The Transition 5.0 Plan for the packaging industry
This measure is not merely an opportunity to reduce consumption and emissions but a strategic programme for enhancing Italian excellence through innovation and sustainability
Stefano Lugli e Priscilla Russo
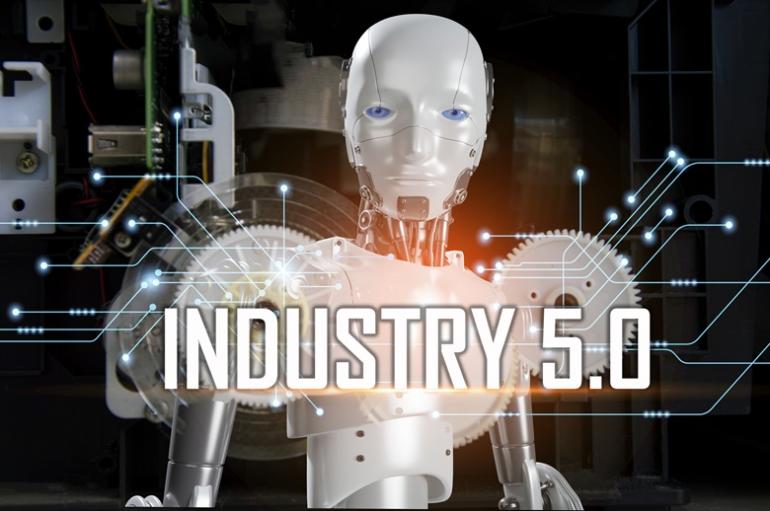
Sustainability and energy efficiency have long been top priorities for the packaging industry, with the sector consistently welcoming European and national initiatives aimed at facilitating the energy transition. One of these is the new Transition 5.0 Plan, which allocates €6.3 billion of EU funding exclusively to projects focused on improving the energy efficiency of Italian industry.
This ambitious measure combines the challenges of energy sustainability with the opportunities offered by an advanced level of digitalisation. Transition 5.0 is not merely an opportunity to reduce consumption and emissions but a strategic programme for enhancing Italian excellence through innovation and sustainability. Italy will receive the funding through the European REPowerEU Plan, which aims to reduce the EU’s dependency on Russian gas supplies and lays the foundations for a transformative production model that embraces circularity.
The specifics of the Italian Plan
The new measure, introduced into the National Recovery and Resilience Plan (NRRP) subsequent to EU Council Implementing Decision 2023/16051 of 8 December 2023, aims to help businesses navigate the digital and energy transition by granting tax credits and is expected to bring a reduction of 0.4 Mtoe in final energy consumption in Italy over the period 2024-2026 (a figure agreed on with the EU).
Since then, a series of national provisions have been adopted to implement the plan, the most recent of which was dated 6 August and led to the launch of a digital platform for project submissions. Several application circulars and FAQs have subsequently been issued to address key questions that the new tool had raised among experts.
For a number of reasons – primarily the complexity of the procedure, along with the five-year post-investment monitoring obligations and the significant costs involved – the Transition 5.0 Plan has struggled to gain traction in its first quarter of implementation. The government has sought to address these issues by introducing a number of corrective measures and simplifications into the 2025 Budget Law. The most important of these is the automatic approval of the procedure for replacing obsolete machinery, which should give fresh impetus to the relief measure.
As a result, the Transition 5.0 Plan is becoming an increasingly valuable tool for all companies in the sector. For example, an investment of €2.5 million can yield significant tax credits depending on the energy savings achieved: €875,000 for savings between 5% and 10%, €1 million for savings between 10% and 15%, and €1,125,000 for savings exceeding 15%.
Application of the Plan by Italian companies
Industry 4.0 revolutionised the packaging industry with the introduction of advanced automation, robotics and real-time data management. Transition 5.0 takes these innovations even further, not only enhancing processes but also fostering interconnected and sustainable production. By integrating predictive analytics, artificial intelligence and Internet of Things (IoT) with green energy management systems, it achieves optimal efficiency while minimising environmental impact.
The essential starting point for evaluating the Transition 5.0 project is to correctly define the production process targeted by the investment and its classification or subdivision, while bearing in mind that interventions must focus exclusively on a single production process at a time.
Initially, the packaging sector seemed disadvantaged by this requirement, as there was debate over whether the entire packaging operation – typically composed of multiple lines – should be treated as a single, unified system.
Fortunately, the interpretative circulars and FAQs clarified the guidelines by introducing the concept of sub-processes and allowing for evaluations based on average consumption values, thereby enabling the packaging sector to fully exploit the Plan’s benefits. Companies are now able to replace individual packaging lines, expand production with the addition of new machinery or upgrade or replace specific machines, provided energy-saving targets are achieved at the sub-process level.
Additionally, certain technologies are recognised as standalone processes, according to the sector’s association Ucima. These include palletising and end-of-line solutions, integrated conveyor systems linking up the various machines, as well as sterilisation and washing equipment.
Mini-guide for access to incentives
The interventions must focus on just one production process per project. The assessment must always be conducted on a case-by-case basis. Projects may cover two or more of the aforementioned interconnected processes or may focus on even more finely divided process stages.
As with the previous 4.0 framework (still applicable but alternative and not cumulative with 5.0), the scope of eligible assets includes capital goods accompanied by software for energy monitoring and improvement, as well as systems for quality and environmental control.
