a-eye clearance technology
Developed by SEA Vision and ARGO Vision, it was shown in operation last May at Interpack. Here we are talking about the new “a-eye clearance” technology which, using AI, makes line clearance processes more efficient and safer than ever.
Usually performed before every lot change, clearance processes have a well-defined objective: to ensure that that equipment and the work areas used are clean and free of any object or residual material resulting from a previous production cycle, so as to avoid erroneous labelling or contamination of the finished products which would expose the company to costly product recalls. This procedure is therefore essential before the start of the production cycle for reasons linked to the maintenance of process safety, quality and efficiency: essential requisites required, moreover, by the pharmaceutical GMP standards.

Why traditional clearance is no longer sufficient
Despite the importance of the process, manual intervention is still required today on the part of operators for the performance of specific tasks and activities, with the consequent risk of human error. This risk is even higher considering the production rhythms of today’s market which requires, among other things, ever more frequent format changes on productions of small lots. The need for greater safety and more fluid processes underpins SEA Vision’s a-eye clearance product, developed starting from software and hardware components that facilitates – automating and digitalizing – the clearance procedures on packaging lines before a lot or product change.
A-eye clearance technology is, therefore, able to perform an automatic and accurate inspection of the packaging line work areas using industrial video cameras, intelligent sensors and – where necessary – manual scanners. This mix of combined controls has been designed to be more reliable than human control: detecting anomalies and providing feedback in real time, it makes it possible to improve operating efficiency and reduce line preparation times, also in conditions of poor light or in zones which are difficult to reach. In this way, the customer has a vision of the entire production line, something which is difficult to obtain using only the technical and visual abilities of their operators, no matter how attentive and expert they are.
Making use of Artificial Intelligence
A-eye clearance is guided by AI algorithms, implemented with the aim of automating the described procedures, so as to avoid errors and, as a consequence, increase the OEE of production lines, reducing the time necessary for format change.
Even production lines which, apparently, work in conditions of less than optimal lighting are made extremely efficient using AI algorithms, thanks to their ability to fully comprehend the situation and detect only real problems, evaluating each critical area in very diverse environmental conditions. The software performs checks on the image acquired using semantic segmentation: in other words, it creates an extremely accurate mapping of every single component on the line. Data Augmentation technologies make it possible, moreover, to multiply all the real data and collect a very large number of comparable models based on a few real images. We have, therefore, an extremely intelligent system that is also able to improve automatically, learning from its time series, so as to react always better to the wide range of variations that can occur during the production process.
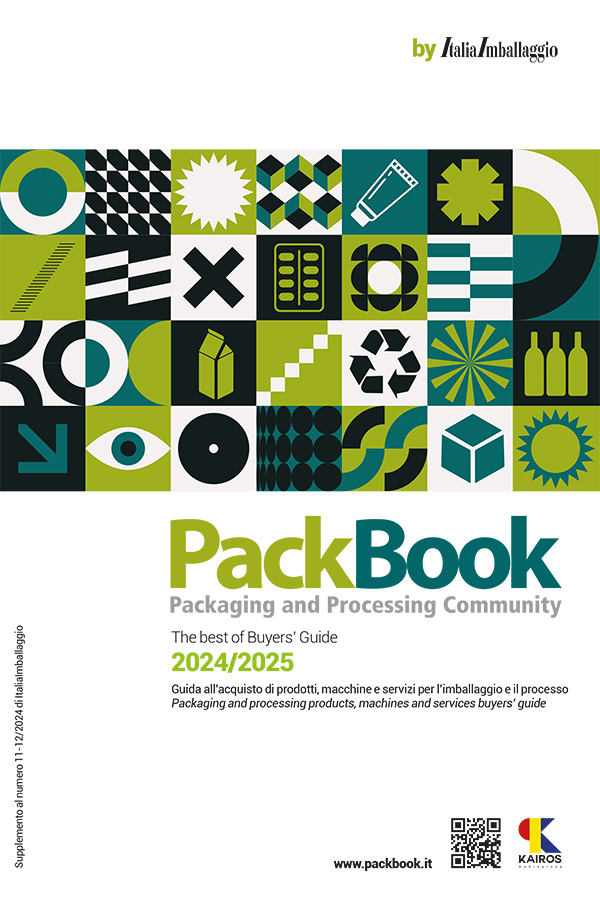