The digital approach to efficiency
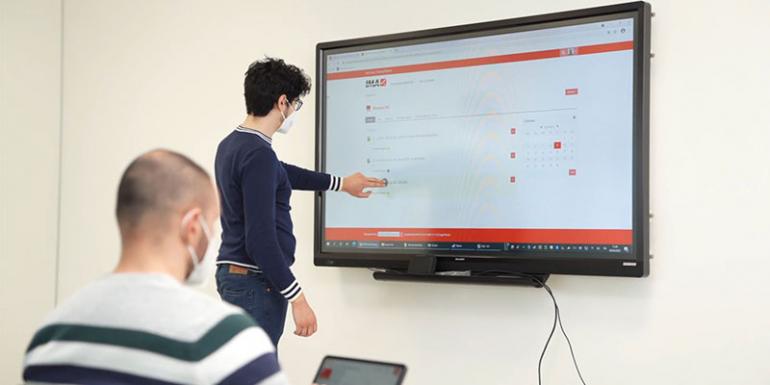
Digital training and services to enhance production activities and plant management: the initiatives of the IMA Group designed for the manufacturing world.
In an increasingly digital manufacturing world, the possibilities for optimizing and increasing efficiency are growing: new products and services can facilitate plant maintenance and management, speed up operations and increase the quality of the final product.And increasing line efficiency achievable with a digital approach is the policy that IMA Group has been pursuing for some time through the IMA Digital initiative, thanks to the wide range of digital products and services created specifically for the manufacturing world.
With IIOT on machines, secure connections and accurate reporting
For some time, the IMA Group (a world leader in the design and production of automatic machines for the processing and packaging of pharmaceutical, food and cosmetic products, as well as one of the largest players in the market of industrial automation and assembly systems) has been offering a wide portfolio of services related to the world of connected machines:
- A4gate, the integrated hardware and software solution to prevent external penetrations and cyber attacks able to cause potential damages and paralyze production;
- IMA Sentinel, the application for smartphones, tablets and desktops able to allow autonomous monitoring of production lines 24/7 wherever you are;
- IMA Control Room, the service that provides the customer with detailed reports on production progress, an alerting system able to prevent damages and malfunctions and a 24/7 first contact real-time service to report to experienced IMA personnel problems related to plants.
Last but not least, the most recent service that IMA has started to offer to its customers, related to IMA Artificial Intelligence, able to process the historical production data through Machine Learning algorithms to implement strategies aimed at increasing production efficiency.
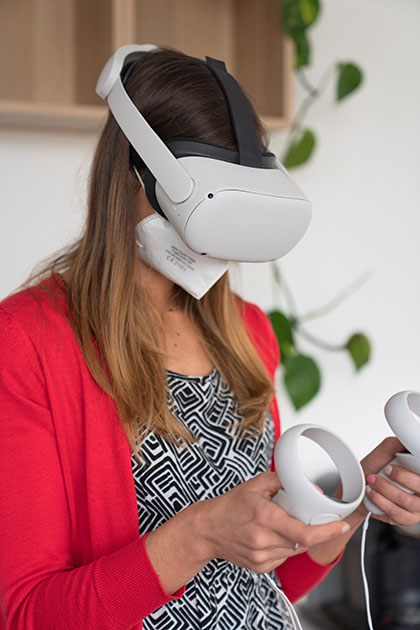
Ad hoc services and training
The products related to the world of connected machines are integrated with other services promoted by the Group in the Digital Training and Digital Services area. In fact, IMA is increasingly oriented towards guaranteeing its customers all the tools and platforms for completely independent plant management. Training plays a key role in achieving this goal, an activity that has prompted the Group to invest significant resources to meet different needs and requirements and offer its customers a training structured in various stages.
IMA Digital Classroom
IMA has created real traditional classrooms equipped with the most advanced technologies. In these environments, operators can count on the support of expert teachers and interactive Touch Monitors to practice with 3D models of machines, manipulate objects and carry out sequenced routine maintenance procedures. Tablet integration ensures that all class participants can manipulate and interact with the plant version on mobile devices as well.
Virtual Reality is perfect to guarantee a greater involvement during the Digital Classroom: with helmets and gloves able to provide physical feedback, the operators find themselves immersed in a completely virtual world within which he is able to increase his familiarity with the plants, testing the different activities indicated by the systems. The Digital Classroom also offers the ability to remotely participate in lessons and have real-time language support from interpreters (also remotely) when needed.
IMA E-Learning
Operators can continue training on their own through IMA E-Learning. Through a dedicated platform, similarly to what happens in the classroom, operators can follow courses and modules with ad hoc content and take final tests to obtain certification of their learning. It is also possible to use Virtual Reality, allowing operators to take advantage of the benefits of the virtual world wherever and whenever they want, with the possibility of taking tests that are integrated with the respective tests carried out on the same platform dedicated to E-Learning.
