Six degrees of freedom in adaptive manufacturing
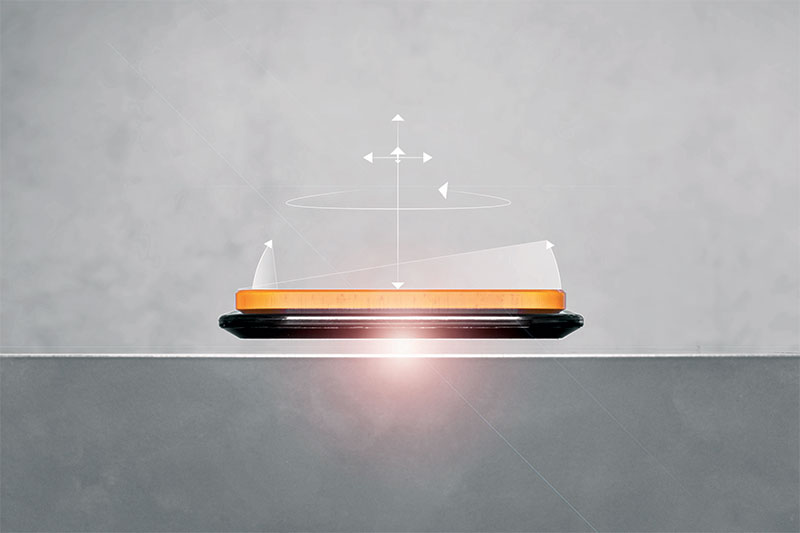
Based on the principle of magnetic levitation, B&R’s ACOPOS 6D opens up a new dimension in adaptive manufacturing. The suffix “6D” in the name stands for “6 Degrees”, i.e. the degrees of freedom the system can offer.
The world of manufacturing is facing a series of challenges, which raise non-trivial critical issues for both end users and machine builders. Compared to the paradigms of the past, products are in fact characterized by extreme variety and are made in ever smaller batches. But their lifecycle is also getting shorter and shorter. In the face of these variables, it is very complex to be able to forecast productive cycles and mass-customization is becoming a common requirement.
These are, to all intents and purposes, urgent and ambitious requests, which require the adoption of a completely new production model, that of adaptive production. To put this paradigm into practice, however, four key requirements must be met:
- zero downtime, switching instantly from one product to another, from one package to another;
- readiness to handle future. It is impossible to anticipate all the changes that a product line will undergo during its lifespan. That’s why machines built today will have to handle products and meet requirements that don’t yet exist;
- high productivity and accelerated time-to-market: this is the only way to keep up with unpredictable fluctuations in demand;
- profitable small batch production. Mass customization represents a definite competitive advantage for manufacturers, provided, however, that they are able to produce small batches at costs comparable to those of mass production.
As a supplier of automation systems, B&R has been supporting machine builders and end users in the creation of inline solutions for several years, relying on the four pillars of adaptive manufacturing. A key piece in the adaptive factory puzzle is a handling system that can move products through the machine and across lines intelligently and flexibly. This is where B&R’s most recent development comes in: at the heart of this epoch-making change is in fact the ACOPOS 6D system, designed in collaboration with Planar Motors Inc., a Canadian company with over 15 years of research and development in the field of magnetic levitation technology for industrial production, of which B&R is a shareholder. Gone are the days when conventional handling systems imposed rigid schedules anchored to a sequential production process, the ACOPOS 6D conveyor system is based on the principle of levitation: the shuttles incorporate permanent magnets that keep them suspended above the continuous surface created by electromagnetic motor segments.
The modular motor segments measure 240 x 240 mm and can be freely arranged to create any shape of movement space. With a range of shuttles of various sizes it is possible to carry payloads from 0.6 to 14 kg and reach speeds of up to 2 m/sec. Shuttles can move freely in two-dimensional space, as well as rotate and tilt along three axes and levitate with precise height control. Combined, these movements enable “six degrees of freedom” control. Let’s look at them together.
