Autonomous Mobile Robot (AMR) for handling operations: when automation is the key to efficiency
An automated company is both more efficient and safer. For this reason, Volpak, part of Coesia, decided to invest in a long-term project aimed at increasing the level of automation in the facility. The first step on this path is the adoption of an AMR capable of moving autonomously in the production environment, effectively assisting operators in the assembly stage of the machines.
Do more with less, that means identifying low-value-added activities and eliminating them; this is the principle behind lean transformation. Volpak has thought of evolving this concept, turning what were time-consuming and risky activities for operators into quality time to be spent on higher-value tasks. Because of this, the company embarked on a long journey, aimed first of all at eliminating as much as possible all risky activities, such as transporting parts within the manufacturing plant. The ultimate goal is to become a highly automated company, where people can work harmoniously with machines.
A custom programmed robot. The first step in this journey is the adoption of an AMR, which is programmed to operate completely autonomously by carrying out transport and delivery operations of mechanical parts or electronic components within the company premises. Compared to Automated Guided Vehicles (AGV), which are constrained to predefined routes, AMRs have a greater level of flexibility, being able to be programmed to move completely autonomously. The robot control software was integrated to perfectly meet Volpak’s requirements.
Right on time. The robot adopted by Volpak moves free from patterns and operates in a mode known as "from push to pull". That is, it operates upon a specific request from the operator and moves according to smart logic, following the shortest possible path and making the various stops in an optimized manner. For example, it can figure out which parts to bring in first, differentiating based on factors such as operator location, part type, and production priority. This saves not only time but also energy.
Designed on a human scale. The robot can manipulate to different types of containers: with a top roll conveyor capable of transporting boxes up to 600x400mm in size and up to 100 kg in weight. Alternatively, it can handle a single pallet up to 200 kg in weight. The robot's movement is smooth and linear and is designed first and foremost to eliminate any risk of collision with people. At the same time, the smooth handling ensures that the parts - which, in many cases, are precision mechanical components - don't fall off or get damaged during transport. A single robot is currently in operation, but the company's development plans include the possibility of implementing additional units as needed.

Volpak will be present through its brand Enflex at the Achema trade fair in Frankfurt, from June 10th to 14th, 2024, to showcase its portfolio of solutions dedicated to the pharmaceutical sector. The company will be at the Coesia booth, Hall 3.0 Booth D73
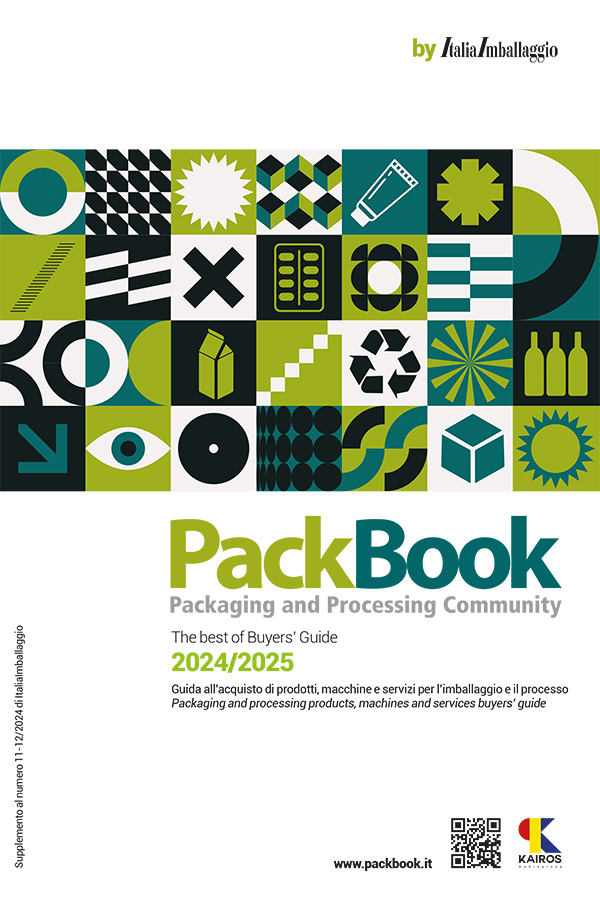