Supplier… of productivity and value
Folding, feeding, transport, robotics: DCM, reference partner for industrial packaging, measures its success in the satisfaction of its customers. And its evolution is marked by sustainability.
Quality, competence and innovation are just the words that best describe DCM, which has been operating for almost 50 years in the world of industrial packaging. Founded in 1974, DCM’s core business is the distribution of folding machines for the pharmaceutical, paper converting and graphic arts sectors in general. However, the ability to evolve and the desire to bring innovation in-house have meant that, over time, its portfolio has been enriched with new packaging solutions: in order to meet the different needs of customers today it also proposes robotic feeding, conveying, handling and conveying systems.
The corporate mission is very clear: helping customers to increase the productivity of their lines; this mission of DCM, is underpinned by its decades of experience in different sectors and the close working relationship with the companies represented: Guk, Kraus, Autonox Robotics and BVM Brunner.
Technological proposals at Interpack: a showcase of excellence
International leaders in paper folding
Over the years, DCM has acquired a unique experience in supplying and installing GUK products, famous all over the world for their practicality, sturdiness and reliability.
The formats produced by GUK machines are among the most varied, with folding lines reaching speeds of up to 600 pieces/min and guaranteeing higher quality of the finished product thanks to the consistency of the results and the use of unique and patented solutions.
Standard versions can be equipped with accessories and add-ons to further extend their capabilities, such as a vision system and automatic rejection to eliminate the risk of mix-ups. Thanks to Guk technology, millions of illustrative brochures are produced every day in Italy and this has led DCM to develop an original method so that the productivity of the machines is never compromised; in particular, the preventive and scheduled maintenance plan for the folding lines has become fundamental for the customers.
For this reason, to enable a constant monitoring, for its folding lines DCM has created the Mercury system to give optimum performance of tasks allowing Industry 4.0 criteria machine interconnection.

Dispensing, transportation and labelling
Kraus feeders are designed to work at industrial rates and are ideal for dispensing products at high speeds in various product sectors.
The lively focus on sustainability in recent years has led to the transformation of machines to accommodate the demand for environmentally friendly, “green” packaging. The increasingly frequent use of recyclable materials in the production of disposable cutlery, cards, trays and tubs has also led to changes in the technological solutions adopted for their singularization and distribution, carried out fully automatically on the production lines. The subject also closely touches the pharmaceutical sector, of which DCM boasts a very in-depth knowledge; and it is precisely through the know-how acquired in this area that DCM has created a new concept solution: the Brava family. Consisting of 3 different machines, it provides as a finished product a cardboard support that has 2 to 6 rows of cusps that, during packaging, go to accommodate products such as syringes, flacons and vials. Since Kraus is not only synonymous with feeding and conveying but also with labelling, another recent development proposed by DCM is the Labeljack system, which is characterized by a high cycle speed, readiness for Industry 4.0 and the management of labels of different formats.
The numerous processes developed for special lines and labelling systems have a primary role, especially for the high level of customisation that they can offer. Through integrated control with Labeljack, it’s possible to set up the language, interface and memory of the label format. The operating messages and warnings are visualized on the multi-touch colour display and the exclusive blocking mechanism and the simplicity of use guarantee easy handling and maximum precision and agility.

