Between new markets and customization
Technical flexibility, an approach to the market that expresses concreteness and foresight for Volpak, part of Coesia Group: with an established presence in the food and non-food sectors, it is thinking about repositioning the Enflex brand in the pharma & healthcare sphere. Research continues on new materials to optimize machine operation and attention to service.
Costanza Candi, Luciana Guidotti
Present in 130 countries, with more than 6,000 machines installed worldwide and 270 employees operating in the production plant in Spain, Volpak deploys a consolidated know-how in the design and construction of automatic machines for packaging in pre-formed flexible pouches of liquid and solid products (from home & personal care to food).
Met at the fair, Francesco Busquets (Head of Sales & Marketing Volpak) explained how the company is rethinking its business, in line with the strategies put in place by the Coesia Group: two large spaces at IPACK-IMA and Pharmintech, where all the companies of the Bologna-based industrial structure were hosted - according to their specialization and target sectors.
Entering Volpak at the height of the pandemic, when in-person events were suspended, Busquets has words of praise «for this great specialized fair and for the number of visitors interested in our solutions. We are present with two brands, Volpak and Enflex, traditionally dedicated to the same market but with different technical vocations in terms of speed and performance. Today, with the Enflex brand, we are oriented to the production of flat sachets and stick packs for pharma.
An example of this is the Enflex - F11 DX on display at the fair: originally created only for pharma, however, we have decided on a focus so that it can also be used for applications in the healthcare, nutraceutical, and cosmetic markets. The rebrand we are working on is also being carried forward with a portfolio review, consisting of generic machines that we want to adapt to pharma, to build a dedicated offering for that specific market. That is why the machines we presented at the fair are GMP and CFR 21 Part 11 (Code of Federal Regulation) compliant, allowing product traceability and adhering to international standards. So we are talking about, a full-fledged pharmaceutical machine, redesigned and built on the feedback we have received from our customers in the industry».
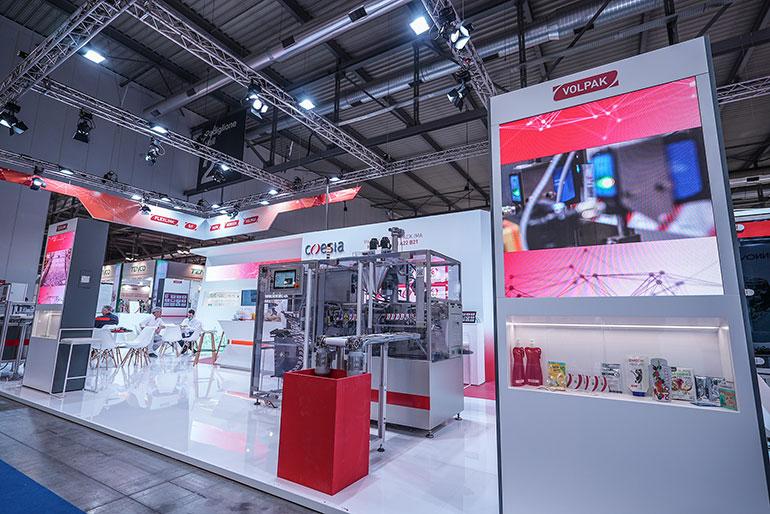
«As for Volpak - Busquets continues - it successfully presides over the pouch sector. We specialize in the design and construction of horizontal machines for forming and filling flexible packaging, and we have developed a wide range of solutions to support different needs in the FMCG sector, from high to low speed, with great flexibility in terms of formats: from the flat pouch to doypack».
Winning strategy: materials R&D and collaboration
The variety of markets and technological solutions offered by Volpak, a Coesia Company, look at contexts where materials play a strategic role, especially if we think of flexible packaging «a packaging solution - Busquets points out - still largely dominated by plastic, which guarantees excellent shelf life and, consequently, a reduction in food waste. Given the increasing world population, if we want everyone to be reached by safe food and products, we have to use the right packaging. Plastic combined with the way the industry is moving toward recyclability and green products is perhaps still the most sustainable in terms of carbon footprint and energy consumption».
