Robotized packaging for traditional biscuits
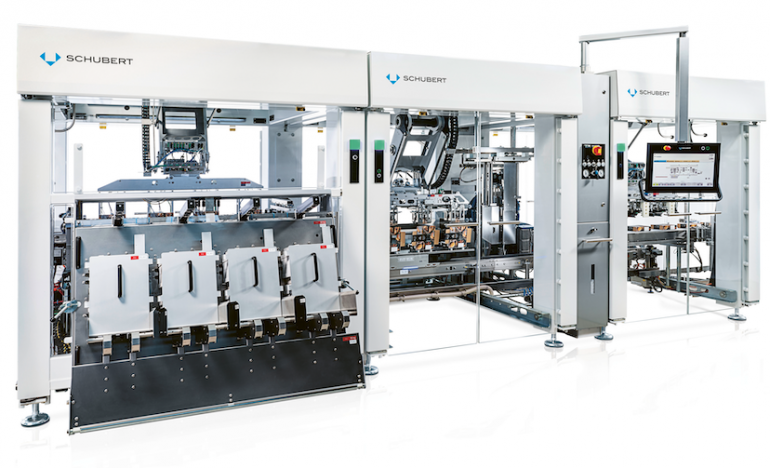
In order to package the semi-homemade biscuits of the Italian company Asolo Dolce, Gerhard Schubert has developed a TLM robotized system, also optimizing the secondary pack. The goal was achieved: a more efficient, flexible and faster packaging process to meet the new production requirements.
Asolo Dolce, a Veneto based traditional manufacturer of confectionery products - Cantuccini, Amaretti and other traditional specialties - for its packaging has favoured for may years flowpacks to keep them fresh and crunchy for a long time. Until recently, however, the treats were packaged in pre-glued cartons – an expensive and labor-intensive process that Asolo Dolce wanted to optimise due to increasing demand.
For an efficient modernisation of its packaging and process, the company turned to Gerhard Schubert, which not only supplied a modular robotized TLM plant designed ad hoc and with simplified format changeover, but also redesigned the design of the boxes, so as to make the entire process more flexible and economical.
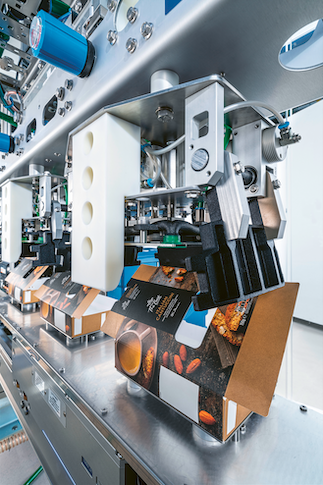
The choice of top loading. Biscuits produced with traditional semi-artisanal processes have an irregular shape, that gives each filled bag its own geometry. This characteristic presents a challenge for automated handling as part of the packaging process. Schubert team designed two carton formats as flat blanks and with two different heights in order to fill the cartons flexibly with bags weighing 150, 200 or 250 grams – all on a single machine.
To save Asolo Dolce time and money over the long term, the Schubert machine experts working with Area Sales Manager Dirk Andrich opted for the top-loading process, which is done through the top opening, the largest available, instead of the more common side loading.
In this way, the system not only works more quickly, but also more flexibly and reliably, because the robots responsible for the filling process can act independently of the height of the cartons.
The new packaging machine is responsible for automatic bag grouping, erecting and gluing the flat blanks, filling the cartons with Cantuccini flowpacks and then closing the filled cartons. The full output of 75 cartons per minute is always guaranteed, regardless of the format. During the final approval process, the tests conducted under production conditions demonstrated an efficiency level of at least 98 per cent.
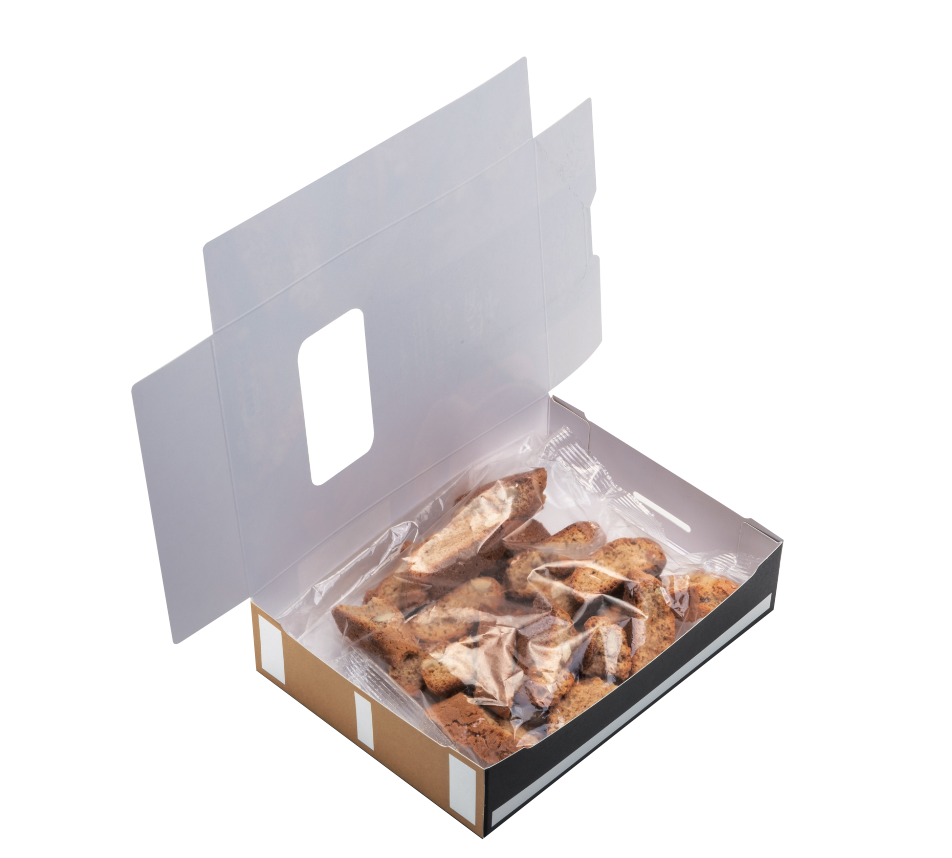
Transmodul transport robots. One of the technical highlights of the modern line is the Transmodul. The transport robot - an in-house Schubert development - seamlessly links the individual steps in the machine’s packaging process. The machine erects the flat blanks and places them onto the Transmodul, which brings the prepared cartons to the filling station. As soon as the grouped bags with the biscuits and the cartons are aligned, the robot places the flowpacks into the packages. The Transmodul then moves the cartons to the closing station.
Flexible format change. In the event of a format changeover, only the magazine plate for the carton blanks needs to be changed, as the packaging machine’s filling tool is equipped with specially adapted suction cups. It automatically adjusts to the new pouch format via a spreading motion. This makes the changeover very quick and easy for the machine operator – and production can proceed quickly.
And in the future, further formats will be possible with the new packaging machine as well.
Thanks to its increased efficiency, cost savings, reliability and ease of use, the Schubert solution has resulted in a high level of satisfaction at Asolo Dolce.
In order to integrate the more efficient packaging of the Cantuccini into the entire production process, the Schubert experts also took into account a uniform logistics concept that extends all the way through to the palletization.