It is important to note that the required energy savings are not defined by an absolute value (e.g. a minimum of x kWh saved) but are instead measured as a relative percentage improvement compared to the company’s pre-intervention baseline (the minimum required energy saving is 5% for interventions on an individual production process).
Clearly, when working on obsolete and technologically outdated processes it is normally easier to meet the energy saving targets required to qualify for the tax benefit.
In addition, a crucial aspect raised by Ucima with the relevant Ministry from the outset is the normalisation of energy consumption data. Energy savings must always be correlated with production data both before and after the intervention. This means that a project can meet the targets, and thus qualify for the benefit, even without a reduction in energy consumption, provided there is a significant increase in annual production or a reduction in factors such as maintenance times, waste or line tooling times. For detailed examples refer to the MIMIT/GSE Application Circular dated 16 August 2024.
One particularly interesting aspect of the plan is the possibility of complementing the principal investment, which focuses on capital goods, with secondary investments such as the introduction or enhancement of photovoltaic systems or training projects. These secondary investments are financed at the same rates as the principal investment, apart from photovoltaic systems which are eligible for an additional bonus, further enhanced by the recent 2025 Budget Law.
Application considerations
The Plan is set to end on 31 December 2025, with a two-month grace period (February 2026) to allow companies to submit the extensive documentation required. By this date, all equipment must be delivered, installed, tested and interconnected (an Industry 4.0 expert opinion is also required). Given the tight timeframe, Ucima has already requested an extension, which is currently expected to be approximately 4 months. However, this measure has unfortunately not been included in the drafting of the 2025 Budget Law.
Procedural aspects to note:
- The reference is based on annual consumption (e.g. 2024 compared to 2023).
- There is no requirement for a particularly long measurement period, nor is there a minimum sampling frequency. Estimates can be used, and it is recommended that they are supported by measurements that accurately reflect the production cycle and its intensity.
- Only one project per plant may be submitted at a time. A new project may not be submitted until the previously submitted project is completed.
- Pre-project and post-project energy certification attesting to the projected energy savings and providing a technical explanation of the results achieved must be prepared by a qualified third party. This party must certify their independence from the beneficiary and possess the appropriate administrative credentials.
- A procedure is available for accessing the benefit in cases where a comparison with a previous situation is not possible, as in the case of a new plant. In these instances, a counterfactual scenario will be used.
For five years following the completion of the investment, the GSE (National Energy Services Operator), the Ministry’s technical body responsible for managing procedures and verifications, may conduct checks to ensure that the declared energy saving values are attained subsequent to the project.
This makes it even more important for packaging machines to be equipped with tools for measuring minimum energy consumption via PLC systems, as well as accurate measuring instruments that can track energy use in relation to the number of pieces produced and hours worked. Such precise monitoring not only simplifies the reporting of savings but also contributes to ongoing verification of the project’s sustainability.
The manufacturer’s role and responsibilities
It is important to note that Transition 5.0 does not impose specific or additional energy efficiency obligations on manufacturers. The latest technological proposals are essentially “candidates” to meet the targets required to obtain the benefit. Unlike the 4.0 framework, where the technical characteristics of the machinery were paramount, the focus under Transition 5.0 is necessarily correlated to the pre-investment baseline. This means that there are no “5.0 ready” machines per se, but rather technologies capable of delivering adequate energy efficiency. Supplies cannot be contested for failing to meet specific thresholds or efficiency values derived for example from literature; the only valid metric is the comparison between consumption values before and after introduction of the new technologies. The manufacturer’s role is therefore crucial, as he is the only party capable of providing normalised consumption data for the new technology.
Moreover, as clearly outlined in the Operating Circular of 16 August, both pre-project and post-project certifications must rely on traceable data derived from appropriate technical documentation. Rather than simply providing data plate consumption values, which are often unnecessarily overstated, manufacturers must perform a more detailed estimate or measurement of overall energy consumption per hour of production or, preferably, an estimate or measurement of energy consumption per unit, weight or cubic metre of output.
The role of UCIMA
The association can provide technology suppliers with a document called the “Technical Energy Efficiency Certificate”, which includes the most important information required to provide an accurate consumption figure. To prepare this certificate, experts must use MID-certified measuring instruments, as shown by the test reports attached to the certificate. This certification can also be tailored to specific cases within the plant in question, serving as an a priori validation that can be provided to the customer as part of their documentation.
Additionally, through its Facilitated Finance Area, Ucima is ready to assist technology manufacturers and packaging companies in navigating the procedures related to Transition 5.0. This support draws on Ucima’s in-depth understanding of the sector’s production processes, while the SBS Training School is fully equipped to provide comprehensive and in-depth training on the subject.
Conclusions
Transition 5.0 marks a significant technological and cultural shift aimed at integrating sustainability and digital innovation within the industry. While presenting operational and regulatory complexities, with the necessary precautions it also offers an opportunity for the sector to evolve. With careful planning and collaboration between companies, manufacturers and institutions, the industry will be able to initiate a gradual process of adaptation that will help redefine its role in a production landscape that is increasingly focused on efficiency and sustainability.
Attestations include key information
• Estimates/measurements of the machinery’s main energy efficiency parameters (e.g. power consumption) with regard to consumption of electricity, compressed air, thermal energy, etc.
• Estimate/measurement of total energy consumption per hour of production. Calculation of energy consumption per unit produced, essential to assess/compare energy savings compared to the prior situation.
• Technical characteristics of the most important components (electric motors, etc.) and their evaluation in terms of energy efficiency
• Measures taken by the manufacturer to reduce the energy consumption of machinery compared to the past.