, for example, we have created complete lines with the use of robots.
«Indeed it was the Italian market that has prompted us to use highly advanced technology - Santi continues - which at the same time, led us to revamp the “cladding” of our machines, no longer worthy of their motor. Hence we modified the design, adopting pharmaceutical industry standards, making the machines more accessible, easier to sanitize, with fewer external cables and so on».
Another decisive aspect derived from the redesign of Omag’s machines is the reduction of energy consumption. «We have been able to make the machines more compact, a feature appreciated not only by the pharmaceutical market and – Santi adds - thanks to Schneider Electric’s PacDrive, we have optimized their size, especially through the use of motors with integrated electronics».
The year 2007 witnessed the marriage between Omag and Elau (subsequently bought up by the Schneider Electric Group). «We had already been acquainted with Elau for some years, but we still didn’t have sturdier enough shoulders to follow their philosophy, because the basic preparation of our electronic engineers was in PLC» Santi states. «Ingegner Filippucci’s joining the company (who took over from his father after an important work experience in a multinational company) turned out to be the driving force behind the change at Omag, also because at that point we had all the skills needed to proceed with our plan. It is worthy of note, however, that our development has never occurred to the detriment of choices made in the past: even today we are still willing to examine any type of problem our customers might have and to question our choices. This philosophy has been rewarding and time is proving us right».
A successful partnership
Why did Omag chose PacDrive products? «We analysed the competitors present on the market and their products. At the time, in addition to Elau, now part of Schneider Electric, there was only one other supplier who proposed the motor with integrated drive», Ingegner Filippucci intervenes. «We liked their solution, because our machines had two control panels: one dedicated to drives and one dedicated to the control part. Two panels, in terms of wiring and space, were beginning to be a bit challenging though; we then directed towards the motor technology with integrated drive, that I had already been able to appreciate. Then there was the advantage, not indifferent, of being able to use multiple feature software libraries that have simplified writing of software for our machines. Furthermore, the excellent relations struck up on the business and technical level with the producer left us with no doubt, and we made our choice».
With the PacDrive solution, Omag started from the heart of the machine, or that is the controller and the motion system. «After Elau’s incorporation into Schneider Electric we began to use many other products from the same supplier, which we got to know and integrate, starting from the inverter (ATV312). Today, in particular, we use the PacDriveM motion system, but we are already trying out PacDrive3».
As Ingegner Lorenzo Degli Esposti, Schneider Electric Sales Manager, states: «The PacDrive motion control system can give excellent results. With our technical support and months of study, programming and testing we reached our objective. Omag placed great faith in us, which we are committed to maintaining in terms of service expectations and product development. Because our product has to evolve with Omag’s machines; and if a product is to be performant and reliable, the technical service behind the product (design, delivery times, service, etc.) especially in the food and pharmaceutical field, has to be very high level.
Degli Esposti goes on to highlight that introducing products under contract on a machine not only requires a technical endorsement but also an economic analysis. In fact, alongside the heart of the machine, where a given choice and a given solution of a mainly technical character are decisive, there are components where the economic aspect also plays an important role. «Our goal is always to work in partnership, and hence in harmony with the customer, proposing the entire Schneider Electric offer. All the same, the advantage of the choice of a sole supplier must always match with the benefit of the customer to integrate quality devices, at the right price and harmoniously integrated with pre-existing devices».
The evaluation of TM5 I/Os subsequently connectable on the SERCOS III communication bus was also important, that with a view to passing on to PacDrive3 architecture, would enable the further integration of the automation solution on Omag’s machines. «When you change a fundamental part of the machine (in this case going over to the PacDrive3 system) one is right in looking ahead to try to grasp the challenges and the opportunities the market presents - Filippucci intervenes - and at the same time, we also need look ahead from a technological point of view; farsightedness has always been one of Omag’s features; indeed the company is already testing the motors with the ILM integrated drive of the PacDrive3 Motion Control system. The transfer from PacDriveM to PacDrive3 system is only possible because the same reliability and the same tried and tested software are also ensured with the new technology, that offers considerable pluspoints like communication on Sercos III».
