OMAC, between Automation and Manufacturing
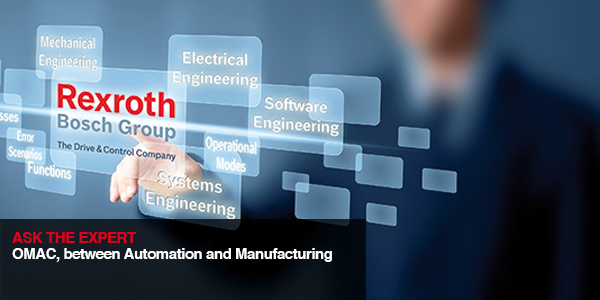
ASK THE EXPERT Processing automation, energy, timed cams, open and modular automation architecture, soft automation, service: in the column on ItaliaImballaggio called “Ask to the Expert”, Luca Stanzani (Packaging and Processing Bosch Rexroth Italia) will provide answers for the specific problems that the readers will tell them about. Write to [email protected].
This month we will be answering the many questions and requests for insight on the concepts behind OMAC and PackML™.
What is OMAC?
OMAC is an organisation that aims to provide support in an area that lies somewhere in between machine automation and manufacturing. OMAC includes two workgroups: The OMAC Packaging Workgroup (OPW) and the OMAC Machine Tool Workgroup (OMW). The OPW is, clearly, the reference point for packaging.
What is OPW's objective?
The OMAC Packaging Workgroup's objective is to increase machine efficiency and integration by minimising customization, thus simplifying and reducing the time necessary - and hence the cost - to install a machine along the production line.
How is the installation time reduced?
Mere operational validation (mechanical, SW…), logically essential, does not suffice. Let us consider a machine that has been fully tested at the place it was manufactured. It must then be dismantled, transported and then reassembled at the production site. Should there be drawbacks in connecting the machine with the other production line units or during reassembly, the installation time would not be optimised, despite the fact that the machine has been fully tested at the place it was manufactured. The application SW must be able to communicate with the production line and must be able to do so as quickly as possible. A suitable design of the mechanical, electrical and SW components is therefore required and ensures that transport and assembly as well as the physical, electrical and SW connections, performed at the production site, are straight forward and that installation times are thus brought to a minimum.
Why is it important today to communicate with a supervisor?
All operators set productivity targets. Knowing mere production data no longer suffices as it is also important to acknowledge possible areas for improvement and the reasons why set targets are not being achieved. OEE (Overall Equipment Effectiveness), for example, is now a well-known acronym: it represents a widely used and appreciated method to assess the productivity of a plant in terms of quality and quantity.
What role is played by OMAC?
OMAC has standardized the machine-upper level interface. Those complying with this standard must supply information concerning established definitions and situations. This information chiefly defines the machine's status, machine status times, causes of machine downtime, production data, the provision of materials (the product requiring packaging, the boxes to be filled...). Supervisor and production lines are therefore speaking the same language. This is the reason why SW installation time, i.e. the time necessary to install the machine's SW at the production site, is brought down to zero.
What is this common language called?
It is called PackML™. The acronym means Packaging Machine Language i.e. a group of rules that OMAC has standardised by defining a common interface, thus allowing a unit along the production line to become readily operational. The PackML™ Implementation Guide is a reference document for the implementation of PackML™ within a SW.
Does the Rexroth system support PackML™?
The Rexroth system does support PackML™. It does so by means of a structured solution or a solution integrating a user SW structure, in order to provide the client with a range of solutions to choose from according to his needs. Rexroth assistants are able to provide support for fully user-oriented solutions via the Rexroth resources that operate within the OMAC groups.
What difficulties are encountered in implementing PackML™ within the SW?
Technically there are no real issues. Issues are mostly cultural or historical. Several manufacturers have only recently been facing such issues, some have yet to face them and some are about to face them. Other manufacturers have successful and well-rooted structures that were established within the technical office for SW design when PackML™ wasn't as well-known. Bosch Rexroth's mission is to provide support for the aforementioned situations and it is confident it has the expertise and the necessary skills to do so successfully and fulfilling everyone's expectations.