A “made in Italy” carbon fibre recycling partnership
The Hera Group, CURTI and the University of Bologna work together on carbon fibre recycling. The imminent start of construction of a specialised factory in Imola forms part of the project which, in consideration of its environmental value, has obtained European funding within the scope of the NRRP, for a value of over 2 million euros.
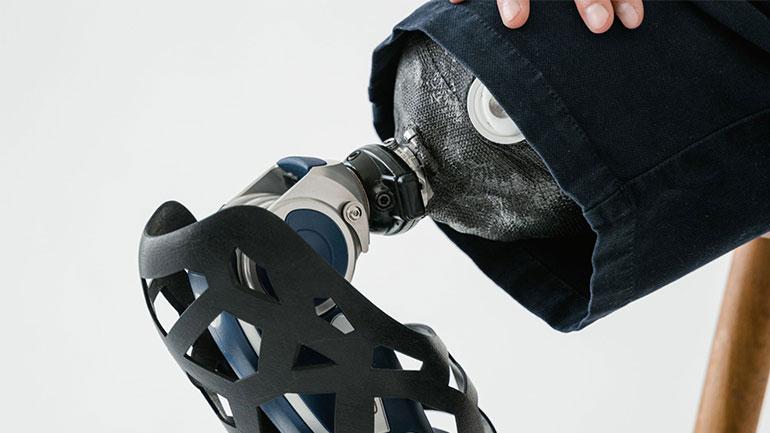
Work on an innovative plant to regenerate carbon fibre is to start at the beginning of March, making “Made in Italy” even more green, given that the material produced will be used in sectors linked to national manufacturers of excellence such as the automotive, aerospace and nautical sectors, but could also be used in the production of biomedical prostheses and sports equipment.
Pieces reaching the end of their life-cycle currently end up in landfills, but thanks to the technologies developed in partnership by the Hera Group, Curti and the Industrial Chemistry Department of the University of Bologna, they can be recovered and recycled, giving rise to a material with “virgin-equivalent” characteristics.
The fibre will be recycled and regenerated in a plant specially-built by Hera Group in Imola - the first in Europe - with the involvement of Aliplast, the group specialized in the production of recycled plastic, which will coordinate the commercial strategies.
The platform will be set up thanks to the supply of Curti SpA machines for processing the material on two production lines, the first of which will start operating at the end of the year, while the second will be operational by the end of 2024.
The Imola factory is focusing strongly on the quality of the material, more than on the quantity: production capacity is expected to be around 160 tonnes per year for each line.
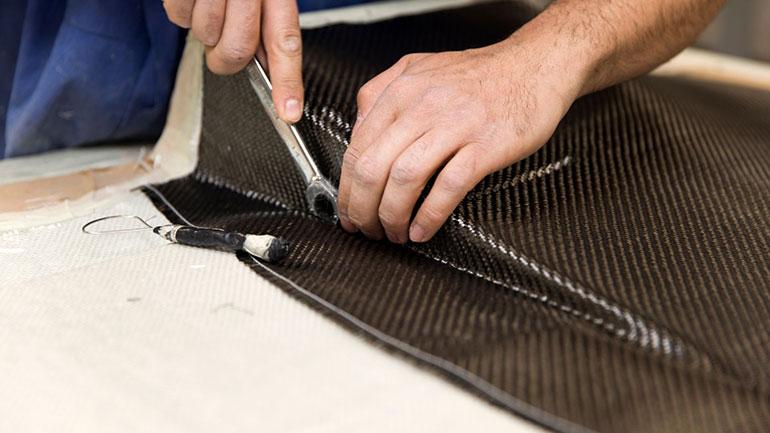
Same quality, lower environmental impact
The different types of material (see box) that will be produced by Hera Group’s plant have a number of shared characteristics. First of all, the quality, equivalent to a virgin product in terms of mechanical resistance.
Environmental impact, on the other hand, is lower: on average, the energy required for the production of recycled fibre is, in fact, 90% less than that required for the virgin product.
Moreover, the specific technological solution for recovery chosen by Hera Group has 50% less impact in LCA terms compared to traditional methods for the treatment and disposal of carbon fibre waste.
The material obtained will, therefore, enrich Aliplast’s portfolio, adding to recycled plastics and packaging in its catalogue, extending its offer to a wide range of production sectors.
Recycled carbon fibre: how it is obtained
The regenerated material is obtained through a thermal process called pyro-gasification, which frees the carbon fibre, more resistant to heat, from the resin added in the moulding and forming phase. The latter decomposes, and through gasifying, is reused to generate part of the energy necessary for the process, maximizing also energy recovery.
At the end of this phase, a fabric composed of carbon filaments is obtained. This material is then be sent for processing to external companies specialized in the carding and production of non-woven fabric.
Finally, it is once more treated with resin to acquire the properties and forms necessary for use in industrial contexts.
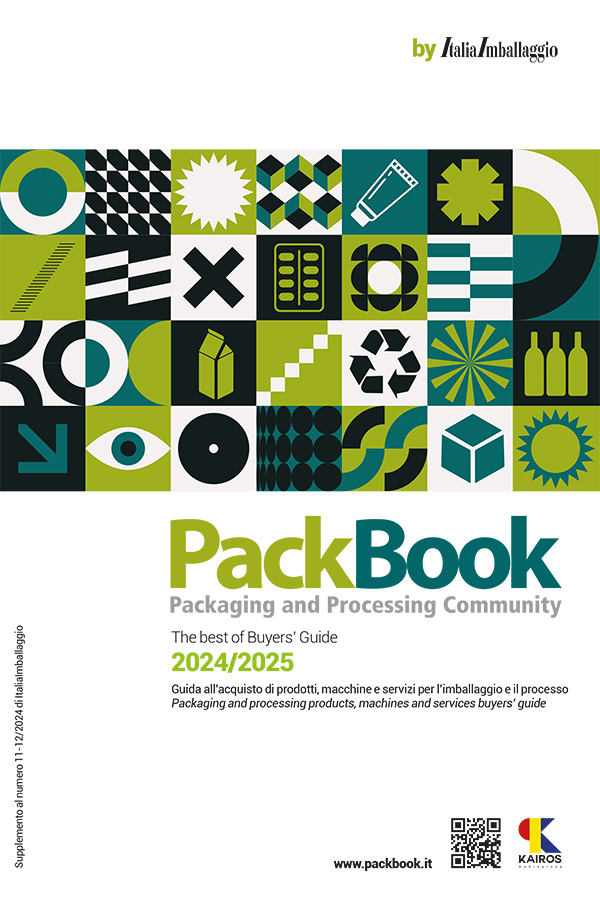