Top Cap vaccine closures: integrity and safety
The commitment on the Covid-19 front of Capsulit, a specialized manufacturer of closure systems for pharmaceutical packaging that, even in the midst of the pandemic, has never stopped. Focus on Top Cap injectable capsules: available in several variants, they ensure product integrity as well as a safe and convenient patient experience.
For over 70 years, the Italian company Capsulit has been a recognized leader in the production of closure systems for the pharmaceutical industry, to which it offers products of proven and consistent quality, benefiting the overall efficiency of filling and closure lines.
Thanks to the expertise gained in decades of collaboration with leading pharmaceutical companies and the flexibility with which it responds to their needs, it offers a wide range of products: capsules for injectables, closures for powdered products (supplements and probiotics), antimicrobial closures, biodegradable closures and bottles, unbreakable spoons.
Since the beginning of the Covid-19 emergency, however, Capsulit has considered it a priority to devote its efforts to the production of closures for vaccines, drawing on decades of experience and constant updating. This has enabled it to supply capsules intended for Covid vaccines to the European and American markets, developing a project that will allow it to increase production capacity.
Top Cap injectable capsules
They have different diameters, shapes and heights, defined according to the size according to ISO standards and can be entirely in aluminum, plastic, or in aluminum and plastic. Called Top Cap, Capsulit capsules for injections are produced in three distinct technological phases: shearing of the ring nut starting from aluminum coil, molding of the plastic disk through an injection process in multi-cavity molds, assembly of the two components using high-speed automatic machines.
Variable in diameter, shape and size, as mentioned at the beginning, the Top Cap capsules can also have different coupling systems between the two components, designed for easy opening and, at the same time, to guaran-tee the inviolability of the package.
All variants are also customizable with engraved or printed brands with autoclavable colors.
RTS Version. The Top Cap can be produced and packaged in the RTS (ready to sterilize) version, therefore ready to undergo gamma and beta sterilization treatment, or in an autoclave using processes validated according to ISO 11137.
The closures for gamma or beta treatment are packed in double low density polyethylene bags, heat-sealed according to Capsulit specifications or ac-cording to specifications agreed with the customer. Studies carried out on the packaging guarantee their tightness - and therefore the sterility of the contents - for a period of at least three years.
The closures intended for autoclave treatment at 121 ° C for 30’ are instead packed in special heat-sealed Tyvek or Stericlean bags.
RTU Version. The capsules can also be supplied in RTU (ready to use) version treated with gamma rays by specialized partner companies, with a minimum level of 25.0 kGy through processes validated according to the ISO 11137 standard aimed at guaranteeing a sterility level of 10- 6.
Each batch of RTU closures is accompanied by a treatment certificate issued by the partner company, which carries it out according to validated processes and in accordance with the agreed specifications.
At the customer’s request, a representative sample of the batch can be subjected to sterility tests performed by an external laboratory, which guarantees its compliance by issuing a relative certificate.
On samples of capsules representative of the batches produced, Capsulit periodically checks the microbial load (bioburden) and dose audits, to verify over time the validity of the initial validation according to ISO 11137.
R&D in progress, under the sign of quality
The constant innovation of processes and products is another key feature of Capsulit. The company has implemented a constant commitment to innovating production processes and its range of closure systems thanks to the internal R&D department also in collaboration with customers.
In addition to the controls foreseen by the quality procedures, on the production lines Capsulit uses sophisticated vision systems, that ensure the quality of the production 100%, with the expulsion of any defective parts. The robots installed also make it possible to reduce the handling and possible contamination of the capsules, which are produced using state-of-the-art technological systems. The processes are constantly monitored by state-of-the-art automatic systems, the processes are therefore connected online with the company’s IT system: according to the logic of Industry 4.0, in this way, the progress of orders is always under strict control.
Certified ISO 15378, 9001, 14001, 45001, DIR. 93-42-CE - and soon to be ISO 13485 - Capsulit operates in compliance with Good Manufacturing Practice standards. In pursuing long-term economic growth, Capsulit has always placed the values of social responsibility and respect for the environment at the center of its vision, embracing the paradigms of sustainable development with conviction. To this end, for several years it has set up an “Integrated Business System for Quality, Safety and Environment Management”, commit-ting itself to implementing continuous improvement policies, aimed at guaranteeing the quality of the product and service, the reduction of the environmental impact of activities and maintenance of personnel safety and health.
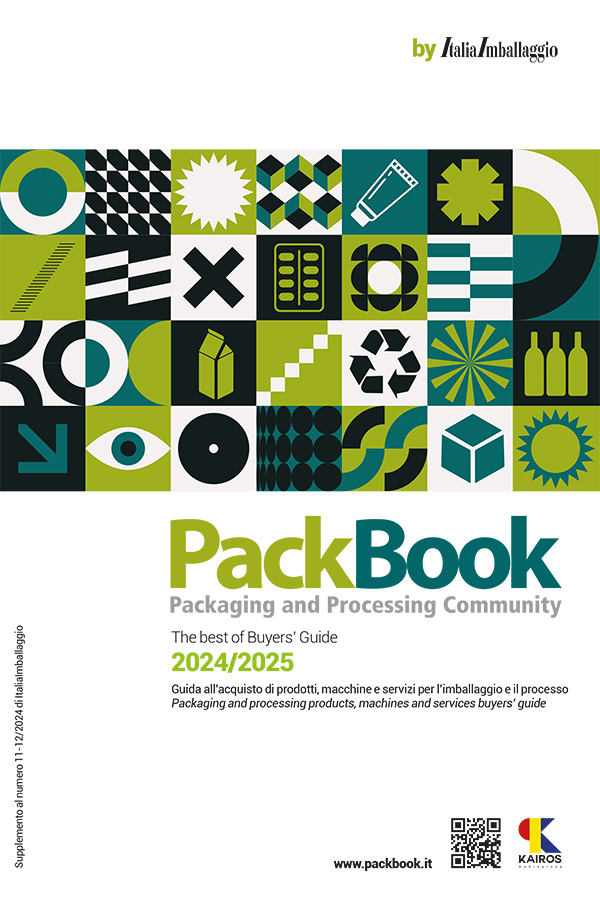