So whether it is monomaterial film, non-laminated or compostable, research into new materials presents a major challenge to machine manufacturers. New plastic-based materials, in fact, require strengthening R&D to solve the technical issues that innovative materials raise.
«In Volpak - Francesc Busquets recounts further - we have always had an R&D laboratory, but three years ago we decided to invest additional resources and created the PouchLab, a unique place where customers and material manufacturers can experiment with the behavior and evolutions of different types of materials, while gathering important information on packaging performance. It is the place where we focus our expertise on materials and automation, but it is above all a space made available to customers and suppliers to develop recyclable or environmentally friendly pouches».
Machines and instrumentation of excellence are thus at the service of those who want to improve the quality and sustainability standards of their packaging, for example by optimizing its size or testing the use of alternative materials (different types of film, paper-based or monomaterial). But in addition to testing the performance of different film types, new closure and re-opening systems applied to pouches can be developed there.
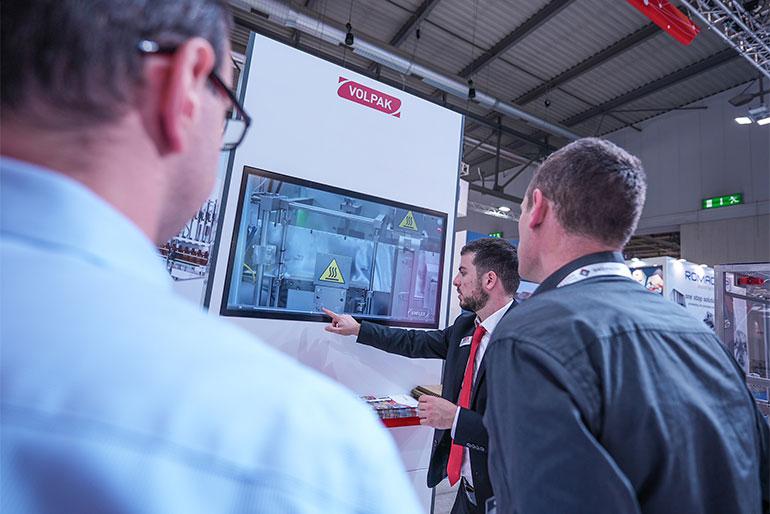
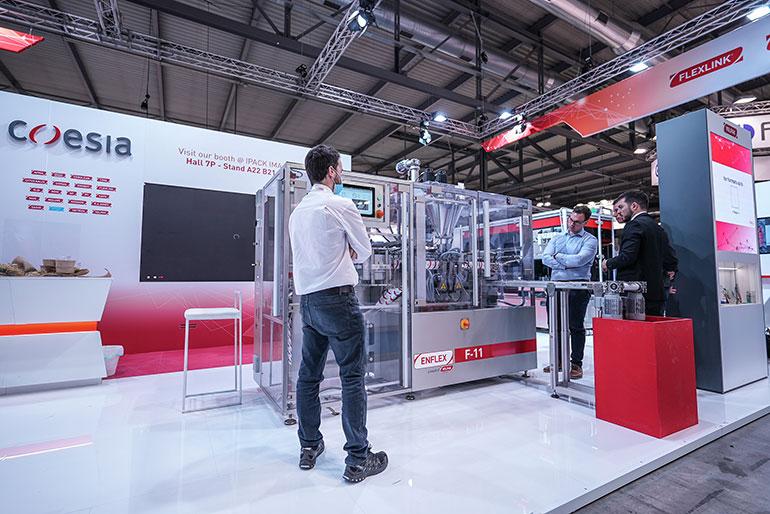
«The PouchLab is working at full speed, to the point of requiring a doubling of capacity and the opening of a dosing lab devoted to pouching; we work with customers and film manufacturers from all over the world, including Asia and the United States come to us to test their materials in development».
