Laminati Cavanna: lamination innovation for 55 years
From the recent Academy to attention towards circularity, from new technological investments to staff training, ItaliaImballaggio has met the chairwoman for an overview of the company
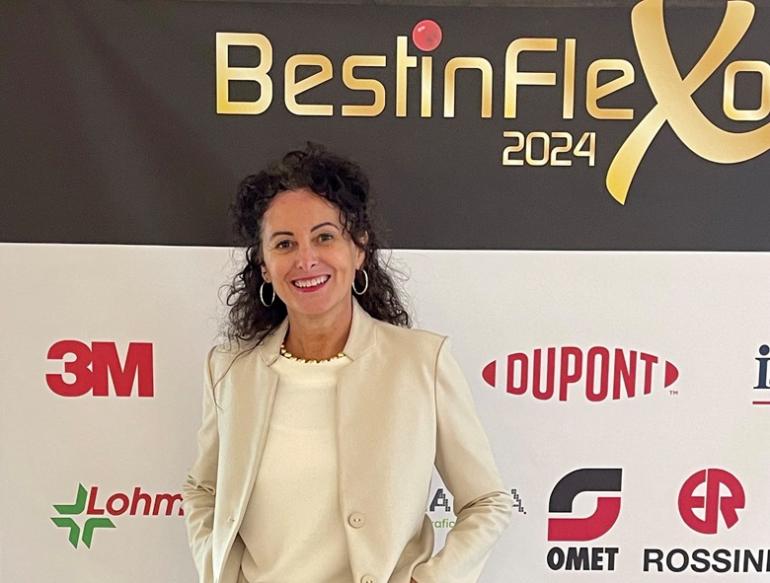
Laminati Cavanna, the leading Italian contractor specialised in the lamination of plastic film, renews its commitment, focusing on digitalisation, staff training and technological updating, aiming at one single objective: to offer customers an increasingly efficient service. Anna Paola Cavanna, second-generation chairwoman of the company, which in 2024 celebrated 55 years of business activity, tells us more about this.
«In the last five years we have invested over 10% of our turnover in new technologies», Anna Paola Cavanna begins. «New developments include the decision to renew machinery from an industry 4.0 point of view, with an enormous effort in back-end interconnection, which today also includes a technical office with staff specifically trained to use the new digital tools. Personnel control the information coming from sensors distributed throughout the company from remote, collecting data, including those regarding the ethyl acetate recovery plant, and sending them to the MES. We are therefore able to verify the proper functioning of all the parts of the plant: regeneration, distillery and the tank showing how much ethyl acetate has been produced: in other words, we closely follow the operations of the plant».
An authentic renewable cycle
The plant, opened in October 2023, allows Laminati Cavanna to recover 1500 litres per day of ethyl acetate, the equivalent of a tank and a half, which was previously purchased to cover the need for 300 tonnes of the substance for production. «By recovering the solvent, we reduce pollution and emissions», Cavanna comments. «We distil it, drain it and put it back into production, reducing our carbon footprint and any surplus. The system allows for monitoring from remote through the use of company devices and from the already-mentioned internal control room: it’s possible to control general activity, monitor performances and visualise alarms from both channels».
Automated order management
The same industrial process automation logic is applied to production orders, which activate a series of paths closely monitored by the technical office, under the coordination of the general manager Carlo Fornaroli and the production manager Ivan Lucev. «When the customer sends an order with the specifications», Anna Paola Cavanna continues, «we generate automatically an internal WO with an efficient flow that includes labels, controls, analyses to be performed and documents both in digital and on paper (the medium serving as a backup). The staff involved in the creation of the WO complete and schedule the orders for the different work centres on the basis also of customer requests and delivery times. It’s a codified process that guarantees constant control of information, traceability and quality in every phase of the production process. In recent years, the challenge that a contractor has to face is that of knowing how to integrate the information flow of its customers, guaranteeing information continuity and being available and flexible in the acquisition and management of third-party documentation and registration methods».
Technological innovation as a key to growth
The machinery fleet is constantly upgraded, with reconfigurations of the lines, specialisation in markets and sectors, also different from traditional flexible packaging ones, and the acquisition of cutting-edge technology for solvent-based, non-solvent based and water-based double and triple lamination, so as to guarantee maximum technological flexibility, aiming also at guaranteeing the most up-do-date safety standards for workers.