Independent robotic controller
The evolution of information technology and electronics has made it possible to develop new advanced industrial robots such as those under the Autonox Robotics brand, capable of performing almost any type of packaging and handling activity on products of different weights and sizes.
The entire range is controller independent and is composed of duopods, Delta robots from 3 to 5 axes and anthropomorphic robots from three to six axes, able to work with sustained cycles and to meet the different requirements for payload and working areas: from 0.5 to 350 kg and from 200 mm up to 2257 mm.
The standard versions are completed by the renewed Hygienic Design versions, to work in primary packaging with IP69K grade protection and other versions for lines with a layout for reduced productions. The mechanics distributed by D.C.M. are independent of the controller: this is a feature which has led various manufacturers to introduce this technology into their factories. The possibility of using a single software for the entire line, the absence of interfacing between machines and the breadth of the range make the Autonox robots the most flexible on the market so as to allow for their use in different sectors, from traditional packaging to additive manufacturing or metal working.
In recent years, as far as software is concerned, the need to simulate production processes and in particular to virtually test robots by means of a “digital twin” has grown increasingly. Always attentive to innovation and value creation, DCM has integrated into its offer the possibility of simulating the customer’s robotic application. Through virtual commissioning software, it proposes the right robotic sizing and test the feasibility of a project; this is a great technological advantage that, in most cases, can replace the physical testing part of the machine.
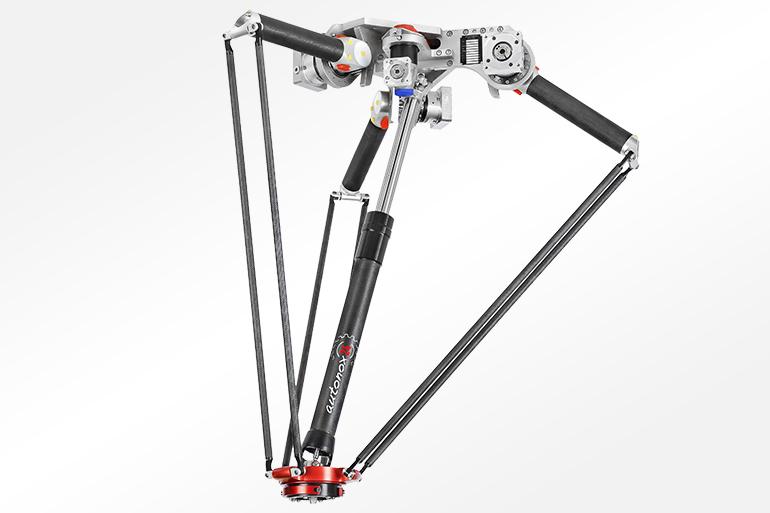
BVM Brunner “labelled” packaging
BVM Brunner-brand solutions include machines for packaging in film and in cardboard and paper: equipped with feeding, transportation and handling systems for the movement of products, they adapt to practically all types of goods, from food products to mail-order products, from textiles to their returns, from packages for the shipment of paper and multimedia products, to medicines and products for the home. The machines in the Comtex and Papertec series are mainly used in e-commerce. What distinguishes the Comtex series is the development of a solution for posting products in a wide range of formats without the need for adjustments and is suitable for companies of various dimensions. The packaging line can be integrated with additional options, such as the application of a shipment label. The Comtex 3G has been developed for managing flows of returns enabling the repackaging of articles returned by customers.
In the wake of the green transition and the need to replace plastic with paper, the Papertec series, on the other hand, has been developed, the alternative to packaging with cardboard and plastic for the automatic packaging of shipped articles, mainly textiles, in a kraft paper bag. The process makes it possible to save precious resources, warehouse space and outgoing goods, as well as disposal costs; from a pair of socks to a jacket, all products are packed completely automatically in a paper bag sealed on all sides with a shipment label.

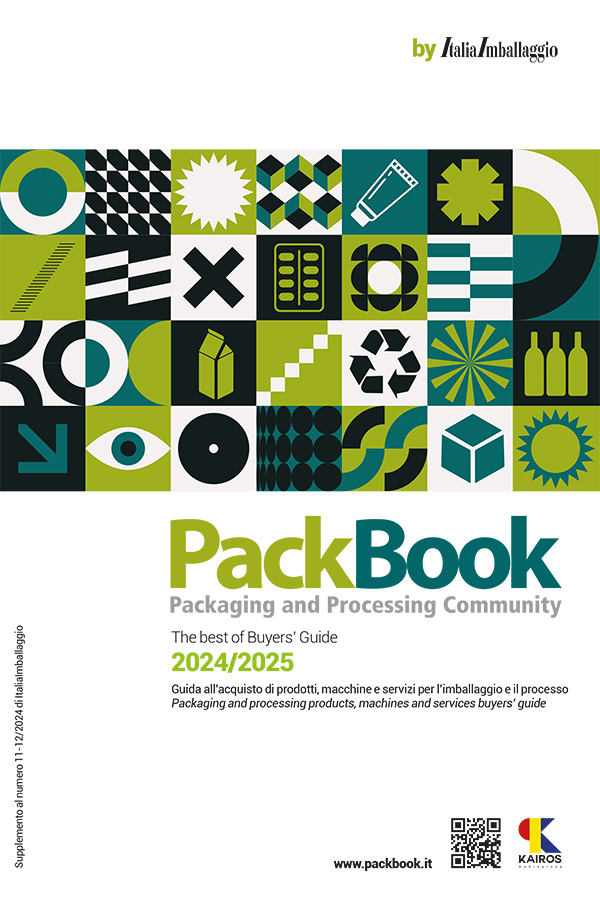