Safe pallets with stabilizing adhesive
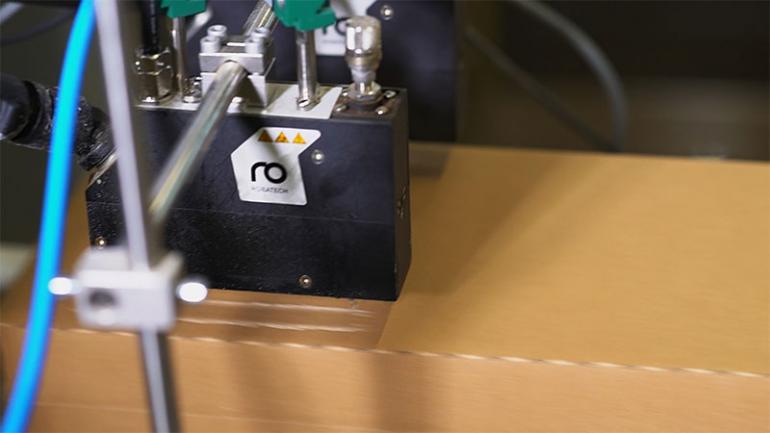
In 2020, the Swissmill installed the Robatech ANTISLIP GLUING adhesive application system to reliably stabilize cardboard packages placed on pallets. The result is sustainable and efficient: 75% less plastic film consumption and time savings for a low investment.
Swissmill (Coop Group) is the largest milling company in Switzerland. At the Zurich site, over 200,000 tons of cereals are processed into more than 100 different products (basis for cereal bars and flakes, crackers and bread).
Before adopting Robatech solutions, Swissmill only used stretch film to wrap and stabilize pallets during transport by truck and rail.
On the initiative of manager Erwin Waldvogel, a pilot project for sustainable palletizing of the packages with Robatech Antislip Gluing was started in the cereal flakes production department in only 8 months from the beginning of 2020.
Easy retrofit
In the Swissmill cereal flakes production and packaging line, 500 g bags for various brands are filled and packed in 12-pack cartons. At the end of the line, a robot stacks 84 cartons on a pallet in seven crossed layers. And it is at this stage that Robatech’s solutions come into action. For each layer, excluding the last, two AX spray guns apply two strips of glue (PSA-based hot melt adhesive) to the top of the cartons. The operation is controlled by the palletizing function integrated in the control electronics of the Concept melter, which communicates directly with the control of the palletizing robot.
Only pallets destined for rail transport - which are exposed to greater forces that may cause the top cartons to fall - are wrapped with stretch film after the application of hot glue, but only half of it. This is enough to obtain uniform load distribution, avoiding loss of stability and accidental collapses.
Advantages
The solution proposed by Robatech has made it possible to reduce the consumption of plastic film by 75%, with a double benefit, both in terms of sustainability and economic savings. A second positive effect is time saving. In fact, operators no longer have to transport pallets from the packaging line to the wrapping station and vice versa. This shortens the working time by 1.5 hours per day, which can be dedicated to other essential activities. Satisfied with the industrial results achieved, Erwin Waldvogel also emphasized the cost-effectiveness of the Robatech system, which was realized with a low investment and amortized after just a few months.
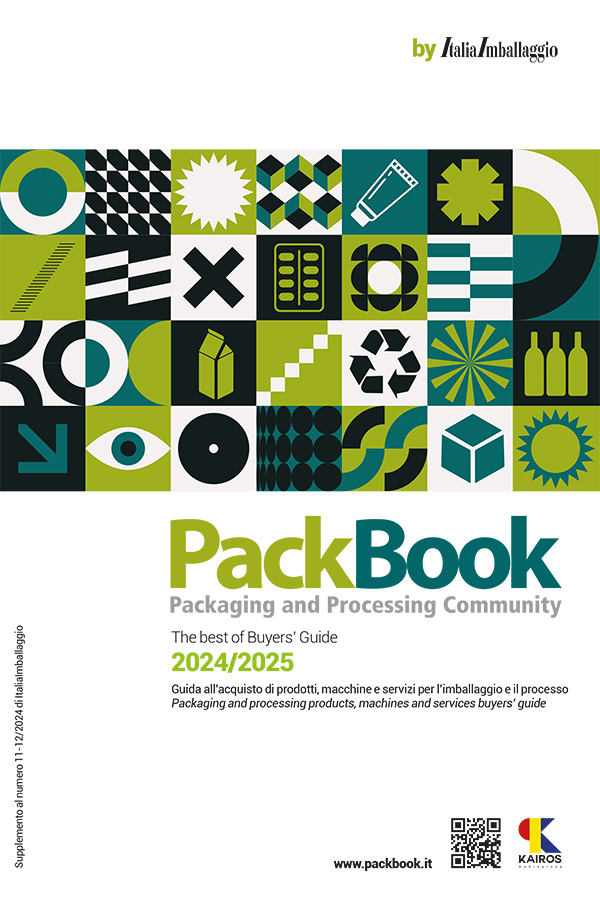