Marchesini Group in the Cosmopack SMART Area
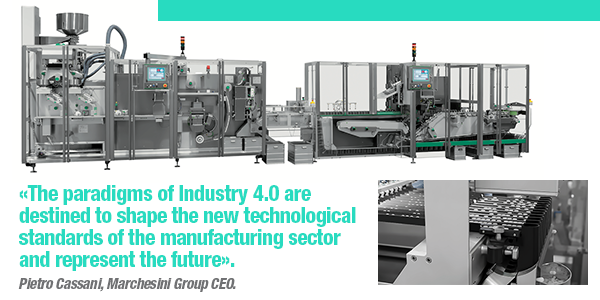
Industry 4.0: reflections emerged from the comparison with some protagonists of the SMART area of Cosmopack. The word goes to Pietro Cassani, CEO of Marchesini Group (Supply of complete lines and machines for packaging pharmaceutical and cosmetics products).
«The paradigms of Industry 4.0 are destined to shape the new technological standards of the manufacturing sector and represent the future. At Marchesini,, we think it is time to move from theory to practice. This is why - Pietro Cassani (Marchesini Group CEO) begins - we started out a long way back basing ourselves on a clear and targeted strategy, which is bearing fruit: on the one hand acquiring companies of excellence specialized in each of these key themes, on the other, coordinating and centralizing these activities at a higher level, at the heart of the Marchesini Group. This allows us to optimize resources, enhancing the skills of each reality, while achieving the highest levels of efficiency».
From traceability to efficiency. The path mentioned by the manager started with the acquisition of Sea Vision, a company specializing in technologies for traceability in the pharmaceutical sector and beyond. «This is a crucial and very current topic in a market that requires transparency and strict guarantees on the non-counterfeiting of products, and more generally, on their origin and quality. This is why today track and trace, in addition to being indispensable in the pharmaceutical industry, is also viewed with the utmost interest by food and cosmetics manufacturers».
Traceability passes, first of all, through the digitalisation of vision and quality control systems, which must be able to record the surveys carried out on an IT level. «So here is the second and decisive step taken with Sea Vision, concerning data collection and processing. Sea has developed software that, in addition to guaranteeing non-counterfeiting, monitors and collects data relating to online processes - productivity, consumption, efficiency and any interruptions in production ... and processes them by providing operators with useful indicators to better manage the same».
From predictive maintenance to neural networks. Marchesini addressed the issue by exploiting the expertise of Proteo (company acquired in 2018, Ed.), with which it is working on two fronts. «First of all, to design and assemble ad hoc sensor on machines, capable of monitoring, during production processes, some critical indicators, such as the level of vibrations, noise and heat: in this case, the surveys enable the identification of any anomalies that often do not lead to immediate breakdowns, but could cause them if they continue over time.
In addition to the "hardware", Proteo also programs the software that collects the data relating to the surveys carried out, comparing them with the normal operating ranges set during calibration, to identify and signal the possible overstepping of the critical thresholds. The system, which processes millions of pieces of information per second, and therefore requires a suitable architecture, allows timely intervention on the lines with targeted maintenance or simple adjustments to the operating parameters, thus avoiding more serious problems and unplanned and prolonged production stops».
In practice, it is a matter of automating and programming upstream a series of operations, optimizing the management to the full - once again - in terms of efficiency and productivity ... And following this guideline, Cassani recalls that «the next step is the implementation of artificial intelligence, a technological challenge on which we are placing a lot. To achieve this it is essential that all the applications I have mentioned - traceability, data collection, predictive maintenance - are integrated with each other.
From integration, self-learning is born: the system itself, processing the data, can also "learn" independently which operations to perform and when, overlooking those that can be defined as "false positives". In this way, human intervention is only necessary in event of real need. For developments in this technological field, we are actively collaborating with various Italian universities, aiming at the use of neural networks, in turn borrowed from the experiential mechanisms of the human brain.
The neural model makes it possible to start and make the lines operational in a very short time, as in the case - exemplifies Cassani - of the calibration of pharmaceutical machines: if executed manually it is a laborious operation, but thanks to the neural networks applied to self-learning systems, the whole setup of a line requires much less time».
Dalle parole ai fatti... passando per la cyber security. These technologies represent the state of the art and the future of the industrial world, and it is no longer possible to do without them.
So is the current transition no return?
«Of course, it is proceeding at such a speed that those who today do not commit themselves with due energy and due investments will remain " cut off ". As for Marchesini, our know-how in the field of artificial intelligence on applications and lines is also a reality: in fact we have already developed a blister packaging line on which, for the first time, the paradigms of the fourth technological revolution coexist, from the interconnection of systems to machine learning, up to big data analysis. We have created a complex "ecosystem", where cameras coexist for a multivision control of the shape, thickness and color of the tablets, a recognition system for the active principle NIR (Near Infrared System), but also a SCADA system - which gives the operator a complete check of the mechanical and functional health status of the machine thanks to a constant tracking of quality parameters - as well as a predictive maintenance system able to recognize any type of mechanical error and suggest scheduled maintenance actions. Downstream, the plant is completed by a labeler with weight control and a horizontal cartoner for track & trace».
To overcome the delicate (but plausible) distrust of users to make sensitive production data accessible, Marchesini has chosen to equip the lines with some digital features to collect and process information relating to non-counterfeiting, to the operation of the machines to indicate any interventions maintenance or adjustments to be performed.
«However, these data - adds Cassani - are not intended for us, but for the customer, who can choose, as the case has it, whether and which data to keep confidential within the local network of the plant or, if necessary, share them with the supplier, allowing connection to the system to provide assistance, this even remotely».
Finally... from costs to benefits. If we think of the incidence of artificial intelligence on the final price of the line, we can see that the hardware devices used to equip the machines to integrate the 4.0 functions - cameras, sensors, etc. - represent a marginal investment compared to the global cost. «What affects us the most is the software infrastructure, the development of which requires more specific and advanced skills.
However, if we consider the benefits deriving from the adoption of 4.0 technologies in terms of efficiency, simplification of the operator’s work, safety, failure reduction and production continuity, I believe I can say that such an investment not only guarantees a rapid return, but it should also be considered a priority and fundamental to remain competitive and keep pace with the productivity standards of the global world. And this applies in every area: the modernization of production infrastructures is a crucial issue, which concerns not only the pharmaceutical or cosmetic industry, but the entire economic fabric of the country.
And how do you improve the efficiency of a system? "Says Cassani. «Investing in "knowhow”, analyzing processes in a capillary way, collecting data and processing it, to understand where and how it can be optimized. Industry 4.0 means this to us».