Oil-free compressors: quality and efficiency in packaging

For a “low energy consumption” packaging capable of preserving the quality of food, drink and pharmaceutical products, Atlas Copco offers a range of latest generation oil-free compressors.
Compressed air is used in 90% of plastic packaging lines intended to contain food or medicine.
Using oil-free compressed air, thus ensuring the absence of contamination from mineral oils, is of primary importance in order not to alter the properties and purity of the product during the packaging phase and/or in contact with the packaging.
Always at the forefront of the oil-free sector, Atlas Copco was the first manufacturer to receive the “Class Zero” certification relating to the ISO 8573-1 standard, which defines the purity standards of compressed air relative to the presence of particles of water and oil.
Added to this is that its Antwerp plant has received the ISO 22000 Certification, the most important global quality and safety standard for food and beverages.
Features and performance
Among the latest generation of Atlas Copco compressors are the ZT and ZR models, the first air-cooled and the second water-cooled, which, regardless of the conditions, produce certified oil-free air while ensuring a reduction in energy consumption.
Oil-free screw compressor ZT 90-160 STD. Available with variable and fixed speed drive, with or without an integrated dryer. All the components of the compressor element, such as the rotor profiles, the entry and the coating of the rotors, have been redesigned for maximum efficiency and durability.
The configuration and tightness of the compression chamber ensure the physical separation between the oil and the air circuits, eliminating the possibility that the oil enters the compression chamber and thus ensuring Class 0 oil-free air.
The compressor is equipped with a high efficiency IP 55 TEFC motor: protected from dust and humidity, it guarantees continuous operation even in extreme ambient temperature conditions. The intake air filtering system contains a 2-stage dust removal system that minimizes suction losses and provides a reduced pressure drop. The FF version compressor integrates a dryer that reduces the space required for the system and makes the compressed air immediately available in the quantity and quality required.
Water-cooled compressor ZR 90-160 VSD+. Equipped with two high-efficiency permanent magnet motors, state-of-the-art compressor elements, a new chiller design and an improved monitoring system.
This plug-and-play compressor is housed in a compact and soundproof cowling. The internal permanent magnet motors are water cooled with IP66 protection degree and are equipped with oil lubricated bearings for long life without maintenance.
The redesigned chiller is equipped with a high efficiency water separator. The parallel water flow optimizes the cooling of the motor, the element and the chiller itself.
The wider stainless steel surface of the chillers improves cooling efficiency and ensures excellent performance with a long service life. Thanks to the variable speed VSD technology, able to faithfully follow the consumptions of the production line, it is possible to obtain a significant reduction not only of the energy consumption, but also of the management costs of the entire plant, favoring at the same time a lower impact environmental.
Among Atlas Copco’s customers in the packaging sector we cite Goglio, a company at the forefront in the production of complete packaging systems and for which, since the beginning of the 90s, the compressed air service has become a fundamental element for guaranteeing quality, reliability and safety.
Goglio chose Atlas Copco oil-free compressors precisely because of their important certifications, which guarantee air quality, but also for the companies Preventive Maintenance Plan, which can provide maintenance, updates and repairs for possible flaws and malfunctions. All this to achieve maximum levels of efficiency and reliability in the production of compressed air.
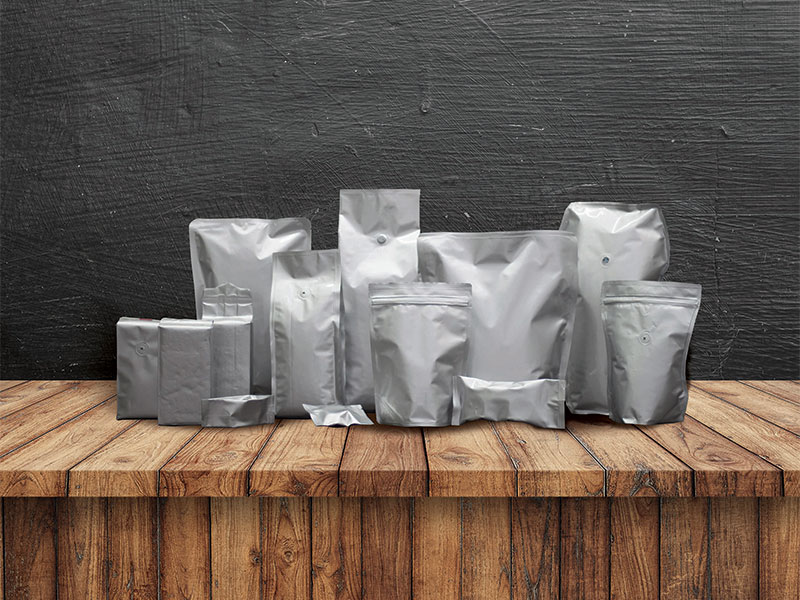