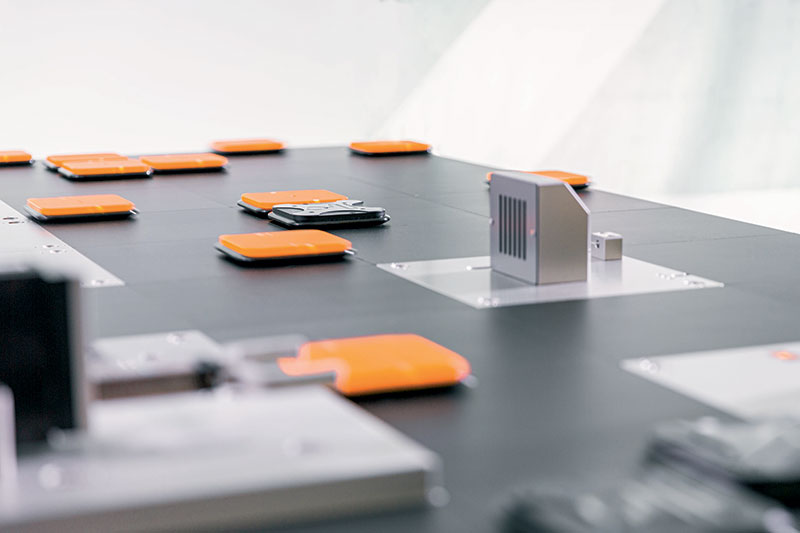
First and second degrees of freedom. Unlimited flexibility of motion in the 2 linear dimensions of translation. The permanent magnets in the shuttles interact with the magnetic field generated by the motor segments. The resulting force allows the shuttles to float in the air. For this reason, ACOPOS does not need a guidance system and the shuttles do not follow a predefined path, but can perform any kind of movement on the surface of the motor segments, giving machines and lines unlimited flexibility of movement. Where, for example, a machining head is installed, it is no longer necessary for it to move in relation to the product, which is statically positioned, since, on the contrary, it is the product itself that can move underneath it, even in non-linear trajectories. ACOPOS 6D therefore enables the replacement of mobile machining heads with static heads, with considerable advantages in terms of costs, sturdiness and maintenance.
Third degree: levitation. The system offers full control of levitation height, from half a millimeter up to 4 mm. But that’s not all: it allows you to control the force applied to the shuttle, regardless of payload. Shuttles can tell the control system how much force they need to apply to maintain a constant height. This also allows for accurate weight measurement, eliminating the need for a weighing station.
Fourth, fifth, and sixth degrees: angular motion along the Z Y Z axes. The shuttle can rotate and tilt along the X and Y axes. These two extra degrees of freedom can be used in a very useful way by synchronizing rolling and pitching with other movements, for example to enhance the anti-sloshing function by tilting in curves. In addition, in machining stations where you need to manage the angle of the product along the X and Y axes, this function can be performed by ACOPOS 6D, eliminating the need for additional drives, optimizing space management and reducing hardware costs. Finally, rotation along Z axes allows you to rotate the product as it moves between stations, eliminating the need to introduce stations to reorient parts. Again, machining stations can be made more efficient and compact.
ACOPOS 6D connects seamlessly with the entire B&R ecosystem, and with machine vision systems. Thanks to the complete software integration and the unique integration in the POWERLINK bus real-time, it is able to fully synchronize with other devices in the network at µs.
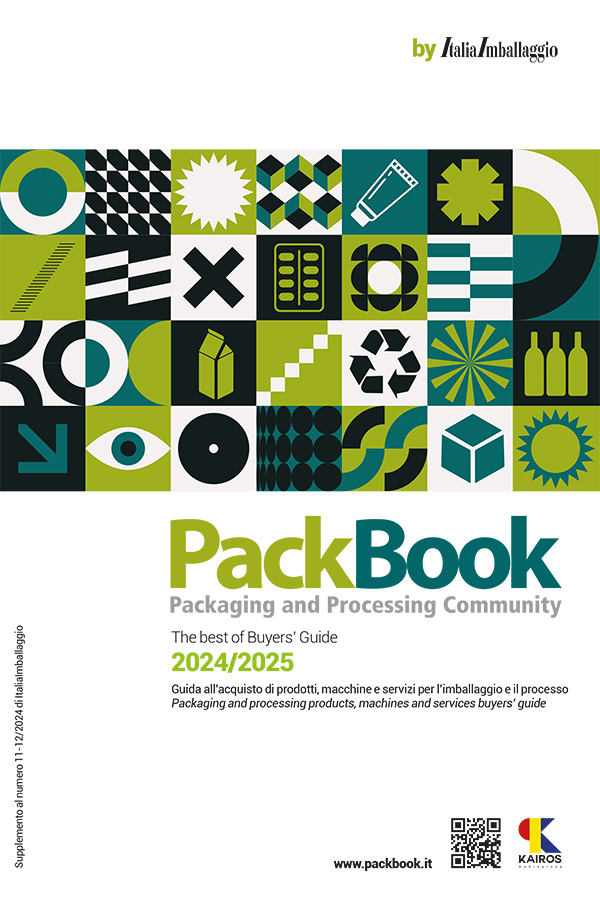