Ultra-clean combi technology at room temperature
Orkla strengthens the production of ketchup with Sidel
Orkla has strengthened the capacity, safety and efficiency of its ketchup production, responding to the growing demands of consumers looking for more convenient, sustainable and healthy products, that is, with a lower sugar, salt and preservative content. The new packaging in PET that the company has recently adopted, adapting its production model with a Sidel integrated solution for blowing, filling and capping operations, also goes in this direction.
Orkla Foods, leader in the ketchup, sauces and seasoning market, sells branded products in central-northern Europe and in the Baltic countries. The Group’s main ketchup production site, situated in Fågelmara, in the south-east of Sweden, produces thirty million bottles of ketchup per year with twenty different recipes.

The new packaging: a model of food and environmental sustainability
To meet consumers’ demands, increasingly oriented towards better nutritional properties and the sustainability of products, Orkla has redesigned its packaging range, passing from cylindrical polypropylene (PP) bottles to modern flat rectangular designs in PET.
The new containers can be easily "squeezed" and can be completely emptied, without wasting any of the product. In addition, the new bottles in PET are 30% lighter compared to the previous container in PP and composed of at least 25% recycled PET (rPET) with the objective of arriving at 50%. The preforms, previously blown in the United Kingdom and then transported to Sweden, are today bought locally, with a reduction of 90% of transport-associated CO2 emissions. This aspect of production is assigned to Sidel's preferred heating technology, which optimises the distribution of the PET and allows for the asymmetric stretching operations necessary for blowing flat and shaped containers.

Cold production with the same hygiene standards and lower consumption with Predis™
Combis Sidel uses an ultra-clean filling technology at room temperature within an integrated Combi solution, which offers also blowing and capping functions. With the Predis™ preform sterilization system integrated into the blow moulding machine and the dry decontamination of the caps performed by the capping machine, Orkla’s quality and safety standards have also been fully met.
The Predis™ Combi’s blowing-filling-capping solution combines all the functions and transfers (performs, bottles ad caps) inside a single safe environment, eliminating any risks. In short, replacing the now obsolete stand-alone filling technology used in the company, Orkla has abandoned the hot-filling process that uses temperatures above 85 °C to guarantee stability of the product and a hygienic production, but also involves high energy consumption.
Thanks to the use of an aseptic surge tank, moreover, the new configuration not only allows for filling at room temperature with a lower quantity of preservatives in the recipe, but it also reduces the energy and water consumption of the process and of the packaging line, as the lower temperature means that the containers do not need to be cooled. Finally, the safe storage of the product batch in the aseptic tank during production and the format change on the packaging line offer two big advantages: a reduction in waste and simple format changes with shorter execution times.
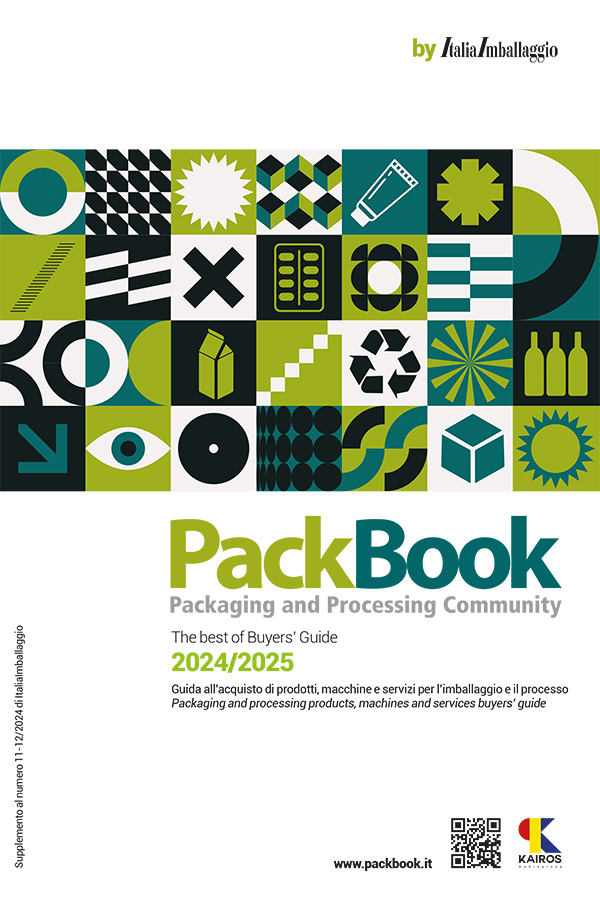