Automation enhances business
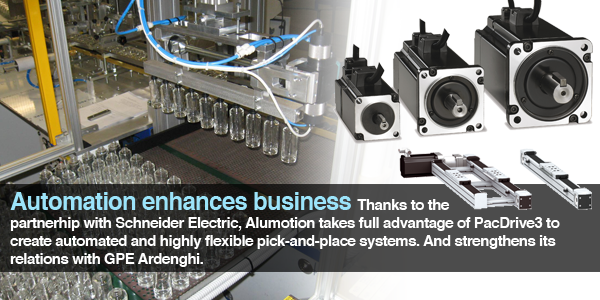
Thanks to the partnerhip with Schneider Electric, Alumotion takes full advantage of PacDrive3 to create automated and highly flexible pick-and-place systems. And strengthens its relations with GPE Ardenghi.
The history of Alumotion starts from Atti Srl, a Cernusco sul Naviglio (MI) based company set up in the eighties as a distributor of mechanical transmission components. Over the years it has guided a major evolution of its business, presenting itself as a technical consultant and systems integrator, then expanding its activities in the electrical sector with the supply of mechanical components for the transmission of the motion powered by servodrives and brushless motors ...
The next step was the creation of a technical department and the further organization into two new divisions, dedicated respectively to the processing and distribution of aluminium and automation area in which the company also proposes, in addition to electrical parts, programmable solutions such as PLC and motion control.
Following the rapid growth of the first of two new fields, Atti founded Alumotions, a separate company focused on the Italian market and on the import of products from abroad. And it is here that relations with Schneider Electric were consolidated. Alumotion, in fact, has become the exclusive distributor of Schneider Electric’s "linear motion" solutions and is active in the production of single modules and Cartesian combinations of linear guides.
For these products, which can be used together to form multi-axial solutions, including rotation, the parent company Atti provides the motion part, integrating Schneider Electric motion control components.
Thus a successful and complete partnership has been created, the result being the creation of a Cartesian robot programmed and installed at GPE Ardenghi, the Bergamo based manufacturer of screenprinting machines. The experience of Alumotion in the automation field, combined with the choice of PacDrive3, the innovative automation solutions featuring data transmission protocols based on Ethernet and a highly flexible and safe development environment, have led to the creation of a successful blend of technology.
A made-to-measure pick-and-place
GPE Ardenghi has a particular specialization: it designs and produces machines that can print on any type of object and in particular caters for the gadget and cosmetics market.
«On demand from our customers - clarifies GPE Ardenghi’s Ingegner Mario Baietti - we began to automate our systems, that at the start were essentially mechanical».
Their latest creation involves a pick-and-place offload robot, programmed to pick up glass bottles at the end of the screenprinting machine operations line and place them in a set pattern on trays ready to be placed in print drying ovens.
To develop and add this component, the Bergamo based company turned to Alumotion, a Schneider Electric partner for Cartesian and robotic motion. The result has been a complex modular automation system formed by SoMachine Motion software, the SH3 motor drive, the mechanical part of the linear guides up to the Lexium62 drive module that comes with PacDrive3, where technology and innovation take pride of place.
The machine designed by GPE Ardenghi includes an indexed belt to accommodate the positioning of the bottles and to facilitate the printing process. The need was to take the objects and place them on a belt, staggered along a diagonal line and with a rhythm phased to the subsequent stage of fixing of the screenprinting. The biggest challenge for Alumotion was to synchronize the two components: the receival of the starting signal from the PLC to then proceed with the gripping, turning and repositioning operation.
The motion was managed thanks to PacDrive3, which includes a robotics software library that provides already preset movements, facilitating the programming of functions such as the interrupt signals and rephasing operations.
Onus on productivity. Approximately 70% of the process was hence set before the modules developed by Alumotion were integrated on the machine devised by GPE Ardenghi, allowing an unprecedented time to market.
Indeed the available software libraries enabled best possible interfacing, avoiding consequences such as the vibrations which, in case of error in constructing the trajectory, would be transmitted to the rest of the machinery. Thanks to this preliminary stage the operations required during on site installation were reduced, much to the satisfaction of the customer. Lastly, crowning the mechatronic integration - which enabled the robot structure being made in aluminium, the implementing and the scaling of the motors and influenced the construction of the circuit board and control panel - Alumotion customized the software to the specific needs of GPE Ardenghi’s machine, with positioning and interfacing done via the original start-up and stop signals.
«Basically we were able to increase the machine’s output up to 5,000 pieces per hour compared to 2,500 in the past» Baietti states. «Previously, in fact, the operation was done manually by a person, who positioned the vials individually. In addition, today, the system enables a uniform distance to be kept between the pieces, making the most of the space for an overall optimal yield. And if the cosmetics producer for which we have managed the implementation is pleased with the sizeable increase in figures, for our part we are satisfied with the qualitative leap made with the support of Alumotion: we have gained a considerable advantage, primarily because we can now offer our customers automated systems which ensure a drastic reduction in labour costs, and secondly because we can open up to a new market».
The advantage of simplification. The chain of benefits is due to the efficiency of solutions using PacDrive3. Indeed, the integration of a multiaxial robot control system on a single hardware platform enables reduced complexity, offering a single software environment in which the various components (logic, motion and IT) can be integrated, with the relative cost cutting deriving from a heterogeneous system.
Furthermore, the Schneider Electric motion solutions mean system integrators such as Alumotion can count on a ready-to-use control component without having to design and program complex automation functions accorded to each specific use.
The added value of Alumotion has been the design of the different components to meet the actual needs of the customer and the provision of a highly engineered modular system; its offering itself to GPE Ardenghi as a sole supplier for all the components included in the system has simplified all stages, from design to testing up to start-up of production of the robot. And now GPE Ardenghi is in a position to propose automated systems capable of handling any type of object on its own print machines and can count on a highly flexible and easily integratable technology.