High hygienic transportation for food and dairy products
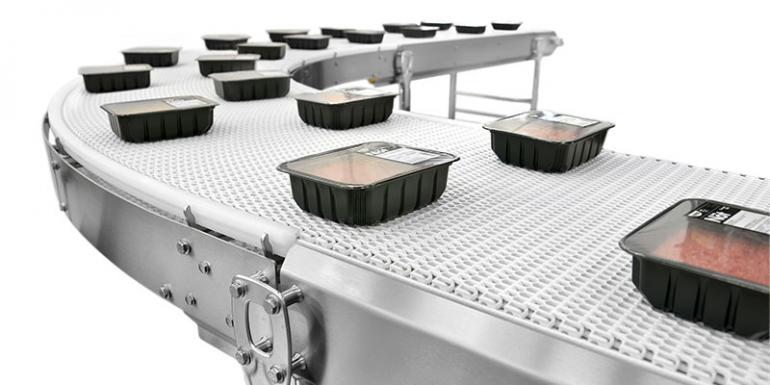
A leading supplier of systems for line and conveyor automation, FlexLink offers a specific range of solutions for transport and handling in the food industry.
The hygienisation of the production environment is crucial, and all the more so when processing unpackaged food - this is the case for dairy or bakery products - in very humid or dry environments. Hence facing a consistent demand from organic food consumers on the one hand and a prolonged shelf life on the other, the risk of contamination increases. This is why the process and packaging of food must be carried out in compliance with strict hygiene standards that prevent the spread of microorganisms.
Failure to comply with these criteria can lead to product recalls or, even worse, to health problems for the final consumer, with dramatic consequences on the brand image.
On the contrary, a line equipped with conveyor belts that meet specific hygiene criteria and simplified design, facilitates cleaning operations, reduces downtime and the overall cost of operation, with a positive impact on the entire supply chain.
FlexLink (part of the Coesia Group) has a particularly relevant know-how in the Food sector, for which it has created a specific range of transport solutions.
Ad hoc safety tools
The project is the result of a team with in-depth knowledge of the criteria that Food brands must meet to ensure the safety of the lines, as well as the challenges that they have to face on a daily basis to ensure maximum product quality.
This has led to the development of ad hoc solutions, aimed at increasing production efficiency, without forgetting the safety of operators.
The FlexLink systems for Food and Dairy, perfectly in line with the company’s construction philosophy, are characterized by an extremely compact and modular design, so as to simplify any changes to the layout.
They also guarantee precise yet gentle handling of the products, designed to minimize the risk of contamination.
Among the features that contribute to the overall hygiene of the production we cite the reduction of the time needed to clean the belts; the design without recesses and cavities eliminates the difficulties that could occur during this phase.
Finally, the reduced contact surface between the components and the absence of sharp surfaces also increases the level of safety.
And while FlexLink has always followed the guidelines of the European consortium EHEDG (European Hygienic Engineering and Design Group) in the design of the systems, it wanted to go further, to create a modular stainless steel belt called WLX, the only one on the market able to meet the strict “3A sanitary standards”.
To complement its conveyor systems, FlexLink offers a wide range of modules, thus being able to guarantee the handling of an even larger number of products, different in shape and size. The solutions that integrate the belts include cleaning stations, singularization modules and transfer jumpers, as well as a series of collaborative robots... A productive repertoire that, as a whole, is designed to help the customer reduce time and industrial costs.
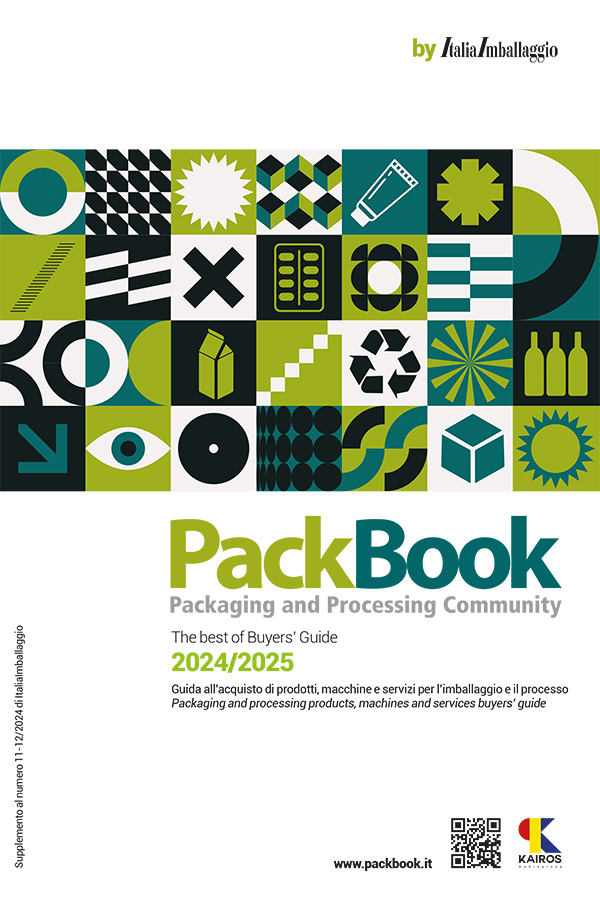