Schubert: towards a green, digital future
Sustainability, robotics and digitalisation are the biggest challenges facing the packaging industry. Gerhard Schubert is responding by developing cutting-edge solutions based on its established expertise.
Mission Blue Sustainability Initiative
Sustainability is firmly anchored in the corporate culture of the German packaging manufacturer Gerhard Schubert, which has now defined four fields of action with its Mission Blue Sustainability Initiative: sustainable corporate management, climate-neutral production, environmentally friendly machines and services, and sustainable packaging.
The objectives Schubert is pursuing with Mission Blue include becoming a climate-neutral company and supporting its customers with more sustainable production. As well as actively advancing future-proof packaging solutions that make use of more environmentally friendly materials and resource-saving blanks, Schubert is laying the foundations for sustainable packaging with the flexibility and state-of-the-art robot technology used on its packaging machines and lines. Schubert offers its services to customers as a partner both in the design of technologies best suited to individual requirements and in the selection of the most environmentally friendly materials, which are meticulously tested at the Schubert Technikum centre to ensure that they are compatible with the machine.
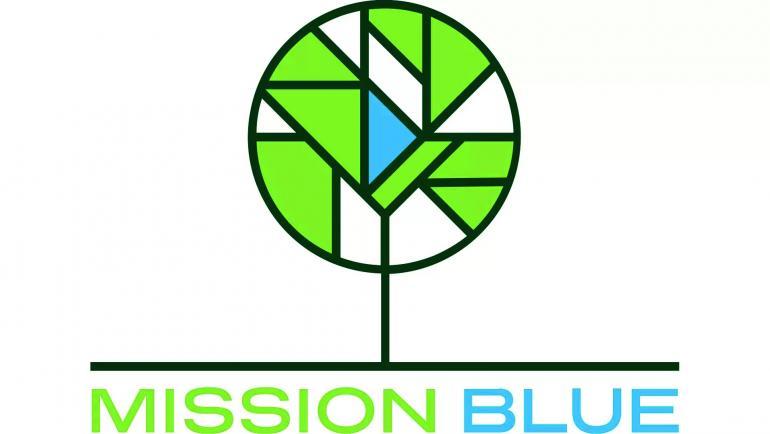
Robotics and flexibility in a traypacker
The ability of robotics to achieve maximum production flexibility is evident in the Schubert branded traypacker, which seals hamburgers in a transparent pack and then loads them into cardboard trays with separate lids. The machine can pack products in three different packaging formats from 4-count to 16-count packaging. In the future, as many as 14 different packaging formats will be available. A variety of packing configurations can be created by flexibly combining single and multiple packs. Single trays can either be glued next to each other or stacked to create a double tray. A completeness check also ensures that only complete trays filled with flawless products are sealed. As is now the case with every Schubert machine, the traypacker’s two F4 pick & place robots are also equipped with 3D printed format parts. The F4 picker tool for transferring the products as well as the lidding tools are each fitted with 3D printed parts, which the customer can call up as a print job via the PARTBOX streaming platform and produce autonomously using the new PARTBOX printer from Schubert.
PARTBOX for 3D printing
PARTBOX is a highly efficient 3D printer that enables manufacturers to produce components directly in their own facilities. This enables defective parts to be replaced quickly and new formats for modified products to be produced in-house. Schubert also supplies the PARTBOX Black filament as a suitable printing material. The material is food-grade and has good mechanical properties and high temperature resistance. The high print quality is ensured by meticulously designed components and precise dosing of the filament.