Integrated automation and energy saving
«The decision to introduce PacDrive technology on our machines – states lngegner Nocita - met with some difficulties early on, concerning the fact that our end users demanded machine automation solely run by PLC. The prospect of abandoning PLC for a product that "does something more and differently" may initially appear daunting, though users soon come to appreciate the added value that the latest generation devices bring to machines with a high technology content. Today the concept of the drive integrated in the brushless motor is much approved of, as well as the possibility of changing the servomotor with a simple plug, not to mention of the reduction of the components in stock, with only one type of motor that is programmed directly on the machine».
«Often the value and advantages of this new technology are not perceived at an early stage, until people have seen for themselves» Ingegner Filippucci agrees. «The first benefits that are normally appreciated by the customer are the most visible, namely the reduction in bulk and cleaner design of the machine. Another important aspect is the energy saving, not to mention the possibility of remote diagnosis and support. With regard to energy saving, it is implemented primarily at the machine hardware level, for example by connecting all the engines on the same bus in order to allow the exchange of energy between the motors themselves and allow the storage of energy in the power supply unit. There is also a machine motion planning and optimization phase via the motion profile software management, trying to implement the most linked profiles, compatible with the machine’s functioning. On average, with the system operating for 8 hours, we rate that an estimated energy saving of around 20% is attained.
Being able to connect the movements harmoniously and with curves and not limited to the trapezoidal profile (typical of asynchronous motors) a management of the mechanics and the electric motor has been obtained which has led to energy saving, less wear on moving parts and less mechanical stress on the machine. Thus maintenance operations are fewer and far between, the mechanical organs, previously often oversized to absorb vibrations induced by the motor, can be more correctly dimensioned. All things considered, a longer machine lifespan is obtained»
«Indeed for Schneider the issue of energy saving is very important» states Degli Esposti. «In fact we have a deep expertise in energy management, in all possible forms: from the photovoltaic to the cabins, a subject much broached by end users».
In the packaging sector, Schneider Electric provides tools (such as the ECAM software) and specific services to already estimate and optimize the machine’s energy consumption in the design phase. These results are then subsequently compared with actual consumption data recorded while the machine is running in the various production stages to evaluate the possibility of yet further energy saving.
«And when we come across concerns like Omag that are youthful, dynamic, receptive, aiming at constant improvement, we manage to propose these concepts» emphasizes Degli Esposti. Something that is confirmed by Ingegner Nocita: «We willingly take risks if we believe that a given solution is actually the optimum one. The PacDrive system and Schneider Electric provides us with the right kind of drive and collaborative support, enabling us to reach new markets that would otherwise be inaccessible to us».
Yet other advantages
Another advantage obtained with the adoption of Schneider Electric’s PacDrive technology, according to Nocita, derives «from the use of servo motors with integrated drive that enable a reduction in the size and the overall bulk of the system because due to the reduction in the number of machine components. And yet again, this choice enables the standardisation of the machine motors; hence the customer only needs to have two different spare parts in storage, which also affects the post-sale phase, because the maintenance operations carried out by customer, but aboveall the number of spare parts, can be significantly reduce. Since it began using this technology, Omag’s demand for spare parts has dropped considerably, due to the very fact that maintenance is much more efficient, and the number of components is reduced, the mechanics having been largely replaced by electronics (no more clutches, chains and so on)».
«Optimizing the sizes of the motors has entailed a considerable amount of engineering design work», Filippucci points out. «Overhauling a mechanical engineering design project to reduce the number of different types of motors was only possible with the collaboration between Omag’s electronic and mechanical engineering department and Schneider Electric’s PacDrive technical support service. This is born witness to by the study made on the machines, that are increasingly customized. And it is this that creates the added value, in addition to reliability and performance of the machine».