Structured learning in Digital Classroom and E-Learning brings with it several advantages: first of all, it guarantees training when a system is not available, because it has not yet been installed or because it is not possible to interrupt production for training activities. Secondly, it makes it possible to anticipate the training of operators, guaranteeing a saving in time and money to start up the plant for production as soon as it is installed.
A further plus lies in the on-premise nature of the technologies: all devices and platforms can be deployed at customer sites, ensuring proximity to the plants themselves.
IMA Digital Classroom and IMA E-Learning are integrated with the third modality developed by the Group and offered to customers, i.e. IMA Training on the Job.
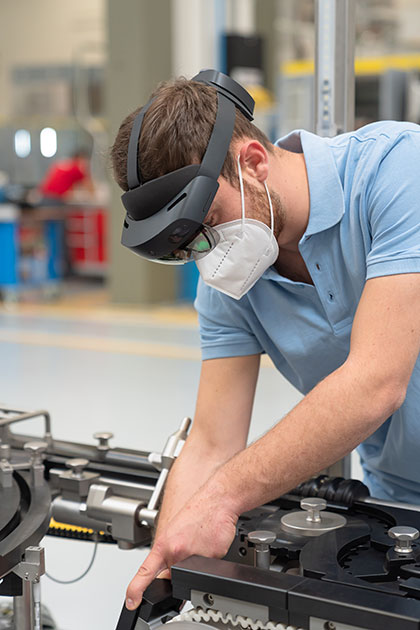
IMA Training on the Job.
The training started in the classroom and carried out independently is completed by the use of digital technologies directly on the plants, thanks to IMA Training on the Job.
The operators face this phase with the support of devices that guarantee a correct execution of all the phases related to the maintenance of the machines. The use of Hololens allows to receive all the practical indications through the use of elements generated by Augmented Reality. The possibility of accessing technical drawings, manuals and other documentation, guarantees immediate and updated content without the need for bulky paper manuals.
Hololens can also be used to receive remote assistance from an IMA expert in case of malfunctions on the machines (through the IMA Remote Assistance service).
Maintenance activities can also be carried out with the Smart Service Suite APP, the IMA application on mobile (and also usable offline) to support operators in the various sequential operations related to machine management. The APP also offers other interesting opportunities: access to the interactive digital documentation of the machine (catalogued according to TAGs for a faster search of the contents), carry out troubleshooting guided procedures, order spare parts directly from the production lines through the integrated e-commerce (in this case an active web connection is required).
A dedicated portal
All the contents related to the three Digital Training modalities are based on IMA Skillgate, the portal dedicated to the Group’s internal and external training. Structured in modules, which are in turn composed of individual courses, the portal allows operators to approach the knowledge of IMA plants in a practical and intuitive way, through the use of images, linear videos, 3D or animated elements.
At the end of each module and each course there is an interactive test that on the one hand involves the operator through active participation, and on the other certifies his career path, a conditio sine qua non for all those areas in which certified training is a necessary element of production activities.
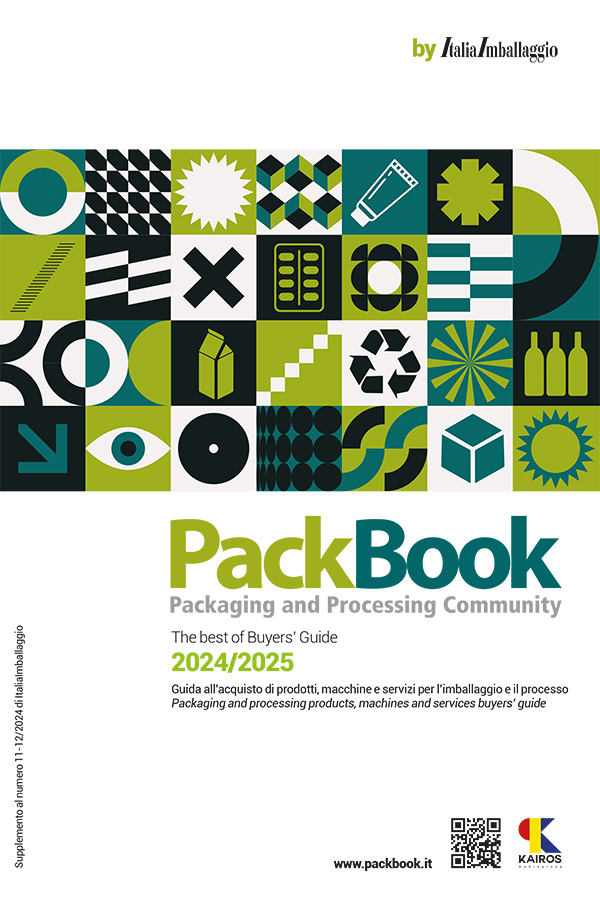