Circular economy and resource conservation with ultrasonic sealing
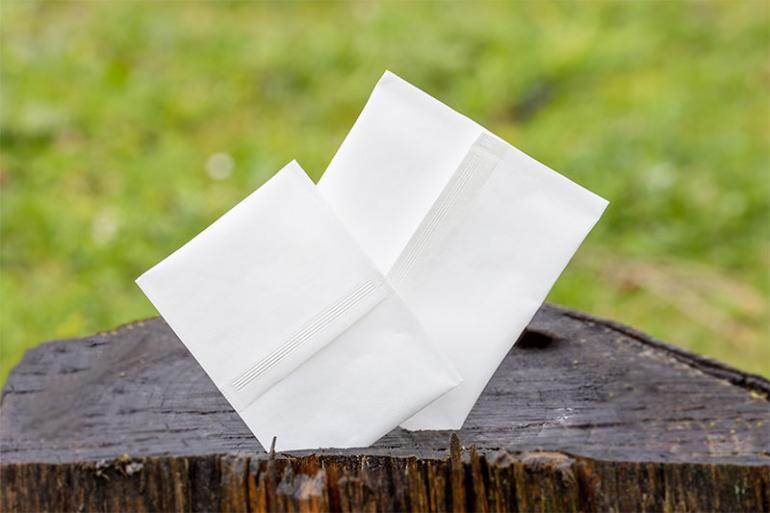
A growing number of companies in the food sector choose to make their packaging with monomaterials and paper compounds to facilitate recycling at the end of its life. These options, aimed at improving the sustainability of the packaging, however, raise some critical issues during sealing, which can be easily solved thanks to Herrmann Ultraschall’s technology.
The varietal purity of packaging is an increasingly widespread construction feature, which is part of the strategies put in place on a large scale to increase the recycling rates of packaging, an objective pursued by many large companies in the food sector, and not only, committed to improving the sustainability of their products. This means that films - to cite one of the most significant examples - must be composed of one or more layers of a single material, instead of different plastic materials.
This monomaterial structure, however, determines criticality in the welding process, which is difficult to solve with conventional procedures such as induction and thermal contact. The first technique, in fact, does not work without aluminium, while the second is very difficult to implement for paper compounds, due to the insulating effect of the cellulosic material.
On the other hand,the advantages of ultrasonic sealing are very beneficial to the current trend towards mono-material packaging. Ultrasonics only generate thermal energy inside the seal area. The support layer is not melted, even though it is made of the same material. This means the amount of energy introduced can be defined very precisely, which is a huge advantage for mono-materials with a tendency to have a smaller process window.
Tighter process limits can be maintained
Robert Hueber, Packaging Business Unit Director at Herrmann Ultraschall: «Ultrasonic technology can also deliver good sealing results with narrow process limits, especially with regard to tightness and visual appearance. The thermal expansion is kept to a minimum. Heat sealing processes can demonstrate disadvantages of excessive heat input, especially in the high-speed welding of film webs made of mono-materials. This can lead to the uncontrolled elongation of the film web and therefore impair the process».
Mono-materials are also more susceptible to film shrinkage due to mechanically and thermally less stable support layers. The sealing seam appearance can suffer and adhesion is possible. Ultrasonic sealing can counteract due to the cold tools. This in turn has a positive effect on downtimes and the need for wear materials such as high-temperature Teflon tapes. Ultrasonics only need energy during the sealing time, so no high stand-by consumption is necessary as with other thermal sealing processes. The tools are immediately ready for use without having to heat up - another contribution to reducing the burden on the environment.
The advantage of producing heat only inside the junction
Ultrasonic sealing has become a real alternative to heat sealing for various applications such as wet food containing proteins and sugary drinks in pouches, as well as salad and powdery products. The difference to conventional sealing using thermal jaws is the way the heat is generated. While in the case of thermal sealing jaws the heat comes from the outside and therefore also heats up and can affect the support layer, in ultrasonic sealing the heat is generated by the ultrasonic vibrations inside the sealing layer. It ensures that the sealing layers bond together at a molecular level before there is any undesirable heat conduction through the entire packaging material. As a result, the packaging can be closed much more gently for the type of packaging and feed material. Shrinkage and possible leakage are minimized.
New Zipper Sealing Module: sealing zippers sustainably
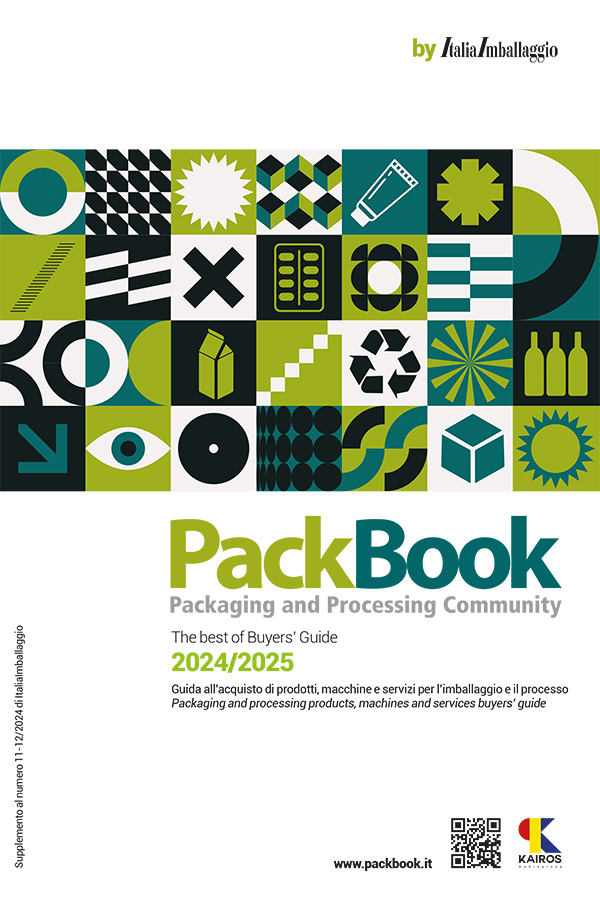