«In reorganising the company layout, we have decided to replace a number of lines, working with important partners such as Nord Meccanica and Bobst», Cavanna continues. «We have chosen laminating and lacquering machines, excluding the printing phases, to focus on the laminating service, which has always been our specialisation. The choice of two identical BOBST plants is aimed at guaranteeing customers business continuity, to simplify maintenance work and to improve the efficiency of training courses for operators. Operators thus become “interchangeable” and the teams can be composed according to contingent needs. Looking at segments other than food, the pharmaceutical and pet sectors are increasingly significant and we have opened up to new sectors such as the production of electrical cables, for optical fibre, solar panels, electrical insulators, components for transformers, credit cards, bows and decorative paper and recently also furniture coverings».
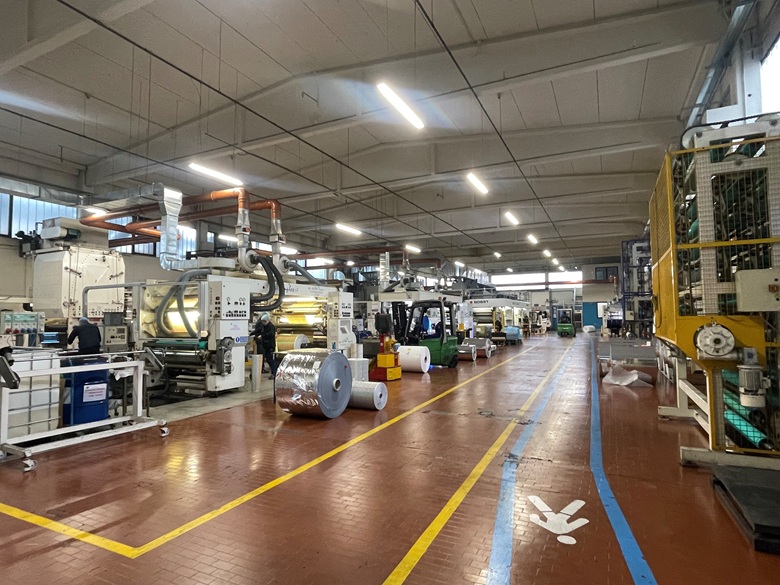
Laminati Cavanna’s choice, is, in fact, to diversify activities and sectors, in this way protecting the company from increasingly frequent and violent market fluctuations. «We have chosen to dedicate lines to only food, pharma and cosmetics, for which there needs to be particular attentions towards hygiene and protection against contamination. We can, therefore, carry out production campaigns where thicknesses, pitches and types of coating (flexographic or rotogravure) change, but not the end use of the product. A compact solventless line is dedicated to the constantly-growing dry pet food sector. There are also water-based productions, with compostable and biodegradable material, and barrier or heat-sealing coating applications on different supports».
There is also great attention towards line inspection systems, with significant economic investments and training, in order to ensure a product of quality. «We have IR Synaptic G-SCAN scanners that constantly scan the strips of film, controlling the quantity, type and uniformity of the chemical applied throughout the strip. All the cutting lines are equipped with mono and bifocal FUTEC video cameras so as to allow us to remove any contaminations, printing or lamination defects and continuously control the quality of the printing and the cut spacing. This technology is also used to carry out remediation activities, at the request of customers, of lots complained about due to the presence of specific defects».
Quality under control
Among company departments, the Quality office has a key role aimed at ensuring constant control along the entire production chain with continuous sampling and analysis regarding which the chairwoman points out: «Our Quality area’s controls start from receipt of the raw materials and continue through to the delivery of the finished product. For every production lot, Laminati Cavanna issues a test report indicating the mechanical performance and thermal resistance characteristics that the laminate has achieved. Each customer has specifications that the company makes its own, in order to ensure the requested quality and technical characteristics, providing all the related documentation guaranteeing the quality of the product and the maintenance of traceability».
Accessory services
«Cutting is also performed in the site, a process for which we have central drum or twin-shaft slitters, with the possibility of making cuts with high flexibility in terms of input and output strip thicknesses and diameters. All the cutting lines are equipped with mono or bifocal video cameras, enabling the removal of any contaminations and printing or lamination defects, continuously controlling printing quality and cut spacing. We carry out the grinding of rollers and rubberized cylinders for third parties using Rossini technology».