This is a winning strategy that responds to the ever-increasing demand for green solutions in materials as well, with ever-changing technical challenges that manufacturers are called upon to respond to, equipping themselves to provide the best solutions for their customers.
Going beyond flexibility
«The change in the industry is substantial - Busquets says - and the only way is through collaboration, because the interests of all parties involved, machine manufacturers, material manufacturers, customers, and end consumers, ultimately coincide. Think of the producers of materials such as caps and films, customers, and machine manufacturers who have to adapt to the new standards that will come into effect in 2030. The major market players have decided to move this forward to 2025, imposing a step-by-step march. This is a major change, because the multi-laminate material already tested, was built to give great protection to the product. But now a new variable comes in, 100 percent recyclability, effectively mandating the single-material, with completely different behavior and machinability issues. Issues on which we have made great progress thanks to constant research, which allows us today to include monomaterial among the standards for all our machines, new and installed. A systems upgrade that, moreover, has not imposed a complete replacement of technology on our customers».

The European Commission’s setting of new sustainability standards can be seen as a constraint, but also as an opportunity to develop new markets.
An approach that Volpak has adopted, thus opening up new business opportunities, particularly with retrofitting, to adapt machines to the requirements imposed by the new materials. This is a difficult market, where customization is one of the keys to meeting customer demands, and where innovation and quality go hand in hand to offer a service that includes technical upgrading even for older machines. Volpak thus applies a concept of customization that, when put into a system, brings benefits to all customers, albeit starting by listening to each of them.
«Let’s say we build many products around the customer - he continues - to cover requests such as retrofitting, remote services, operator training. For each specific request, we have tried to create a dedicated sector that would bring the experience gained to the service of the system.
If we look at flexibility, for example, in our industry it is made to coincide with the changeover, which is quick and easy to do, but it is not the only issue that requires rapid adaptation to new demands. Even in industries like ours, for example, volume fluctuations are important, imposing logic typical of mass customization. Flexibility today also means putting customers in a position to strengthen their production capacity, expanding machines without going so far as to buy new ones. A result possible thanks to modular design».
Volpak’s news does not stop there. Having filed away Ipack Ima, in fact, the next stop is Pack Expo Chicago, where new machine features will be presented.
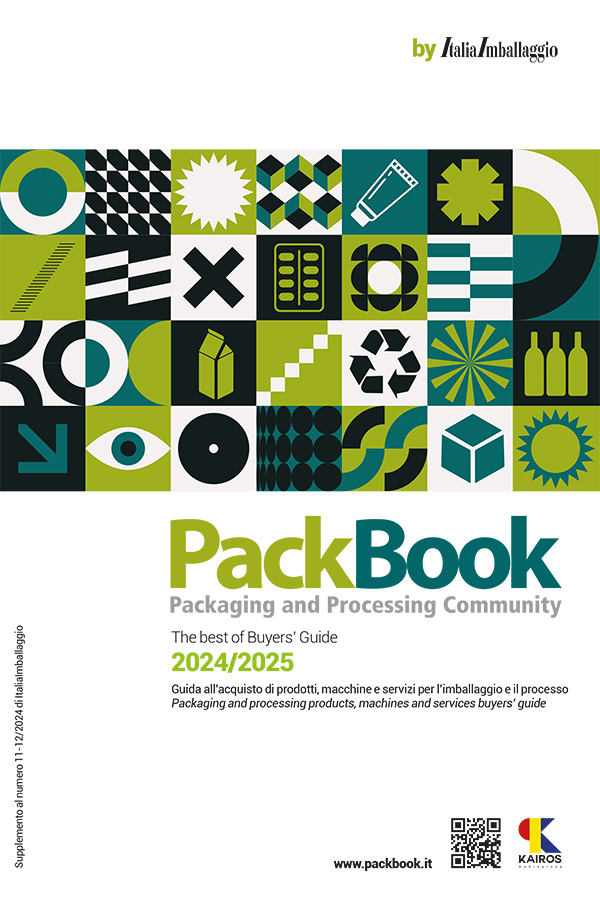