Examples for today and plans for tomorrow
Pharmasachet and Pharmastick are cornerstones of Omag’s product offer both for the technological solutions adopted and for the success they are having on the market.
Pharmasachet and Pharmastick are machines designed for the pharmaceutical industry, devised for producing sachets or stickpacks sealed on four sides.
In particular, the stick packaging machine, now very much in demand on the pharmaceutical market for packaging powders, is equipped with a metering screw patented by Omag, which facilitates the packaging of not very smooth-flowing powders. «We are talking about a vertical intermittent motion machine for stickpack style sachets» Nocita explains. «The stickpack started by satisfying a large demand in the food market and is now entering the pharmaceutical market to an increasing extent. Compared to the sealed sachet, the stickpack saves around 15-20% of wrapping material while packaging the same dose».
Packaging with the stickpack requires very accurate equipment. In the case of a metering screw, for example the screw powered by a PacDrive iSH servomotor with integrated drive, must be worked full and to high accuracy. At the same time, the servomotor enables the management of all the different metering screw parameters in order to dose products with a very narrow tolerance. This is especially crucial in the pharmaceutical field, where products are very expensive and the legislation very strict.
«In the management of powders, various processes often come into play, and not all manufacturers have the resources to ensure the right consistency of flow of the formulation» adds Nocita. «Where it is not possible to work the powders in a granulator, they derive from the direct mixing of the ingredients and the resulting mixture may not be that smooth-flowing. In this case highly specialized metering screws need to be used so as to ensure the required accuracy. Omag’s patented system, which works on the principle of depressurisation, together with the metering screw operated by a PacDrive iSH servomotor, ensures the high performance of the machine as well as precision metering regardless how smooth-flowing the product is. Used with different qualities of primary product the same machine always operates ensuring the desired results with the expected speed performance».
The strength of this Omag patent lies in being able to pack a high variety of powder products with different flow rates using the same machine. To the intelligence of Omag and the people who developed it, the Schneider Electric PacDrive system adds the ability to handle the system with the precision of its servo motors, so that the metering screw moves exactly as expected. «A price had to be paid for accuracy in terms of building the motor, the type of drive and encoder" emphasizes Degli Esposti. «We also set up a partnership with Omag to deal with the economic positioning of the products, for markets requiring high performance while having downward price trends». lngegner Nocita agrees: "Pharmasachet and Pharmastick, but products our for the food market as well stand out both for their quality and their price. And their competitiveness was undoubtedly helped by the partnership established with Elau beforehand and with Schneider Electric subsequent to that, since the PacDrive solution constitutes most of the electronics used on the machine».
Future plans - Omag has already developed the prototype of a new machine that will be used to test the new PacDrive3 Motion Control technology which is based on the SERCOS III motion bus. This technology not only enables increased performance but also greater ease of use for the developers, thanks to a new SoMachineMotion software development environment. The new communication bus will not only be used for motion data transmission, but also for capturing signals from the field.
«All our previous work allowed us in 2011 to consolidate our leadership position in the nutritional market in Italy, particularly in the food energy integrator segment» concludes Nocita. «We can indeed say that all companies operating in this market in Italy have Omag machines. Our objective is to expand this domain to the rest of the world. Today, in addition to maintaining our leadership in the Russian market, where we have been operating since 1985, we are devoting time and energy to operating in other markets such as India, China, Brazil or the United States. Countries, therefore, where competition is high, but the results encourage us to persevere. At the same time, we will shortly be adding another production facility of about 4000 square meters to the current 2000 square meter facility, thus increasing production capacity and doubling the forces we will field to conquer these new markets. New offices, a new showroom and a new high-tech factory will also be available, which will allow us to develop every single piece of machinery in-house. Indeed, with the exception of the commercial Omag, is already capable of building all the piece of its machinery itself. This is important in order to ensure an appropriate response to customers who need simple machines or spare parts quickly».
Omag presented the full range of its machines at Ipack-Ima (Milan, 28th February-3rd March 2012), obtaining excellent results.