Market management and stability, the strength of partnerships with customers and partners
Market differentiation and continuous innovation combine with partnership relationships with customers that actively collaborate in the improvement of every phase of production. «Thanks to collaborative relationships with customers, we have a fairly long view of orders, also three weeks, and planning approach which allows us to optimise production and meet requests and variations. Coim, Henkel, Basf, Dow and Sun Chemical are only some of the names with which we work as suppliers, but with methods that are more similar to a strategic partnership, with sampling, industrial tests of new formulations and in general, shared commitment to reach ever-higher standards. With the same logic of exchange, these relations make it possible to bring together extraordinary professional skills in the Academy, guaranteeing a training path for our employees that have today reached 60 people working in two shifts, including Saturdays».
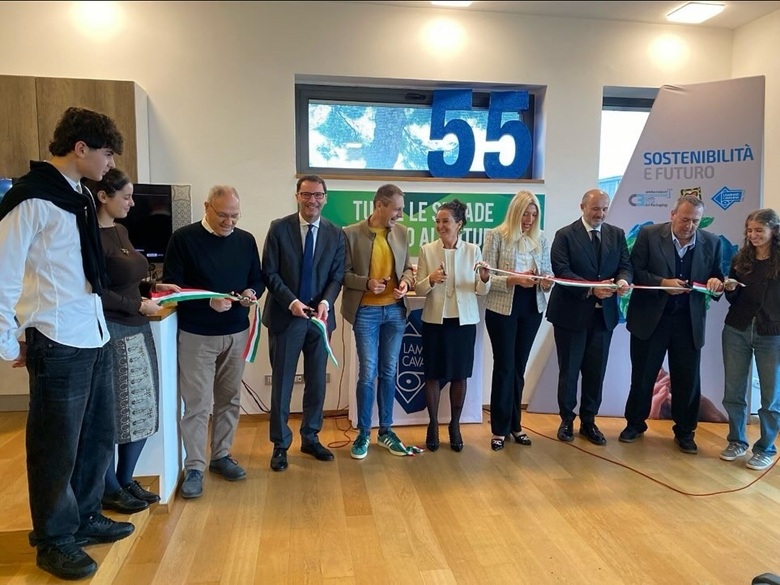
A training service that focuses on the new generations
Financed with calls for proposals organised by the Emilia-Romagna region, the Academy is a context for continuous training characterised by a physical space next to the company and by a digital platform designed to provide information in mobile form which, thanks to the use of AI, is also multi-lingual. This choice has been driven by the need to make communication methods suitable for the more recent generations. Videos, manuals, technical data sheets and certified hours of training are additional components of a project that also sees suppliers and customers specializing in adhesives, safety, packaging and IT, as key participants.
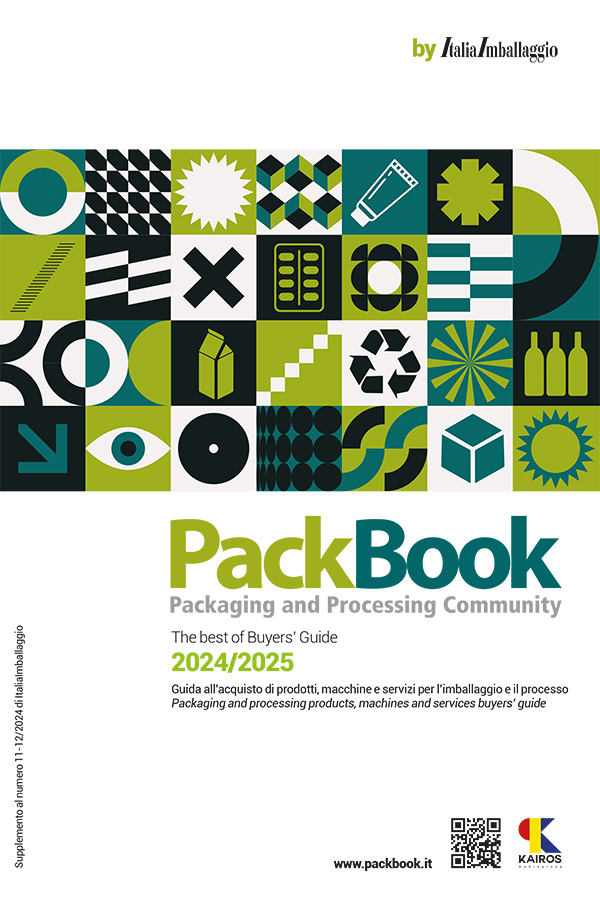